Logística/Imprimir: diferenças entre revisões
[edição não verificada] | [edição não verificada] |
criação automática da versão para impressão |
Trocando o conteúdo da página por "{{subst:Versão para impressão automática}} {{AutoCat}}" |
||
Linha 1: | Linha 1: | ||
{{Versão para impressão |
{{Versão para impressão|{{BASEPAGENAME}}|{{BASEPAGENAME}}/Imprimir}} |
||
__FORCETOC__ |
|||
=Capa= |
|||
{{:Logística/Capa}} |
|||
=Prefácio= |
|||
{{:Logística/Prefácio}} |
|||
=Introdução= |
|||
{{:Logística/Introdução}} |
|||
=Técnicas de previsão= |
|||
{{:Logística/Técnicas de previsão}} |
|||
=Técnicas de previsão/Séries temporais e dados transversais= |
|||
{{:Logística/Técnicas de previsão/Séries temporais e dados transversais}} |
|||
=Técnicas de previsão/Representações gráficas= |
|||
{{:Logística/Técnicas de previsão/Representações gráficas}} |
|||
=Técnicas de previsão/Estatísticas univariadas, bivariadas e autocorrelação= |
|||
{{:Logística/Técnicas de previsão/Estatísticas univariadas, bivariadas e autocorrelação}} |
|||
=Técnicas de previsão/Medidas de precisão da previsão= |
|||
{{:Logística/Técnicas de previsão/Medidas de precisão da previsão}} |
|||
=Técnicas de previsão/Intervalo de previsão= |
|||
{{:Logística/Técnicas de previsão/Intervalo de previsão}} |
|||
=Técnicas de previsão/Estimativa dos mínimos quadrados= |
|||
{{:Logística/Técnicas de previsão/Estimativa dos mínimos quadrados}} |
|||
=Técnicas de previsão/Transformações e ajustamentos= |
|||
{{:Logística/Técnicas de previsão/Transformações e ajustamentos}} |
|||
=Técnicas de previsão/Decomposição de séries temporais= |
|||
{{:Logística/Técnicas de previsão/Decomposição de séries temporais}} |
|||
=Técnicas de previsão/Princípios= |
|||
{{:Logística/Técnicas de previsão/Princípios}} |
|||
=Técnicas de previsão/Médias móveis= |
|||
{{:Logística/Técnicas de previsão/Médias móveis}} |
|||
=Técnicas de previsão/Médias móveis/Média móvel simples= |
|||
{{:Logística/Técnicas de previsão/Médias móveis/Média móvel simples}} |
|||
=Técnicas de previsão/Médias móveis/Média móvel centrada= |
|||
{{:Logística/Técnicas de previsão/Médias móveis/Média móvel centrada}} |
|||
=Técnicas de previsão/Médias móveis/Média móvel ponderada= |
|||
{{:Logística/Técnicas de previsão/Médias móveis/Média móvel ponderada}} |
|||
=Técnicas de previsão/Alisamento local de regressão= |
|||
{{:Logística/Técnicas de previsão/Alisamento local de regressão}} |
|||
=Técnicas de previsão/Decomposição clássica= |
|||
{{:Logística/Técnicas de previsão/Decomposição clássica}} |
|||
=Técnicas de previsão/Métodos do Census Bureau= |
|||
{{:Logística/Técnicas de previsão/Métodos do Census Bureau}} |
|||
=Técnicas de previsão/Decomposição STL= |
|||
{{:Logística/Técnicas de previsão/Decomposição STL}} |
|||
=Técnicas de previsão/Alisamento exponencial= |
|||
{{:Logística/Técnicas de previsão/Alisamento exponencial}} |
|||
=Técnicas de previsão/Regressão simples= |
|||
{{:Logística/Técnicas de previsão/Regressão simples}} |
|||
=Técnicas de previsão/Regressão múltipla= |
|||
{{:Logística/Técnicas de previsão/Regressão múltipla}} |
|||
=Técnicas de previsão/Métodos ARIMA de Box-Jenkins= |
|||
{{:Logística/Técnicas de previsão/Métodos ARIMA de Box-Jenkins}} |
|||
=Técnicas de previsão/Modelos avançados de previsão= |
|||
{{:Logística/Técnicas de previsão/Modelos avançados de previsão}} |
|||
=Técnicas de previsão/Previsão a longo prazo= |
|||
{{:Logística/Técnicas de previsão/Previsão a longo prazo}} |
|||
=Técnicas de previsão/Dinâmica de grupo= |
|||
{{:Logística/Técnicas de previsão/Dinâmica de grupo}} |
|||
=Técnicas de previsão/Intenções= |
|||
{{:Logística/Técnicas de previsão/Intenções}} |
|||
=Técnicas de previsão/Opinião de peritos= |
|||
{{:Logística/Técnicas de previsão/Opinião de peritos}} |
|||
=Técnicas de previsão/Opinião de peritos/Método Delphi= |
|||
{{:Logística/Técnicas de previsão/Opinião de peritos/Método Delphi}} |
|||
=Técnicas de previsão/Análise conjunta= |
|||
{{:Logística/Técnicas de previsão/Análise conjunta}} |
|||
=Técnicas de previsão/Análise conjunta/Pesquisa de mercado= |
|||
{{:Logística/Técnicas de previsão/Análise conjunta/Pesquisa de mercado}} |
|||
=Técnicas de previsão/Análise conjunta/Pesquisa de mercado/Pesquisa qualitativa= |
|||
{{:Logística/Técnicas de previsão/Análise conjunta/Pesquisa de mercado/Pesquisa qualitativa}} |
|||
=Técnicas de previsão/Análise conjunta/Pesquisa de mercado/Pesquisa quantitativa= |
|||
{{:Logística/Técnicas de previsão/Análise conjunta/Pesquisa de mercado/Pesquisa quantitativa}} |
|||
=Técnicas de previsão/Metodologia bootstrap= |
|||
{{:Logística/Técnicas de previsão/Metodologia bootstrap}} |
|||
=Técnicas de previsão/Analogias= |
|||
{{:Logística/Técnicas de previsão/Analogias}} |
|||
=Técnicas de previsão/Extrapolação= |
|||
{{:Logística/Técnicas de previsão/Extrapolação}} |
|||
=Técnicas de previsão/Redes neuronais= |
|||
{{:Logística/Técnicas de previsão/Redes neuronais}} |
|||
=Técnicas de previsão/Previsão baseada em regras= |
|||
{{:Logística/Técnicas de previsão/Previsão baseada em regras}} |
|||
=Técnicas de previsão/Sistemas periciais= |
|||
{{:Logística/Técnicas de previsão/Sistemas periciais}} |
|||
=Técnicas de previsão/Integração, ajustamento e combinação= |
|||
{{:Logística/Técnicas de previsão/Integração, ajustamento e combinação}} |
|||
=Sistemas de informação= |
|||
{{:Logística/Sistemas de informação}} |
|||
=Sistemas de informação/Introdução= |
|||
{{:Logística/Sistemas de informação/Introdução}} |
|||
=Sistemas de informação/Custo logístico= |
|||
{{:Logística/Sistemas de informação/Custo logístico}} |
|||
=Sistemas de informação/Custo logístico/Introdução= |
|||
{{:Logística/Sistemas de informação/Custo logístico/Introdução}} |
|||
=Sistemas de informação/Custo logístico/O custo logístico e a economia= |
|||
{{:Logística/Sistemas de informação/Custo logístico/O custo logístico e a economia}} |
|||
=Sistemas de informação/Custo logístico/Impacto do desenvolvimento de novas tecnologias no custo logístico= |
|||
{{:Logística/Sistemas de informação/Custo logístico/Impacto do desenvolvimento de novas tecnologias no custo logístico}} |
|||
=Sistemas de informação/Custo logístico/O número de armazéns do sistema logístico= |
|||
{{:Logística/Sistemas de informação/Custo logístico/O número de armazéns do sistema logístico}} |
|||
=Sistemas de informação/Custo logístico/Factores que afectam o custo logístico= |
|||
{{:Logística/Sistemas de informação/Custo logístico/Factores que afectam o custo logístico}} |
|||
=Sistemas de informação/Custo logístico/Factores que afectam o custo logístico/Competitividade= |
|||
{{:Logística/Sistemas de informação/Custo logístico/Factores que afectam o custo logístico/Competitividade}} |
|||
=Sistemas de informação/Custo logístico/Factores que afectam o custo logístico/Produto= |
|||
{{:Logística/Sistemas de informação/Custo logístico/Factores que afectam o custo logístico/Produto}} |
|||
=Sistemas de informação/Custo logístico/Factores que afectam o custo logístico/Localização= |
|||
{{:Logística/Sistemas de informação/Custo logístico/Factores que afectam o custo logístico/Localização}} |
|||
=Sistemas de informação/Custo logístico/Análise do custo logístico total= |
|||
{{:Logística/Sistemas de informação/Custo logístico/Análise do custo logístico total}} |
|||
=Sistemas de informação/Custo logístico/Outros custos relacionados com a logística= |
|||
{{:Logística/Sistemas de informação/Custo logístico/Outros custos relacionados com a logística}} |
|||
=Sistemas de informação/Custo logístico/Modelos de optimização do custo logístico= |
|||
{{:Logística/Sistemas de informação/Custo logístico/Modelos de optimização do custo logístico}} |
|||
=Sistemas de informação/Processamento de encomendas= |
|||
{{:Logística/Sistemas de informação/Processamento de encomendas}} |
|||
=Sistemas de informação/Processamento de encomendas/Preparação da encomenda= |
|||
{{:Logística/Sistemas de informação/Processamento de encomendas/Preparação da encomenda}} |
|||
=Sistemas de informação/Processamento de encomendas/Transmissão da encomenda= |
|||
{{:Logística/Sistemas de informação/Processamento de encomendas/Transmissão da encomenda}} |
|||
=Sistemas de informação/Processamento de encomendas/Atendimento da encomenda= |
|||
{{:Logística/Sistemas de informação/Processamento de encomendas/Atendimento da encomenda}} |
|||
=Sistemas de informação/Processamento de encomendas/Aviamento da encomenda= |
|||
{{:Logística/Sistemas de informação/Processamento de encomendas/Aviamento da encomenda}} |
|||
=Sistemas de informação/Processamento de encomendas/Relatório da situação da encomenda= |
|||
{{:Logística/Sistemas de informação/Processamento de encomendas/Relatório da situação da encomenda}} |
|||
=Sistemas de informação/Processamento de encomendas/Exemplo de processamento de uma encomenda= |
|||
{{:Logística/Sistemas de informação/Processamento de encomendas/Exemplo de processamento de uma encomenda}} |
|||
=Sistemas de informação/Rastreabilidade= |
|||
{{:Logística/Sistemas de informação/Rastreabilidade}} |
|||
=Sistemas de informação/Rastreabilidade/Introdução= |
|||
{{:Logística/Sistemas de informação/Rastreabilidade/Introdução}} |
|||
=Sistemas de informação/Rastreabilidade/Rastreabilidade e tecnologias da informação= |
|||
{{:Logística/Sistemas de informação/Rastreabilidade/Rastreabilidade e tecnologias da informação}} |
|||
=Sistemas de informação/Rastreabilidade/Unidades de expedição= |
|||
{{:Logística/Sistemas de informação/Rastreabilidade/Unidades de expedição}} |
|||
=Sistemas de informação/Rastreabilidade/Processo de rastreabilidade GS1= |
|||
{{:Logística/Sistemas de informação/Rastreabilidade/Processo de rastreabilidade GS1}} |
|||
=Sistemas de informação/Rastreabilidade/Sistema de rastreabilidade no sector alimentar= |
|||
{{:Logística/Sistemas de informação/Rastreabilidade/Sistema de rastreabilidade no sector alimentar}} |
|||
=Sistemas de informação/Rastreabilidade/Sistema de rastreabilidade no sector alimentar/Características fundamentais= |
|||
{{:Logística/Sistemas de informação/Rastreabilidade/Sistema de rastreabilidade no sector alimentar/Características fundamentais}} |
|||
=Sistemas de informação/Rastreabilidade/Sistema de rastreabilidade no sector alimentar/Rastreabilidade e qualidade alimentar= |
|||
{{:Logística/Sistemas de informação/Rastreabilidade/Sistema de rastreabilidade no sector alimentar/Rastreabilidade e qualidade alimentar}} |
|||
=Sistemas de informação/Rastreabilidade/Sistema de rastreabilidade no sector alimentar/Autenticidade= |
|||
{{:Logística/Sistemas de informação/Rastreabilidade/Sistema de rastreabilidade no sector alimentar/Autenticidade}} |
|||
=Sistemas de informação/Indicadores de desempenho= |
|||
{{:Logística/Sistemas de informação/Indicadores de desempenho}} |
|||
=Sistemas de informação/Indicadores de desempenho/Valor Económico Acrescentado (EVA)= |
|||
{{:Logística/Sistemas de informação/Indicadores de desempenho/Valor Económico Acrescentado (EVA)}} |
|||
=Sistemas de informação/Indicadores de desempenho/Indicadores AECOC= |
|||
{{:Logística/Sistemas de informação/Indicadores de desempenho/Indicadores AECOC}} |
|||
=Sistemas de informação/Indicadores de desempenho/Taxa de rotação dos stocks= |
|||
{{:Logística/Sistemas de informação/Indicadores de desempenho/Taxa de rotação dos stocks}} |
|||
=Sistemas de informação/Indicadores de desempenho/Indicadores de utilização de recursos: pessoas= |
|||
{{:Logística/Sistemas de informação/Indicadores de desempenho/Indicadores de utilização de recursos: pessoas}} |
|||
=Sistemas de informação/Indicadores de desempenho/Indicadores de utilização de recursos: pessoas/Mão de obra na movimentação de materiais= |
|||
{{:Logística/Sistemas de informação/Indicadores de desempenho/Indicadores de utilização de recursos: pessoas/Mão de obra na movimentação de materiais}} |
|||
=Sistemas de informação/Indicadores de desempenho/Indicadores de utilização de recursos: pessoas/Mão de obra directa na movimentação de materiais= |
|||
{{:Logística/Sistemas de informação/Indicadores de desempenho/Indicadores de utilização de recursos: pessoas/Mão de obra directa na movimentação de materiais}} |
|||
=Sistemas de informação/Indicadores de desempenho/Indicadores de utilização de recursos: pessoas/Perda de mão de obra directa em movimentações= |
|||
{{:Logística/Sistemas de informação/Indicadores de desempenho/Indicadores de utilização de recursos: pessoas/Perda de mão de obra directa em movimentações}} |
|||
=Sistemas de informação/Indicadores de desempenho/Indicadores de utilização de recursos: equipamentos= |
|||
{{:Logística/Sistemas de informação/Indicadores de desempenho/Indicadores de utilização de recursos: equipamentos}} |
|||
=Sistemas de informação/Indicadores de desempenho/Indicadores de utilização de recursos: equipamentos/Utilização de equipamento= |
|||
{{:Logística/Sistemas de informação/Indicadores de desempenho/Indicadores de utilização de recursos: equipamentos/Utilização de equipamento}} |
|||
=Sistemas de informação/Indicadores de desempenho/Indicadores de utilização de recursos: equipamentos/Percentagem de ocupação= |
|||
{{:Logística/Sistemas de informação/Indicadores de desempenho/Indicadores de utilização de recursos: equipamentos/Percentagem de ocupação}} |
|||
=Sistemas de informação/Indicadores de desempenho/Indicadores de utilização de recursos: equipamentos/Disponibilidade= |
|||
{{:Logística/Sistemas de informação/Indicadores de desempenho/Indicadores de utilização de recursos: equipamentos/Disponibilidade}} |
|||
=Sistemas de informação/Indicadores de desempenho/Indicadores de utilização de recursos: equipamentos/Flexibilidade da linha de produção= |
|||
{{:Logística/Sistemas de informação/Indicadores de desempenho/Indicadores de utilização de recursos: equipamentos/Flexibilidade da linha de produção}} |
|||
=Sistemas de informação/Indicadores de desempenho/Indicadores de utilização de recursos: equipamentos/Flexibilidade do posto de trabalho= |
|||
{{:Logística/Sistemas de informação/Indicadores de desempenho/Indicadores de utilização de recursos: equipamentos/Flexibilidade do posto de trabalho}} |
|||
=Sistemas de informação/Indicadores de desempenho/Indicadores de controlo de gestão: movimento= |
|||
{{:Logística/Sistemas de informação/Indicadores de desempenho/Indicadores de controlo de gestão: movimento}} |
|||
=Sistemas de informação/Indicadores de desempenho/Indicadores de controlo de gestão: movimento/Movimento por operação= |
|||
{{:Logística/Sistemas de informação/Indicadores de desempenho/Indicadores de controlo de gestão: movimento/Movimento por operação}} |
|||
=Sistemas de informação/Distância média por movimento= |
|||
{{:Logística/Sistemas de informação/Distância média por movimento}} |
|||
=Gestão do aprovisionamento= |
|||
{{:Logística/Gestão do aprovisionamento}} |
|||
=Gestão do aprovisionamento/Funções do aprovisionamento= |
|||
{{:Logística/Gestão do aprovisionamento/Funções do aprovisionamento}} |
|||
=Gestão do aprovisionamento/Gestão de fornecedores= |
|||
{{:Logística/Gestão do aprovisionamento/Gestão de fornecedores}} |
|||
=Gestão do aprovisionamento/Gestão de fornecedores/Introdução= |
|||
{{:Logística/Gestão do aprovisionamento/Gestão de fornecedores/Introdução}} |
|||
=Gestão do aprovisionamento/Gestão de fornecedores/Âmbito= |
|||
{{:Logística/Gestão do aprovisionamento/Gestão de fornecedores/Âmbito}} |
|||
=Gestão do aprovisionamento/Gestão de fornecedores/Processo de fornecimento= |
|||
{{:Logística/Gestão do aprovisionamento/Gestão de fornecedores/Processo de fornecimento}} |
|||
=Gestão do aprovisionamento/Gestão de fornecedores/Abordagens actuais= |
|||
{{:Logística/Gestão do aprovisionamento/Gestão de fornecedores/Abordagens actuais}} |
|||
=Gestão do aprovisionamento/Gestão de fornecedores/Organização do aprovisionamento= |
|||
{{:Logística/Gestão do aprovisionamento/Gestão de fornecedores/Organização do aprovisionamento}} |
|||
=Gestão do aprovisionamento/Gestão de fornecedores/Abordagem estratégica= |
|||
{{:Logística/Gestão do aprovisionamento/Gestão de fornecedores/Abordagem estratégica}} |
|||
=Gestão do aprovisionamento/Integração das decisões de aprovisionamento e transporte= |
|||
{{:Logística/Gestão do aprovisionamento/Integração das decisões de aprovisionamento e transporte}} |
|||
=Gestão do aprovisionamento/Integração das decisões de aprovisionamento e transporte/Introdução= |
|||
{{:Logística/Gestão do aprovisionamento/Integração das decisões de aprovisionamento e transporte/Introdução}} |
|||
=Gestão do aprovisionamento/Integração das decisões de aprovisionamento e transporte/Condições do frete FOB= |
|||
{{:Logística/Gestão do aprovisionamento/Integração das decisões de aprovisionamento e transporte/Condições do frete FOB}} |
|||
=Gestão do aprovisionamento/Integração das decisões de aprovisionamento e transporte/Intervenção do aprovisionamento nas actividades de transporte= |
|||
{{:Logística/Gestão do aprovisionamento/Integração das decisões de aprovisionamento e transporte/Intervenção do aprovisionamento nas actividades de transporte}} |
|||
=Gestão do aprovisionamento/Integração das decisões de aprovisionamento e transporte/Factores de decisão na selecção do modo de transporte e transportador= |
|||
{{:Logística/Gestão do aprovisionamento/Integração das decisões de aprovisionamento e transporte/Factores de decisão na selecção do modo de transporte e transportador}} |
|||
=Gestão do aprovisionamento/Integração das decisões de aprovisionamento e transporte/Organização para tomada de decisões sobre o transporte= |
|||
{{:Logística/Gestão do aprovisionamento/Integração das decisões de aprovisionamento e transporte/Organização para tomada de decisões sobre o transporte}} |
|||
=Gestão do aprovisionamento/Integração das decisões de aprovisionamento e transporte/Integração contínua= |
|||
{{:Logística/Gestão do aprovisionamento/Integração das decisões de aprovisionamento e transporte/Integração contínua}} |
|||
=Gestão do aprovisionamento/Questões ambientais do aprovisionamento= |
|||
{{:Logística/Gestão do aprovisionamento/Questões ambientais do aprovisionamento}} |
|||
=Gestão de existências= |
|||
{{:Logística/Gestão de existências}} |
|||
=Gestão de existências/Introdução= |
|||
{{:Logística/Gestão de existências/Introdução}} |
|||
=Gestão de existências/Introdução/Existências= |
|||
{{:Logística/Gestão de existências/Introdução/Existências}} |
|||
=Gestão de existências/Introdução/Tipos de existências= |
|||
{{:Logística/Gestão de existências/Introdução/Tipos de existências}} |
|||
=Gestão de existências/Introdução/Tipos de organizações e problemas de gestão de existências= |
|||
{{:Logística/Gestão de existências/Introdução/Tipos de organizações e problemas de gestão de existências}} |
|||
=Gestão de existências/Introdução/Funções das existências= |
|||
{{:Logística/Gestão de existências/Introdução/Funções das existências}} |
|||
=Gestão de existências/Introdução/Classificação dos problemas de gestão de existências= |
|||
{{:Logística/Gestão de existências/Introdução/Classificação dos problemas de gestão de existências}} |
|||
=Gestão de existências/Introdução/Componentes dos sistemas de existências= |
|||
{{:Logística/Gestão de existências/Introdução/Componentes dos sistemas de existências}} |
|||
=Gestão de existências/Introdução/Custos das existências= |
|||
{{:Logística/Gestão de existências/Introdução/Custos das existências}} |
|||
=Gestão de existências/Introdução/Conflito de objectivos= |
|||
{{:Logística/Gestão de existências/Introdução/Conflito de objectivos}} |
|||
=Gestão de existências/Introdução/Ciclo do fluxo das existências= |
|||
{{:Logística/Gestão de existências/Introdução/Ciclo do fluxo das existências}} |
|||
=Gestão de existências/Introdução/Considerações financeiras= |
|||
{{:Logística/Gestão de existências/Introdução/Considerações financeiras}} |
|||
=Gestão de existências/Introdução/Influência nos ciclos económicos= |
|||
{{:Logística/Gestão de existências/Introdução/Influência nos ciclos económicos}} |
|||
=Gestão de existências/Introdução/Just in time= |
|||
{{:Logística/Gestão de existências/Introdução/Just in time}} |
|||
=Técnicas de previsão= |
|||
{{:Logística/Técnicas de previsão}} |
|||
=Sistemas de procura independente: modelos determinísticos= |
|||
{{:Logística/Sistemas de procura independente: modelos determinísticos}} |
|||
=Gestão de existências/Sistemas de procura independente: modelos determinísticos/Modelo de Quantidade Fixa de Encomenda= |
|||
{{:Logística/Gestão de existências/Sistemas de procura independente: modelos determinísticos/Modelo de Quantidade Fixa de Encomenda}} |
|||
=Gestão de existências/Sistemas de procura independente: modelos determinísticos/Modelo de Quantidade Económica de Encomenda (QEE)= |
|||
{{:Logística/Gestão de existências/Sistemas de procura independente: modelos determinísticos/Modelo de Quantidade Económica de Encomenda (QEE)}} |
|||
=Gestão de existências/Sistemas de procura discreta: modelos determinísticos= |
|||
{{:Logística/Gestão de existências/Sistemas de procura discreta: modelos determinísticos}} |
|||
=Gestão de existências/Sistemas de procura independente: modelos estocásticos= |
|||
{{:Logística/Gestão de existências/Sistemas de procura independente: modelos estocásticos}} |
|||
=Gestão de existências/Alteração e limitações dos sistemas de existências= |
|||
{{:Logística/Gestão de existências/Alteração e limitações dos sistemas de existências}} |
|||
=Gestão de existências/Encomendas únicas= |
|||
{{:Logística/Gestão de existências/Encomendas únicas}} |
|||
=Gestão de existências/Encomendas únicas/Procura e tempo de aprovisionamento conhecidos= |
|||
{{:Logística/Gestão de existências/Encomendas únicas/Procura e tempo de aprovisionamento conhecidos}} |
|||
=Gestão de existências/Encomendas únicas/Procura conhecida, tempo de aprovisionamento variável= |
|||
{{:Logística/Gestão de existências/Encomendas únicas/Procura conhecida, tempo de aprovisionamento variável}} |
|||
=Gestão de existências/Encomendas únicas/Procura variável, tempo de aprovisionamento conhecido= |
|||
{{:Logística/Gestão de existências/Encomendas únicas/Procura variável, tempo de aprovisionamento conhecido}} |
|||
=Gestão de existências/Encomendas únicas/Procura e tempo de aprovisionamento variáveis= |
|||
{{:Logística/Gestão de existências/Encomendas únicas/Procura e tempo de aprovisionamento variáveis}} |
|||
=Gestão de existências/Avaliação e medição de existências= |
|||
{{:Logística/Gestão de existências/Avaliação e medição de existências}} |
|||
=Gestão de existências/Controlo de existências= |
|||
{{:Logística/Gestão de existências/Controlo de existências}} |
|||
=Reparações e sobressalentes= |
|||
{{:Logística/Reparações e sobressalentes}} |
|||
=Reparações e sobressalentes/Gestão de sobressalentes= |
|||
{{:Logística/Reparações e sobressalentes/Gestão de sobressalentes}} |
|||
=Movimentação de materiais= |
|||
{{:Logística/Movimentação de materiais}} |
|||
=Movimentação de materiais/Introdução= |
|||
{{:Logística/Movimentação de materiais/Introdução}} |
|||
=Movimentação de materiais/Princípios de movimentação de materiais= |
|||
{{:Logística/Movimentação de materiais/Princípios de movimentação de materiais}} |
|||
=Movimentação de materiais/Listas de verificação= |
|||
{{:Logística/Movimentação de materiais/Listas de verificação}} |
|||
=Movimentação de materiais/Unidade de carga= |
|||
{{:Logística/Movimentação de materiais/Unidade de carga}} |
|||
=Movimentação de materiais/Equipamento= |
|||
{{:Logística/Movimentação de materiais/Equipamento}} |
|||
=Movimentação de materiais/Equipamento/Equipamento de contentorização e unitivo= |
|||
{{:Logística/Movimentação de materiais/Equipamento/Equipamento de contentorização e unitivo}} |
|||
=Movimentação de materiais/Equipamento/Equipamento de contentorização e unitivo/Contentores= |
|||
{{:Logística/Movimentação de materiais/Equipamento/Equipamento de contentorização e unitivo/Contentores}} |
|||
=Movimentação de materiais/Equipamento/Equipamento de contentorização e unitivo/Unificadores= |
|||
{{:Logística/Movimentação de materiais/Equipamento/Equipamento de contentorização e unitivo/Unificadores}} |
|||
=Movimentação de materiais/Equipamento/Equipamento de movimentação de materiais= |
|||
{{:Logística/Movimentação de materiais/Equipamento/Equipamento de movimentação de materiais}} |
|||
=Movimentação de materiais/Equipamento/Equipamento de movimentação de materiais/Conveyors= |
|||
{{:Logística/Movimentação de materiais/Equipamento/Equipamento de movimentação de materiais/Conveyors}} |
|||
=Movimentação de materiais/Equipamento/Equipamento de movimentação de materiais/Conveyors/Chute conveyors= |
|||
{{:Logística/Movimentação de materiais/Equipamento/Equipamento de movimentação de materiais/Conveyors/Chute conveyors}} |
|||
=Movimentação de materiais/Equipamento/Equipamento de movimentação de materiais/Conveyors/Belt conveyor= |
|||
{{:Logística/Movimentação de materiais/Equipamento/Equipamento de movimentação de materiais/Conveyors/Belt conveyor}} |
|||
=Movimentação de materiais/Equipamento/Equipamento de movimentação de materiais/Conveyors/Roller conveyor= |
|||
{{:Logística/Movimentação de materiais/Equipamento/Equipamento de movimentação de materiais/Conveyors/Roller conveyor}} |
|||
=Movimentação de materiais/Equipamento/Equipamento de movimentação de materiais/Conveyors/Wheel conveyor= |
|||
{{:Logística/Movimentação de materiais/Equipamento/Equipamento de movimentação de materiais/Conveyors/Wheel conveyor}} |
|||
=Movimentação de materiais/Equipamento/Equipamento de movimentação de materiais/Conveyors/Slat Conveyor= |
|||
{{:Logística/Movimentação de materiais/Equipamento/Equipamento de movimentação de materiais/Conveyors/Slat Conveyor}} |
|||
=Movimentação de materiais/Equipamento/Equipamento de movimentação de materiais/Conveyors/Chain Conveyor= |
|||
{{:Logística/Movimentação de materiais/Equipamento/Equipamento de movimentação de materiais/Conveyors/Chain Conveyor}} |
|||
=Movimentação de materiais/Equipamento/Equipamento de movimentação de materiais/Conveyors/Tow Line Conveyor= |
|||
{{:Logística/Movimentação de materiais/Equipamento/Equipamento de movimentação de materiais/Conveyors/Tow Line Conveyor}} |
|||
=Movimentação de materiais/Equipamento/Equipamento de movimentação de materiais/Conveyors/Trolley Conveyor= |
|||
{{:Logística/Movimentação de materiais/Equipamento/Equipamento de movimentação de materiais/Conveyors/Trolley Conveyor}} |
|||
=Movimentação de materiais/Equipamento/Equipamento de movimentação de materiais/Conveyors/Power e Free Conveyor= |
|||
{{:Logística/Movimentação de materiais/Equipamento/Equipamento de movimentação de materiais/Conveyors/Power e Free Conveyor}} |
|||
=Movimentação de materiais/Equipamento/Equipamento de movimentação de materiais/Conveyors/Cart-on-Track Conveyor= |
|||
{{:Logística/Movimentação de materiais/Equipamento/Equipamento de movimentação de materiais/Conveyors/Cart-on-Track Conveyor}} |
|||
=Movimentação de materiais/Equipamento/Equipamento de movimentação de materiais/Conveyors/Sorting Conveyor= |
|||
{{:Logística/Movimentação de materiais/Equipamento/Equipamento de movimentação de materiais/Conveyors/Sorting Conveyor}} |
|||
=Movimentação de materiais/Equipamento/Equipamento de movimentação de materiais/Veículos Industriais= |
|||
{{:Logística/Movimentação de materiais/Equipamento/Equipamento de movimentação de materiais/Veículos Industriais}} |
|||
=Movimentação de materiais/Equipamento/Equipamento de movimentação de materiais/Veículos Industriais/Walking= |
|||
{{:Logística/Movimentação de materiais/Equipamento/Equipamento de movimentação de materiais/Veículos Industriais/Walking}} |
|||
=Movimentação de materiais/Equipamento/Equipamento de movimentação de materiais/Veículos Industriais/Riding= |
|||
{{:Logística/Movimentação de materiais/Equipamento/Equipamento de movimentação de materiais/Veículos Industriais/Riding}} |
|||
=Movimentação de materiais/Equipamento/Equipamento de movimentação de materiais/Veículos Industriais/Automated= |
|||
{{:Logística/Movimentação de materiais/Equipamento/Equipamento de movimentação de materiais/Veículos Industriais/Automated}} |
|||
=Movimentação de materiais/Equipamento/Equipamento de movimentação de materiais/Monocarris,Hoists e Gruas= |
|||
{{:Logística/Movimentação de materiais/Equipamento/Equipamento de movimentação de materiais/Monocarris,Hoists e Gruas}} |
|||
=Movimentação de materiais/Equipamento/Equipamento de movimentação de materiais/Monocarris,Hoists e Gruas/Monocarril= |
|||
{{:Logística/Movimentação de materiais/Equipamento/Equipamento de movimentação de materiais/Monocarris,Hoists e Gruas/Monocarril}} |
|||
=Movimentação de materiais/Equipamento/Equipamento de movimentação de materiais/Monocarris,Hoists e Gruas/Hoists= |
|||
{{:Logística/Movimentação de materiais/Equipamento/Equipamento de movimentação de materiais/Monocarris,Hoists e Gruas/Hoists}} |
|||
=Movimentação de materiais/Equipamento/Equipamento de movimentação de materiais/Monocarris,Hoists e Gruas/Gruas= |
|||
{{:Logística/Movimentação de materiais/Equipamento/Equipamento de movimentação de materiais/Monocarris,Hoists e Gruas/Gruas}} |
|||
=Movimentação de materiais/Equipamento/Equipamento de armazenagem= |
|||
{{:Logística/Movimentação de materiais/Equipamento/Equipamento de armazenagem}} |
|||
=Movimentação de materiais/Equipamento/Equipamento de armazenagem/Armazenagem de unidades de carga= |
|||
{{:Logística/Movimentação de materiais/Equipamento/Equipamento de armazenagem/Armazenagem de unidades de carga}} |
|||
=Movimentação de materiais/Equipamento/Equipamento de armazenagem/Armazenagem de unidades de carga/Estantes para armazenagem de unidades de carga= |
|||
{{:Logística/Movimentação de materiais/Equipamento/Equipamento de armazenagem/Armazenagem de unidades de carga/Estantes para armazenagem de unidades de carga}} |
|||
=Movimentação de materiais/Equipamento/Equipamento de armazenagem/Armazenagem de unidades de carga/Estantes para armazenagem de unidades de carga/Armazenagem por empilhamento= |
|||
{{:Logística/Movimentação de materiais/Equipamento/Equipamento de armazenagem/Armazenagem de unidades de carga/Estantes para armazenagem de unidades de carga/Armazenagem por empilhamento}} |
|||
=Movimentação de materiais/Equipamento/Equipamento de armazenagem/Armazenagem de unidades de carga/Estantes para armazenagem de unidades de carga/Armação para empilhamento= |
|||
{{:Logística/Movimentação de materiais/Equipamento/Equipamento de armazenagem/Armazenagem de unidades de carga/Estantes para armazenagem de unidades de carga/Armação para empilhamento}} |
|||
=Movimentação de materiais/Equipamento/Equipamento de armazenagem/Armazenagem de unidades de carga/Estantes para armazenagem de unidades de carga/Estante de profundidade simples= |
|||
{{:Logística/Movimentação de materiais/Equipamento/Equipamento de armazenagem/Armazenagem de unidades de carga/Estantes para armazenagem de unidades de carga/Estante de profundidade simples}} |
|||
=Movimentação de materiais/Equipamento/Equipamento de armazenagem/Armazenagem de unidades de carga/Estantes para armazenagem de unidades de carga/Estante de profundidade dupla= |
|||
{{:Logística/Movimentação de materiais/Equipamento/Equipamento de armazenagem/Armazenagem de unidades de carga/Estantes para armazenagem de unidades de carga/Estante de profundidade dupla}} |
|||
=Movimentação de materiais/Equipamento/Equipamento de armazenagem/Armazenagem de unidades de carga/Estantes para armazenagem de unidades de carga/Estante drive-in= |
|||
{{:Logística/Movimentação de materiais/Equipamento/Equipamento de armazenagem/Armazenagem de unidades de carga/Estantes para armazenagem de unidades de carga/Estante drive-in}} |
|||
=Movimentação de materiais/Equipamento/Equipamento de armazenagem/Armazenagem de unidades de carga/Estantes para armazenagem de unidades de carga/Estante drive-thru= |
|||
{{:Logística/Movimentação de materiais/Equipamento/Equipamento de armazenagem/Armazenagem de unidades de carga/Estantes para armazenagem de unidades de carga/Estante drive-thru}} |
|||
=Movimentação de materiais/Equipamento/Equipamento de armazenagem/Armazenagem de unidades de carga/Estantes para armazenagem de unidades de carga/Estante dinâmica= |
|||
{{:Logística/Movimentação de materiais/Equipamento/Equipamento de armazenagem/Armazenagem de unidades de carga/Estantes para armazenagem de unidades de carga/Estante dinâmica}} |
|||
=Movimentação de materiais/Equipamento/Equipamento de armazenagem/Armazenagem de unidades de carga/Estantes para armazenagem de unidades de carga/Estante push-back= |
|||
{{:Logística/Movimentação de materiais/Equipamento/Equipamento de armazenagem/Armazenagem de unidades de carga/Estantes para armazenagem de unidades de carga/Estante push-back}} |
|||
=Movimentação de materiais/Equipamento/Equipamento de armazenagem/Armazenagem de unidades de carga/Estantes para armazenagem de unidades de carga/Estante móvel= |
|||
{{:Logística/Movimentação de materiais/Equipamento/Equipamento de armazenagem/Armazenagem de unidades de carga/Estantes para armazenagem de unidades de carga/Estante móvel}} |
|||
=Movimentação de materiais/Equipamento/Equipamento de armazenagem/Armazenagem de unidades de carga/Estantes para armazenagem de unidades de carga/Estante cantilever= |
|||
{{:Logística/Movimentação de materiais/Equipamento/Equipamento de armazenagem/Armazenagem de unidades de carga/Estantes para armazenagem de unidades de carga/Estante cantilever}} |
|||
=Movimentação de materiais/Equipamento/Equipamento de armazenagem/Armazenagem de unidades de carga/Equipamento para armazenagem de unidades de carga= |
|||
{{:Logística/Movimentação de materiais/Equipamento/Equipamento de armazenagem/Armazenagem de unidades de carga/Equipamento para armazenagem de unidades de carga}} |
|||
=Movimentação de materiais/Equipamento/Equipamento de armazenagem/Armazenagem de unidades de carga/Equipamento para armazenagem de unidades de carga/Operador a pé= |
|||
{{:Logística/Movimentação de materiais/Equipamento/Equipamento de armazenagem/Armazenagem de unidades de carga/Equipamento para armazenagem de unidades de carga/Operador a pé}} |
|||
=Movimentação de materiais/Equipamento/Equipamento de armazenagem/Armazenagem de unidades de carga/Equipamento para armazenagem de unidades de carga/Operador a pé/Porta paletes= |
|||
{{:Logística/Movimentação de materiais/Equipamento/Equipamento de armazenagem/Armazenagem de unidades de carga/Equipamento para armazenagem de unidades de carga/Operador a pé/Porta paletes}} |
|||
=Movimentação de materiais/Equipamento/Equipamento de armazenagem/Armazenagem de unidades de carga/Equipamento para armazenagem de unidades de carga/Operador a pé/Empilhadora= |
|||
{{:Logística/Movimentação de materiais/Equipamento/Equipamento de armazenagem/Armazenagem de unidades de carga/Equipamento para armazenagem de unidades de carga/Operador a pé/Empilhadora}} |
|||
=Movimentação de materiais/Equipamento/Equipamento de armazenagem/Armazenagem de unidades de carga/Equipamento para armazenagem de unidades de carga/Condutor a bordo= |
|||
{{:Logística/Movimentação de materiais/Equipamento/Equipamento de armazenagem/Armazenagem de unidades de carga/Equipamento para armazenagem de unidades de carga/Condutor a bordo}} |
|||
=Movimentação de materiais/Equipamento/Equipamento de armazenagem/Armazenagem de unidades de carga/Equipamento para armazenagem de unidades de carga/Condutor a bordo/Corredores largos= |
|||
{{:Logística/Movimentação de materiais/Equipamento/Equipamento de armazenagem/Armazenagem de unidades de carga/Equipamento para armazenagem de unidades de carga/Condutor a bordo/Corredores largos}} |
|||
=Movimentação de materiais/Equipamento/Equipamento de armazenagem/Armazenagem de unidades de carga/Equipamento para armazenagem de unidades de carga/Condutor a bordo/Corredores largos/Porta paletes motorizado= |
|||
{{:Logística/Movimentação de materiais/Equipamento/Equipamento de armazenagem/Armazenagem de unidades de carga/Equipamento para armazenagem de unidades de carga/Condutor a bordo/Corredores largos/Porta paletes motorizado}} |
|||
=Movimentação de materiais/Equipamento/Equipamento de armazenagem/Armazenagem de unidades de carga/Equipamento para armazenagem de unidades de carga/Condutor a bordo/Corredores largos/Empilhadora de contrapeso= |
|||
{{:Logística/Movimentação de materiais/Equipamento/Equipamento de armazenagem/Armazenagem de unidades de carga/Equipamento para armazenagem de unidades de carga/Condutor a bordo/Corredores largos/Empilhadora de contrapeso}} |
|||
=Movimentação de materiais/Equipamento/Equipamento de armazenagem/Armazenagem de unidades de carga/Equipamento para armazenagem de unidades de carga/Condutor a bordo/Corredores estreitos= |
|||
{{:Logística/Movimentação de materiais/Equipamento/Equipamento de armazenagem/Armazenagem de unidades de carga/Equipamento para armazenagem de unidades de carga/Condutor a bordo/Corredores estreitos}} |
|||
=Movimentação de materiais/Equipamento/Equipamento de armazenagem/Armazenagem de unidades de carga/Equipamento para armazenagem de unidades de carga/Condutor a bordo/Corredores estreitos/Empilhadora straddle= |
|||
{{:Logística/Movimentação de materiais/Equipamento/Equipamento de armazenagem/Armazenagem de unidades de carga/Equipamento para armazenagem de unidades de carga/Condutor a bordo/Corredores estreitos/Empilhadora straddle}} |
|||
=Movimentação de materiais/Equipamento/Equipamento de armazenagem/Armazenagem de unidades de carga/Equipamento para armazenagem de unidades de carga/Condutor a bordo/Corredores estreitos/Empilhadora straddle reach= |
|||
{{:Logística/Movimentação de materiais/Equipamento/Equipamento de armazenagem/Armazenagem de unidades de carga/Equipamento para armazenagem de unidades de carga/Condutor a bordo/Corredores estreitos/Empilhadora straddle reach}} |
|||
=Movimentação de materiais/Equipamento/Equipamento de armazenagem/Armazenagem de unidades de carga/Equipamento para armazenagem de unidades de carga/Condutor a bordo/Corredores estreitos/Empilhadora lateral= |
|||
{{:Logística/Movimentação de materiais/Equipamento/Equipamento de armazenagem/Armazenagem de unidades de carga/Equipamento para armazenagem de unidades de carga/Condutor a bordo/Corredores estreitos/Empilhadora lateral}} |
|||
=Movimentação de materiais/Equipamento/Equipamento de armazenagem/Armazenagem de unidades de carga/Equipamento para armazenagem de unidades de carga/Condutor a bordo/Corredores estreitos/Empilhadora de torre= |
|||
{{:Logística/Movimentação de materiais/Equipamento/Equipamento de armazenagem/Armazenagem de unidades de carga/Equipamento para armazenagem de unidades de carga/Condutor a bordo/Corredores estreitos/Empilhadora de torre}} |
|||
=Movimentação de materiais/Equipamento/Equipamento de armazenagem/Armazenagem de unidades de carga/Equipamento para armazenagem de unidades de carga/Condutor a bordo/Corredores estreitos/Empilhadora híbrida= |
|||
{{:Logística/Movimentação de materiais/Equipamento/Equipamento de armazenagem/Armazenagem de unidades de carga/Equipamento para armazenagem de unidades de carga/Condutor a bordo/Corredores estreitos/Empilhadora híbrida}} |
|||
=Movimentação de materiais/Equipamento/Equipamento de armazenagem/Armazenagem de unidades de carga/Equipamento para armazenagem de unidades de carga/Máquina de armazenamento automática= |
|||
{{:Logística/Movimentação de materiais/Equipamento/Equipamento de armazenagem/Armazenagem de unidades de carga/Equipamento para armazenagem de unidades de carga/Máquina de armazenamento automática}} |
|||
=Movimentação de materiais/Equipamento/Equipamento de armazenagem/Equipamento de armazenagem de pequenas cargas= |
|||
{{:Logística/Movimentação de materiais/Equipamento/Equipamento de armazenagem/Equipamento de armazenagem de pequenas cargas}} |
|||
=Movimentação de materiais/Equipamento/Equipamento de armazenagem/Equipamento de armazenagem de pequenas cargas/Equipamento de armazenagem operator-to-stock= |
|||
{{:Logística/Movimentação de materiais/Equipamento/Equipamento de armazenagem/Equipamento de armazenagem de pequenas cargas/Equipamento de armazenagem operator-to-stock}} |
|||
=Movimentação de materiais/Equipamento/Equipamento de armazenagem/Equipamento de armazenagem de pequenas cargas/Equipamento de armazenagem operator-to-stock/Estante para caixas= |
|||
{{:Logística/Movimentação de materiais/Equipamento/Equipamento de armazenagem/Equipamento de armazenagem de pequenas cargas/Equipamento de armazenagem operator-to-stock/Estante para caixas}} |
|||
=Movimentação de materiais/Equipamento/Equipamento de armazenagem/Equipamento de armazenagem de pequenas cargas/Equipamento de armazenagem operator-to-stock/Armários com módulos de gavetas= |
|||
{{:Logística/Movimentação de materiais/Equipamento/Equipamento de armazenagem/Equipamento de armazenagem de pequenas cargas/Equipamento de armazenagem operator-to-stock/Armários com módulos de gavetas}} |
|||
=Movimentação de materiais/Equipamento/Equipamento de armazenagem/Equipamento de armazenagem de pequenas cargas/Equipamento de armazenagem operator-to-stock/Estante dinâmica para caixas= |
|||
{{:Logística/Movimentação de materiais/Equipamento/Equipamento de armazenagem/Equipamento de armazenagem de pequenas cargas/Equipamento de armazenagem operator-to-stock/Estante dinâmica para caixas}} |
|||
=Movimentação de materiais/Equipamento/Equipamento de armazenagem/Equipamento de armazenagem de pequenas cargas/Equipamento de armazenagem operator-to-stock/Mezanino= |
|||
{{:Logística/Movimentação de materiais/Equipamento/Equipamento de armazenagem/Equipamento de armazenagem de pequenas cargas/Equipamento de armazenagem operator-to-stock/Mezanino}} |
|||
{{AutoCat}} |
{{AutoCat}} |
Revisão das 17h51min de 13 de março de 2011
Capa
Prefácio
Introdução
Texto da introdução
Técnicas de previsão
Etapas de desenvolvimento - 9 fases | ||||||||
---|---|---|---|---|---|---|---|---|
Início: ![]() |
Básico: ![]() |
Criação: ![]() |
Desenvolvimento: ![]() |
Maturação: ![]() |
Revisão: ![]() |
Desenvolvido: ![]() |
Finalização: ![]() |
Abrangente: ![]() |
Série temporal e dados transversais
Representação gráfica
Estatísticas univariadas, bivariadas e autocorrelação (Gonçalo Ferreira)
Medidas de precisão da previsão
Intervalo de previsão (Luís Pedro Seixas)
Estimativa dos mínimos quadrados
Transformações e ajustamentos (Gonçalo Ferreira)
Decomposição de séries temporais (José Santos)
Princípios
Médias móveis
Média móvel simples
Média móvel centrada
Média móvel ponderada
Alisamento local de regressão
Decomposição clássica
Métodos do Census Bureau
Decomposição STL
Alisamento exponencial (José Santos)
Regressão simples
Regressão múltipla (António Cruz)
Métodos ARIMA de Box-Jenkins (Luís Pedro Seixas)
Modelos avançados de previsão
Previsão a longo prazo
Dinâmica de grupo
Intenções
Opinião de peritos
Análise conjunta (Pedro Rito)
Metodologia bootstrap
Analogias
Extrapolação
Redes neuronais (Luís Pedro Seixas)
Previsão baseada em regras (Pedro Rito)
Sistemas periciais
Integração, ajustamento e combinação
Técnicas de previsão/Séries temporais e dados transversais
Logística/Técnicas de previsão/Séries temporais e dados transversais
Técnicas de previsão/Representações gráficas
Logística/Técnicas de previsão/Representações gráficas
Técnicas de previsão/Estatísticas univariadas, bivariadas e autocorrelação
Considera-se uma estatística o resumo numérico de um determinado conjunto de dados. (Makridakis, 1998, p. 28-29).
As estatísticas descritivas mais usadas tanto para conjuntos de dados univariados únicos, como séries temporais únicas são a média, o desvio padrão e a variância. No caso de existirem dados bivariados (par de variáveis aleatórias), as estatísticas mais usadas para descrever a relação entre os dois conjuntos de dados são a covariância e a correlação. Finalmente, as estatísticas mais comuns para efectuar a comparação entre as observações de uma única série temporal em dois períodos de tempo distintos são a autocovariância e a autocorrelação.
Estatísticas univariadas
A medição do valor em relação ao qual 50 por cento dos desvios estão acima e 50 por cento dos desvios estão abaixo é dada pela média (ou média aritmética), ou seja, a soma dos desvios em torno desta é zero. Por exemplo (DeLurgio, 1998, p. 41):
1 | 2 | 3 | 4 | 5 | 6 | 7 | 8 | 9 | |
8 | 8 | 11 | 7 | 8 | 12 | 10 | 13 | 13 | |
onde , na Tabela 1, é o valor de vendas de um determinado produto nos últimos nove meses. A média das vendas é dada por:
onde é o somatório de = 1 até = 9.
Desvios
Um desvio médio () é definido pela subtracção da média a um valor observado () e é dado por:
1 | 2 | 3 | 4 | 5 | 6 | 7 | 8 | 9 | |
8 | 8 | 11 | 7 | 8 | 12 | 10 | 13 | 13 | |
-2 | -2 | 1 | -3 | -2 | 2 | 0 | 3 | 3 | |
Como a soma dos desvios é sempre igual a zero, é útil desenvolver uma estatística descritiva para estes desvios, que, ou são elevados ao quadrado, ou, ocasionalmente, toma-se o seu valor absoluto.
O desvio médio absoluto é denominado de DMA e é dado por:
Neste caso:
Por seu lado, o desvio médio quadrado, é designado por DMQ e é dado por:
Neste caso:
Intimamente relacionado com o desvio médio quadrado (DMQ), está a variância. Esta é definida da seguinte maneira:
Neste caso:
onde representa os «graus de liberdade», que podem ser definidos como o número de observações a subtrair pelo número de parâmetros estimados (Makridakis, 1998, p. 31-32).
A variância é menos intuitiva que o DMQ mas possui propriedades matemáticas desejáveis, porque, ao contrário do DMQ não é uma estimativa tendenciosa.
Tanto a variância como o desvio médio absoluto fornecem medidas de dispersão. Medem aproximadamente o desvio médio das observações em relação à sua média. Se as observações estiverem muito dispersas, estarão longe da média (acima e abaixo). Neste caso tanto o desvio médio absoluto como a variância terão um valor elevado. Quando as observações estão próximas entre si, o desvio médio absoluto e a variância terão valores pequenos. Ambos têm a mesma unidade que as observações.
O desvio padrão é a raiz quadrada do desvio médio quadrado (DMQ) e é dado por (DeLurgio, 1998, p. 43):
Neste caso:
Muitos conjuntos de dados verificam as seguintes regras empíricas (Makridakis, 1998, p. 32):
- Aproximadamente dois terços das observações distam até 1 desvio padrão da sua média;
- Aproximadamente 95% das observações distam até 2 desvios padrões da sua média.
Quando se ordena o número de observações por ordem crescente, como acontece na Tabela 2, e este for ímpar, a mediana é o valor em relação ao qual 50 por cento dos valores são maiores e 50 por cento são menores, ou seja, a mediana é a observação a meio. Nos casos em que o número de observações for par, a mediana é igual à média entre os valores das duas observações centrais.
7 | 8 | 8 | 8 | 10 | 11 | 12 | 13 | 13 | |
Para as nove observações da Tabela 2, quatro estão acima de 10 e quatro estão abaixo de 10. A mediana é, portanto, 10.
A média e a mediana providenciam uma medida numérica do centro do conjunto de dados, bem como a medição da sua dispersão, de modo a saber se estes estão fortemente agrupados ou espalhados por uma vasta gama de valores (Makridakis, 1998, p. 29-30).
O número, ou conjunto de números, que ocorre mais vezes dá pelo nome de moda. Nos dados da Tabela 2, o número que aparece com maior frequência é 8, logo é a moda(DeLurgio, 1998, p. 41).
Técnicas de previsão/Medidas de precisão da previsão
No estudo das técnicas de previsão as medidas de precisão são uma aplicação de extrema importância. Os valores futuros das variáveis tornam-se bastante difíceis de prever dada a complexidade da grande maioria dessas variáveis na vida real. Assim, é fundamental incluir informação acerca da medida em que a previsão pode desviar-se do valor real da variável. Este conhecimento adicional fornece uma melhor percepção sobre o quão precisa pode ser a previsão (Stevenson, 1996, p. 496).
Por forma a fazer a escolha mais acertada de entre as técnicas disponíveis e devido ao facto de algumas técnicas oferecerem uma maior precisão do que outras, consoante a situação, o responsável pela decisão necessita de uma medida de precisão para usar como base de comparação ao escolher uma dessas técnicas.
Note-se, que enquanto algumas aplicações de previsões envolvem uma série de previsões (por exemplo, as receitas mensais de uma empresa), outras envolvem uma única previsão que conduz a uma única decisão (por exemplo, o tamanho de um centro comercial). É importante monitorizar os erros de previsão para determinar se estão dentro de limites razoáveis, quando são efectuadas previsões periódicas. Devem ser implementadas medidas correctivas no caso de os erros de previsão não se encontrarem dentro destes limites.
A diferença entre o valor real e a previsão do valor dá origem ao erro de previsão:
=
Onde:
= Erro no período
= Valor real no período
= Previsão para o período
Quando a previsão é muito baixa, ou seja, menor que o valor actual, o resultado são erros positivos. Os erros negativos ocorrem quando a previsão tem um valor mais elevado que o valor actual. Por exemplo, se a procura actual de um produto num mês é de 50 unidades e a previsão de procura for de 60 unidades, a previsão é demasiado alta e o erro será negativo (50 - 60 = -10).
As decisões podem ser influenciadas de duas formas distintas pelos erros de previsão. A primeira consiste na escolha entre alternativas de previsão. A outra é na avaliação do sucesso ou fracasso da técnica utilizada.
De seguida são apresentados os vários erros de previsão, as suas definições e fórmulas. No final, é exposto um exemplo de aplicação e respectivos cálculos, para melhor compreensão.
Erro médio
De acordo com Dilworth (1992, p. 93-94), o valor da previsão raramente é igual ao valor real devido às variações aleatórias que caracterizam a variável que, contudo, não deve diferir muito da média dos valores reais ao longo desses mesmos períodos. Assim, a previsão do modelo não deve ser tendenciosa, quer isto dizer que a variável não deve ser sobrestimada ou subestimada. O erro médio deve ser muito próximo de zero caso o modelo de previsão seja isento, sendo calculado pela soma dos erros de previsão de uma série de períodos e dividindo essa soma pelo número de erros usados para calcular a soma. O erro médio pode ser expresso através da seguinte equação:
Onde:
= Número de períodos usados
O numerador da equação é chamado de soma corrente dos erros de previsão. De referir que, caso a soma de erros positivos seja igual à soma de erros negativos, o modelo de previsão é imparcial, isto é, a soma é próxima de zero.
Desvio médio absoluto
O desvio médio absoluto (DMA) é uma das medidas mais comuns de erro de previsão. O DMA não leva em conta se um erro foi sobrestimado ou subestimado, caracterizando-se por ser a média dos erros cometidos pelo modelo de previsão durante uma série de períodos de tempo. Outra designação possível de aplicar ao DMA é de erro médio absoluto (EMA). Para calcular o DMA, subtrai-se o valor da previsão ao valor real em cada período de tempo, tendo em conta que o resultado deverá ser positivo, ou seja, sempre em módulo, soma-se e divide-se pelo número de valores que foram usados para obter a soma.
Onde:
| | Significa: usar o valor absoluto, ignorando a direcção do desvio
Erro quadrático médio
O erro quadrático médio (EQM) também pode ser usado como uma medida do erro de previsão. O EQM é determinado somando os erros de previsão ao quadrado e dividindo pelo número de erros usados no cálculo. O erro quadrático médio pode ser expresso pela seguinte equação:
Erro percentual
Segundo Machado et al. (2009, p. 26), o erro percentual mede a percentagem do erro em relação ao valor real. Calcula-se, subtraindo ao valor real no período t a previsão no respectivo período e divide-se o resultado pelo valor real utilizado anteriormente.
Erro médio percentual
Calcula-se dividindo a erro percentual pelo número de períodos. Se os erros positivos forem compensados pelos erros negativos, o resultado deve ser aproximadamente nulo.
Erro médio percentual absoluto
De acordo com Heizer et al. (2004, p. 114), tanto os valores do desvio médio absoluto como do erro quadrático médio dependem da importância do item que está a ser previsto, o que pode causar problemas ao nível da dimensão dos resultados. Se a previsão do item é medida em milhares, os valores do desvio médio absoluto e do erro quadrático médio podem ser muito grandes. A utilização do erro médio percentual absoluto (EMPA) é uma medida eficaz para resolver esse problema. O EMPA é a média da diferença absoluta entre os valores previstos e actuais, expressa em percentagem dos valores actuais. Assim, se existem previsões e valores reais para períodos, o erro médio percentual absoluto é:
Exemplo de aplicação
Na Tabela 1 os valores da procura real e prevista são conhecidos e é possível calcular os vários erros mencionados acima, aplicando as respectivas fórmulas.
Período | Procura real |
Previsão | Erro | Erro absoluto |
Erro quadrático |
Erro percentual |
Erro percentual absoluto |
1 | 117 | 115 | 2 | 2 | 4 | 1,7 | 1,7 |
2 | 113 | 116 | -3 | 3 | 9 | -2,7 | 2,7 |
3 | 116 | 115 | 1 | 1 | 1 | 0,9 | 0,9 |
4 | 110 | 114 | -4 | 4 | 16 | -3,6 | 3,6 |
5 | 113 | 111 | 2 | 2 | 4 | 1,8 | 1,8 |
6 | 119 | 114 | 5 | 5 | 25 | 4,2 | 4,2 |
7 | 116 | 117 | -1 | 1 | 1 | -0,9 | 0,9 |
8 | 112 | 116 | -4 | 4 | 16 | -3,6 | 3,6 |
Total | -2 | 22 | 76 | -2,2 | 19,3 | ||
Técnicas de previsão/Intervalo de previsão
No âmbito da previsão pretende-se, geralmente, encontrar não só valores mas também parâmetros associados à incerteza sob a forma de intervalos de previsão. Estes são úteis porque possibilitam ao utilizador da previsão encontrar o pior ou melhor cenário e com uma percepção do quão dependente é a previsão e ainda porque protege-o das críticas que apontem para uma incorrecção da previsão. As previsões não podem ser tidas como valores perfeitos, facto enfatizado por estes intervalos. Os intervalos de previsão são normalmente baseados na Estimativa dos Mínimos Quadrados (MSE) porque permite obter um valor estimado para a variância, em previsões de um passo, do erro de previsão. Logo, a raíz quadrada da MSE é uma estimativa do desvio padrão do erro de previsão. A suposição habitual para a construção de intervalos de previsão é que os erros de previsão estão normalmente distribuídos com média igual a zero. Tendo isto em conta, uma aproximação para o intervalo de previsão da próxima observação é (Makridakis et al., 1998, p. 52):
O valor de determina a extensão e a probabilidade do intervalo de previsão.
Para previsões com passos múltiplos é necessário modificar a MSE, uma abordagem é definir a h-step MSE como (Makridakis et al., 1998, p. 54):
onde é o erro associado à previsão h-step da observação no instante t. Assim, se assumirmos que o erro da previsão h-step é normalmente distribuído com média igual a zero, temos o intervalo de previsão
Antes do cálculo do intervalo de previsão desta forma, deve-se verificar os erros para assegurar que os pressupostos da distribuição normal e média igual a zero são cumpridos.
Técnicas de previsão/Estimativa dos mínimos quadrados
Logística/Técnicas de previsão/Estimativa dos mínimos quadrados
Técnicas de previsão/Transformações e ajustamentos
O ajuste de dados históricos leva, por vezes, a modelos de previsão mais simples e facilmente interpretáveis. Existem três tipos de ajuste (Makridakis, 1998, p. 63):
- Transformações matemáticas (tais como logaritmos e raízes quadrados);
- Ajustes para remover a variação dos dados relativa a efeitos do calendário;
- Ajustes relacionados com mudanças e aumento da população.
Transformações matemáticas
À aplicação de uma alteração matemática nos valores de uma variável dá-se o nome de transformação de dados. Existe uma grande variedade de transformações possíveis, como a adição ou multiplicação de constantes, elevação a uma potência, conversão para escalas logarítmicas, tomar o inverso, simétrico ou a raiz quadrada dos valores ou aplicação de transformações trigonométricas tais como o seno. (Osbourne, [2002])
A raiz quadrada e o logaritmo são as transformações mais úteis. A função raiz quadrada ajuda a reduzir a variação do tamanho dos ciclos anuais, facilitando assim, a previsão dos dados, enquanto que os logaritmos são mais fáceis de interpretar (alterações no valor do logaritmo levam a alterações percentuais na escala original). Uma lista das transformações mais úteis é apresentada na tabela seguinte (Makridakis, 1998, p. 63-70):
Raiz quadrada | |||||||||
Raiz cúbica | |||||||||
Logaritmo | |||||||||
Simétrico do inverso | |||||||||
Onde são as observações originais e as observações transformadas.
Cada uma destas transformações pertence à família das transformações de potência:
Para a transformação é simplesmente , para é a raiz quadrada e para é o simétrico do inverso. Para a transformação está definida como o logaritmo porque comporta-se como tal para valores de próximos de . Para , o sinal negativo na transformação de potência é usado para que todas as transformações resultem em funções crescentes (a variável transformada aumenta com o aumento de ). O parâmetro pode ser qualquer número se os dados forem positivos, superior a zero se estes tiverem zeros e se forem negativos não é possível utilizar transformações de potência a não ser que estas sejam ajustadas primeiro através da adição de uma constante a todos os valores.
As previsões são calculadas nos dados transformados em vez de nos originais. No entanto é necessário reverter a transformação porque o interesse está na previsão dos dados originais. As transformações revertidas da potência são geralmente dadas por:
Por exemplo, obtém-se a previsão da escala original elevando ao quadrado as previsões da raiz quadrada dos dados.
É preferível escolher valores mais simples de para fazer as transformações presentes na Tabela 1. Valores próximos de produzirão resultados semelhantes porque os modelos e previsões de séries temporais são relativamente insensíveis ao valor de escolhido. No entanto, valores de tais como , ou torna mais fácil a interpretação dos resultados. Há ainda a possibilidade de não ser necessário efectuar qualquer transformação, como no caso de .
Após a transformação dos dados, é necessário transformar também os intervalos de previsão de volta para a escala original. A maneira mais simples de proceder é aplicar a transformação inversa nos limites do intervalo de previsão. Portanto, caso tenham sido usados logaritmos, e a previsão na escala de logaritmos for e o intervalo de previsão (,), então a previsão na escala original será com o intervalo de previsão (,). Estes intervalos de previsão não necessitam de ser simétricos à volta da previsão.
O impacto das transformações na precisão das previsões nem sempre é importante tal como é demonstrado em certos estudos empíricos. Esta situação deve-se ao facto da maioria das técnicas de previsão valorizarem mais os dados mais recentes. Portanto, é natural que uma pequena variação no início de uma série não afecte consideravelmente as previsões. As transformações matemáticas fazem a grande diferença apenas quando as séries alteram rapidamente a sua variação.
No entanto, o EQM (e outras medidas de precisão) dão igual importância a todos os dados daí que os intervalos de previsão sejam afectados pelas transformações. No cálculo de intervalos de previsão, assume-se que a variação é aproximadamente constante ao longo da série.
Referências
- OSBOURNE, Jason W. - Notes on the use of data transformations [Em linha]. North Carolina State University, 2002. [Consult. 17 Mai. 2011]. Disponível em WWW:<URL:http://pareonline.net/getvn.asp?v=8&n=6>.
Técnicas de previsão/Decomposição de séries temporais
Muitos métodos de previsão, têm como propósito distinguir a tendência de qualquer aleatoriedade que possa estar contida nas observações. Numa série de dados com tendência, o alisamento das observações passadas, permite separar e eliminar a aleatoriedade, facilitando a utilização da tendência para prever os valores futuros da série temporal. De modo a reconhecer as componentes da série temporal de forma isolada, é frequente a separação da tendência em subtendências, proporcionando previsões mais precisas e uma melhor compreensão do comportamento da série (Makridakis, 1998, p. 82-84).
A ciclicidade e a sazonalidade são duas componentes distintas da tendência que, normalmente, caracterizam as séries económicas e comerciais através dos métodos de decomposição. A sazonalidade, consiste numa flutuação periódica da variável, causada, por exemplo, pela temperatura, pluviosidade, mês do ano, feriados ou politicas empresariais. Quando ocorrem mudanças a longo prazo no nível da série, está-se perante uma situação de ciclicidade. Habitualmente, a ciclicidade é separada em componentes de tendência e cíclicos, distinção sempre algo artificial, integrando os dois efeitos num único componente, a ciclicidade.
A decomposição pressupõe que os dados são compostos como se segue:
Dados = tendência + erro = (ciclicidade, sazonalidade, erro)
Assim, a presença de um elemento de erro ou aleatoriedade é também assumida, em adição aos componentes da tendência. Este erro é, normalmente, apelidado de componente «irregular» ou «resto» e, caracteriza-se por ser a diferença entre o efeito combinado das duas subtendências da série e os dados reais.
Para isolar cada componente da série com a maior precisão possível, há várias alternativas de decompor uma série temporal. Esta separação consiste em remover a ciclicidade, isolando a componente sazonal numa fase posterior. Qualquer resíduo é considerado aleatório, sendo possível a sua identificação, apesar da sua previsão ser impossível. Apesar das fragilidades existentes na abordagem da decomposição, do ponto de vista estatístico, na prática, esta tem sido usada com um sucesso notável, ignorando estas fraquezas.
Técnicas de previsão/Princípios
Logística/Técnicas de previsão/Princípios
Técnicas de previsão/Médias móveis
Logística/Técnicas de previsão/Médias móveis
Técnicas de previsão/Médias móveis/Média móvel simples
Logística/Técnicas de previsão/Médias móveis/Média móvel simples
Técnicas de previsão/Médias móveis/Média móvel centrada
Logística/Técnicas de previsão/Médias móveis/Média móvel centrada
Técnicas de previsão/Médias móveis/Média móvel ponderada
Logística/Técnicas de previsão/Médias móveis/Média móvel ponderada
Técnicas de previsão/Alisamento local de regressão
Logística/Técnicas de previsão/Alisamento local de regressão
Técnicas de previsão/Decomposição clássica
Logística/Técnicas de previsão/Decomposição clássica
Técnicas de previsão/Métodos do Census Bureau
Logística/Técnicas de previsão/Métodos do Census Bureau
Técnicas de previsão/Decomposição STL
Logística/Técnicas de previsão/Decomposição STL
Técnicas de previsão/Alisamento exponencial
Quando o custo de armazenamento de dados em computador era muito elevado, a utilização de médias móveis exponencialmente ponderadas, ou seja, alisamento exponencial, era muito vantajosa. Apesar desses custos terem deixado de ser uma grande preocupação o alisamento exponencial continua a ser muito popular. O alisamento exponencial refere-se a um conjunto de métodos de previsão, alguns dos quais são amplamente utilizados e, por isso, importantes. Os métodos de alisamento exponencial com a tendência e a sazonalidade ajustadas são utilizados em muitos sistemas de previsão computadorizados da produção, existências, distribuição e planeamento no retalho. Brown, Holt e Winters iniciaram o desenvolvimento do alisamento exponencial (Delurgio, 1998, p. 153-154).
Segundo Casaca (2008, p. 18), o modelo de alisamento exponencial simples (AES) é apropriado quando a procura não apresenta tendência ou sazonalidade. Por ser um modelo constante, é apropriado para séries que são caracterizadas localmente pelo seu nível, acrescentado de uma variação aleatória desprezável, ou seja, as mudanças ocorridas numa série neste formato são bastante lentas. Este modelo caracteriza-se por ser aplicável a séries localmente estacionárias, ponderando todos os valores históricos da série com pesos sucessivamente menores à medida que estes se afastam do valor mais recente.
O alisamento exponencial simples é fácil de aplicar. De acordo com Delurgio (1998, p. 154-155), as previsões através do AES exigem apenas três dados: a previsão mais recente, o valor real mais recente e uma constante de alisamento. A constante de alisamento, , determina o peso dado às observações passadas mais recentes e, por conseguinte, controla a taxa de alisamento ou da média. O seu valor está, geralmente, restrito ao intervalo [0; 1]. A fórmula do AES pode ser expressa por:
Onde:
= Previsão para o periodo | |
= Valor real para o periodo | |
= Previsão para o periodo | |
= Constante de alisamento |
Supondo que uma empresa deseja prever a procura para um produto usando o AES com um de 0,4 e sabendo que a procura real do mês passado foi de 800 unidades e a previsão era de 700 unidades, pretende-se saber qual a previsão para este mês.
= unidades
A fórmula indica que a previsão é igual à média ponderada dos valores mais recentes: real e previsto. Alfa () é o peso relativo dado a cada termo da equação (1). Com alfa igual a 0,4, a previsão representa 40 % do valor real mais recente e 60 % do valor da previsão mais recente. Para atingir o nível da média ou alisamento desejado, assim se escolhe o valor de .
Continuando o exemplo acima, suponha-se que a procura para o período , foi na realidade de 760. Qual é a previsão para o período ?
= unidades
E se
Então,
= unidades
Outra forma igualmente simples de calcular o AES é através da equação:
De acordo com esta fórmula, a previsão actual é igual à previsão do período anterior mais uma fracção do erro na previsão anterior. É de notar, no entanto, que as equações (1) e (2) são a mesma equação escrita com os termos combinados de maneiras diferentes.
A utilização do AES requer a escolha de uma constante de alisamento, uma previsão inicial e um valor real. A escolha da constante de alisamento não deve ser arbitrária. A verdade é que em algumas situações a selecção de uma constante de alisamento pode não ser importante, sendo aceitáveis valores entre 0,1 e 0,5. Muitas vezes a escolha de pode ser muito importante. Com computadores de baixo custo e erros de previsão com custos elevados, não é aconselhável escolher um valor de conveniente ou típico. Em vez disso, o melhor deve ser escolhido com base no valor mínimo de soma de erros quadráticos. Nos exemplos que se seguem será usado um de 0,4.
O passo seguinte no processo, após escolher uma constante de alisamento, é escolher um valor de previsão inicial. Normalmente, o primeiro valor real é escolhido como a previsão para o segundo período. Considere-se a seguinte situação:
Período | Valor real | Valor previsto |
1 | 700 | |
2 | 800 | 700 |
Para calcular a previsão para o período 3, supõe-se que o valor inicial previsto para o período 2 é igual ao valor real para o período 1.
Então,
=
= unidades
Este método é muito comum e eficiente para o AES, embora a previsão inicial possa ser ser obtida por outros métodos.
A constante de alisamento atribui os pesos relativos ao valor mais recente, real e previsto. O alisamento exponencial também pode ser chamado de média exponencial, uma vez que alisamento e cálculo da média são sinónimos em previsões. Um valor alisado exponencialmente não é mais que uma média móvel ponderada de todos os valores reais passados. Assim, a constante de alisamento, , determina o peso exponencial da realidade passada. Os primeiros quatro pesos, quando é 0,4 são dados na Tabela 2.
Antiguidade das observações | Pesos |
Mais recente | = 0,4000 |
Um período antes | (1 - ) = 0,2400 |
Dois períodos antes | (1 - )(1 - ) = 0,1440 |
Três períodos antes | (1 - )(1 - )(1 - ) = 0,0864 |
Segundo Casaca (2008, p. 18), para um alisamento constante, os pesos comportam-se como uma função exponencial decrescente. À observação mais recente é dado maior peso e a soma das ponderações deve ser igual a 1. Assim, o sistema de pesos fica dependente de um único parâmetro () e corresponde-lhe um decaimento exponencial dos pesos com a antiguidade das observações, sendo essa redução dos pesos tão mais rápida quanto mais elevado for o valor de [1].
A abordagem de alisamento exponencial tem sido aplicada com sucesso em praticamente todos os tipos de negócio, dada a sua facilidade de utilização. No entanto, o valor adequado da constante de alisamento pode fazer a diferença entre uma previsão exacta e uma previsão imprecisa (Heizer et al., 2004, p. 112).
Relativamente à constante de alisamento () podem destacar-se as seguintes características (Casaca, 2008, p. 18-19):
- Quanto maior a constante de alisamento, maior o peso dado às observações mais recentes;
- A soma das ponderações é igual a um;
- Quanto maior for a constante de alisamento, mais rápida é a convergência para a unidade;
- No método do alisamento exponencial, atribuir o valor de 1 ou 0 ao alfa, seria a contradição do próprio método;
- A nova previsão será muito próxima da previsão anterior, quando o alfa é próximo de zero;
- Deve-se usar um valor reduzido para o alfa, caso o objectivo seja obter uma previsão estável e que alisa toda a variação aleatória;
- Um valor de alfa elevado, deve ser usado, quando o objectivo é obter uma rápida resposta a alterações rápidas no comportamento das observações;
Em relação aos modelos de médias móveis o AES apresenta a vantagem de depender de um só parâmetro (). Uma outra vantagem traduz-se no facto de a fórmula de recorrência permitir actualizar de forma rápida o valor da média móvel quando é conhecida uma nova observação, bastando para isso conhecer o valor anterior dessa média móvel.
Segundo Tavares et al. (1996, p. 251-252) a última vantagem referida tem como consequência uma enorme poupança nos volumes de informação a manter. Um exemplo ilustrativo desta situação é um sistema informático de gestão de stocks envolvendo milhares de artigos em que as previsões das vendas são efectuadas de forma rotineira. Recorrendo a um modelo de médias móveis aritméticas a quantidade de informação a manter revela-se bastante grande. Um modelo de médias móveis pesadas exponencialmente obriga a manter apenas 2 valores por artigo.
O alisamento exponencial é uma das técnicas mais utilizadas na previsão, em parte devido aos seus requisitos mínimos de armazenamento de dados e facilidade de cálculo e, também, devido à facilidade com que o sistema de ponderação pode ser alterado através da variação do valor de (Stevenson, 1996, p. 479).
Técnicas de previsão/Regressão simples
De acordo com Sousa (2009, p. 15), deve-se utilizar a regressão linear simples quando se está perante amostras com duas variáveis, e cujos valores estão relacionados de forma linear entre si. Exemplos típicos da regressão linear são a relação entre altura e peso de uma pessoa, ou o diâmetro do tronco e a altura de uma árvore. Em ambos os casos tem-se uma variável que depende linearmente da outra.
Sousa (2009, p. 15) define regressão linear simples como um modelo de relação entre uma variável aleatória dependente e uma variável independente , com a seguinte expressão:
Onde:
: | variável dependente ou explicada; |
: | variável independente ou explicativa, cujos erros de medição são assumidos desprezáveis; |
: | valor da ordenada na origem; |
: | declive; |
: | erro que resulta do facto de ter características aleatórias. |
Assume-se
Os parâmetros da recta de regressão a serem estimados são e .
Segundo Ferreira (2010, p. 94) e Sousa (2009, p. 8), pelo método dos mínimos quadrados (Figura 1), as estimativas dos parâmetros e são dadas por:

Onde:
: | variabilidade de , dada por |
: | variabilidade entre e , dada por |
: | média das observações da variável , dada por |
: | média das observações da variável , dada por |
: | número de observações. |
Segundo Henriques (2009, p. 32), a equação de regressão deve ser vista como uma tentativa de explicação das variações da variável dependente, que são resultado de variações na variável independente.
Seja a média das observações registadas para a variável dependente. Uma previsão baseada no modelo de regressão deve ter mais qualidade do que uma previsão baseada em .
Se a dispersão (ou erro) associado à equação da recta de regressão é muito menor do que a dispersão (ou erro) associada a , as previsões do modelo de regressão são melhores do que as previsões baseadas na média das observações registadas.
Para medir a qualidade do ajustamento da recta de regressão calculada (Sousa, 2009, p. 15) define-se uma quantidade, a que se chama de coeficiente de determinação, que é calculada da seguinte forma:
Onde:
: | coeficiente de determinação; |
: | variabilidade de , e é dada por . |
Segundo Sousa (2009, p. 15), representa a percentagem da variabilidade dos dados observados que é explicada pela recta de regressão e pode tomar qualquer valor no intervalo de 0 a 1. Um valor do coeficiente de determinação igual a (ou próximo de) 1 significa que se tem um ajuste perfeito da recta de regressão calculada aos dados observados. Um valor do coeficiente de determinação igual a (ou próximo de) 0 significa um mau ajuste da recta de regressão aos dados. Henriques (2009, p. 35) considera que neste caso se está perante uma relação não linear entre as duas variáveis.
Henriques (2009, p. 35) define ainda o coeficiente de correlação simples, , dado por:
Onde o sinal de positivo ou negativo é o mesmo que o sinal do declive .
O valor de pode tomar qualquer valor no intervalo de -1 a 1, onde r = 1 ou r = -1 indicam uma relação linear perfeita (positiva e negativa, respectivamente) entre as duas variáveis, r = 0 indica uma relação não linear entre as duas variáveis ou mesmo a inexistência de uma relação entre as mesmas, e r < 0 indica uma relação linear negativa e r > 0 indica uma relação linear positiva entre as variáveis e .
De acordo com Henriques (2009, p. 16), a regressão linear deve ser utilizada com cautela, pois um conjunto de pontos mostra a existência de uma relação linear entre as duas variáveis apenas para os valores do conjunto de dados. Para valores fora desse conjunto, não há nenhuma prova de linearidade. Pode ser incorrecto utilizar a recta de regressão estimada para prever valores da variável dependente correspondentes a valores da variável independente que estão fora do âmbito dos dados recolhidos.
Adnan et al. (2003, p. 30) refere que podem existir termos de erro que não tem distribuição normal, nem estão independentemente distribuídos. Nestes casos, poderá ocorrer distorção da recta de regressão e, consequentemente, valores dos parâmetros de regressão com erros. Estas aberrações (outliers) que parecem inconsistentes com o restante conjunto de dados podem ter uma grande influência na análise estatística e, consequentemente, na recta de regressão estimada. Para Rosado (2009, p. 13) o outlier é frequentemente o valor máximo ou mínimo da amostra, embora a discordância de valores possa não se manifestar exclusivamente nos extremos.
Para Maia (2004, p. 2), quando duas variáveis são correlacionadas, podem-se prever valores de uma variável em função do valor da outra variável, embora isso possa levar à conclusão errada de que uma variável é verdadeiramente a causa da variação da outra. De acordo com esse autor, não é possível provar uma relação de causa-efeito entre ambas as variáveis, mesmo havendo uma expressão matemática que relacione uma variável com a outra. Há, portanto, três explicações plausíveis para a existência de um modelo matemático que relaciona ambas as variáveis:
- Existência de uma relação efectiva de causa-efeito entre as variáveis;
- As duas variáveis relacionam-se com uma terceira variável;
- A correlação matemática obtida é fruto do acaso.
Maia (2004, p. 2) dá o seguinte exemplo para a terceira hipótese: há estudos que revelam alta correlação entre a variação do comprimento das saias das senhoras e a as movimentações da bolsa de Nova Iorque, ou entre os nascimentos na Inglaterra e a produção de gusa nos Estados Unidos.
Técnicas de previsão/Regressão múltipla
Sousa (2009, p. 20) define regressão linear múltipla como uma relação entre uma variável aleatória dependente, , e variáveis independentes, , , …, , com a seguinte expressão:
Onde, tal como no caso da regressão simples, se utiliza o método dos mínimos quadrados para determinar os parâmetros
De acordo com Henriques (2009, p. 22), a expressão acima pode ser re-escrita na forma matricial como:
Onde:
: | matriz das observações da variável dependente; |
: | matriz das observações da variável independente, ou matriz significativa do modelo; |
: | vector dos parâmetros de regressão a serem estimados; |
: | vector do erro que resulta do facto de ter características aleatórias. |
Admite-se que , , ..., são variáveis aleatórias independentes de média 0 e desvio padrão .
Da mesma forma que na regressão simples se utiliza o método dos mínimos quadrados para estimar os parâmetros da regra de regressão, o mesmo acontece na regressão múltipla, da qual se obtém que o vector dos parâmetros da regressão é dado por:
Caso ocorra , está-se perante um problema de regressão linear simples, que também pode ser resolvido desta forma.
Um exemplo de regressão múltipla, dado por Henriques (2009, p. 18), é a relação entre o volume de vendas efectuadas num período de tempo por um vendedor, os seus anos de experiência, e a sua pontuação num teste de inteligência.
Técnicas de previsão/Métodos ARIMA de Box-Jenkins
Etapas de desenvolvimento - 9 fases | ||||||||
---|---|---|---|---|---|---|---|---|
Início: ![]() |
Básico: ![]() |
Criação: ![]() |
Desenvolvimento: ![]() |
Maturação: ![]() |
Revisão: ![]() |
Desenvolvido: ![]() |
Finalização: ![]() |
Abrangente: ![]() |
Os modelos Autorregressivos Integrados de Médias Móveis, Autoregressive / Integrated / Moving Average (ARIMA) geram previsões através da informação contida na própria série cronológica (Hanke et al., 2008, p. 399). George Box e Gwilym Jenkins tornaram populares os modelos ARIMA no início dos anos 70, sendo os seus nomes usados, frequentemente, como sinónimos dos modelos ARIMA gerais, aplicados à análise de séries cronológicas e previsões. Os fundamentos teóricos são bastante sofisticados, mas é possível um entendimento claro da essência da metodologia ARIMA por parte de pessoas que não dominem técnicas estatísticas (Makridakis et al., 1998, p. 312).
Existe uma grande variedade de modelos ARIMA. O modelo geral sem a componente de sazonalidade é conhecido como ARIMA(p,d,q) (Makridakis et al., 1998, p. 336-337):
AR: | p = ordem da componente autorregressiva |
I: | d = grau da diferenciação |
MA: | q = ordem da componente média móvel |
Um modelo de ruído branco é classificado como ARIMA(0,0,0) porque não apresenta componente autorregressiva (AR), não envolve nenhuma diferenciação e também não apresenta a componente média móvel.
Utilizando o mesmo raciocínio, um modelo de passeio aleatório é classificado como ARIMA(0,1,0), pois não apresenta componentes autorregressiva e de média móvel, envolvendo apenas uma diferenciação.
De realçar que, se p, d ou q forem iguais a zero, o modelo pode ser escrito de forma abreviada, ignorando as componentes ausentes. Por exemplo, um modelo ARIMA(2,0,0) pode ser escrito como AR(2) pois não existe diferenciação, nem componente de média móvel.
A metodologia Box-Jenkins, utiliza uma estratégia de construção de modelo de forma iterativa que consiste na selecção de um modelo inicial, cálculo dos coeficientes do modelo e por fim análise dos resíduos. Caso seja necessário, o modelo inicial é modificado e o processo é repetido até que a análise dos resíduos mostre que não se justifica nova alteração. Neste ponto, o modelo obtido, pode ser usado para previsões (Hanke et al., 2008, p. 407).
Identificação do modelo
Estimativa dos coeficientes
Verificação do modelo
Aplicação do modelo em previsões
Técnicas de previsão/Modelos avançados de previsão
Logística/Técnicas de previsão/Modelos avançados de previsão
Técnicas de previsão/Previsão a longo prazo
Etapas de desenvolvimento - 9 fases | ||||||||
---|---|---|---|---|---|---|---|---|
Início: ![]() |
Básico: ![]() |
Criação: ![]() |
Desenvolvimento: ![]() |
Maturação: ![]() |
Revisão: ![]() |
Desenvolvido: ![]() |
Finalização: ![]() |
Abrangente: ![]() |
- Métodos de previsão subjectivos
Técnicas de previsão/Dinâmica de grupo
Logística/Técnicas de previsão/Dinâmica de grupo
Técnicas de previsão/Intenções
De acordo com Morwitz (2001, p. 33), intenções são medidas dos objectivos, planos ou expectativas de indivíduos, acerca de acontecimentos futuros. São utilizadas para elaborar previsões devendo ser cumpridos certos princípios, nomeadamente:
- Em relação às medições das intenções: as intenções devem ser medidas utilizando escalas probabilísticas e os inquiridos devem ser alertados para se concentrarem nas suas características quando respondem sobre as suas intenções.
- Relativamente ao uso das intenções para determinar previsões do comportamento: as intenções devem ser ajustadas de modo a remover enviesamentos. Os inquiridos devem ser divididos em classes antes de ajustar as intenções e podem ser utilizadas para desenvolver tanto as previsões mais optimistas como as mais pessimistas.
- Em relação ao facto dos investigadores deverem ser cautelosos na utilização dos dados: a medição das intenções pode alterar o comportamento dos inquiridos e aqueles que erram ao relembrar a decisão anterior podem fazer predições erradas sobre as suas decisões futuras.
Algumas empresas medem com frequência as intenções de indivíduos de forma a determinar uma previsão do seu comportamento, por exemplo, nos estudos de mercado costuma-se medir as intenções de compra dos clientes, com o objectivo de determinar a previsão das vendas do produto.
Apesar da investigação sobre as intenções do consumidor terem sido iniciados a partir dos anos 50, ainda existem algumas questões importantes sobre a validade predictiva destas medições que continuam por responder (Morwitz, 2001, p. 52).
Técnicas de previsão/Opinião de peritos
Etapas de desenvolvimento - 9 fases | ||||||||
---|---|---|---|---|---|---|---|---|
Início: ![]() |
Básico: ![]() |
Criação: ![]() |
Desenvolvimento: ![]() |
Maturação: ![]() |
Revisão: ![]() |
Desenvolvido: ![]() |
Finalização: ![]() |
Abrangente: ![]() |
A forma mais básica de previsão por análise qualitativa é a perspicácia, na qual um indivíduo informado utiliza a sua experiência pessoal ou profissional para elaborar expectativas futuras. Apesar desta abordagem ser subjectiva, a opinião de um indivíduo informado pode fornecer conhecimentos valiosos (Hirschey, 2009, p. 204). A grande questão é como obter as melhores previsões a partir das opiniões de peritos. Uma solução requer a utilização de uma técnica de grupo estruturada, denominada método de Delphi, para obter e combinar as opiniões de peritos (Rowe, 2001, p. 125).
Técnicas de previsão/Opinião de peritos/Método Delphi
Segundo DeLurgio (1998, p. 636), o método Delphi é aplicável quando se pretende prever a probabilidade e a data de acontecimentos futuros. Para fazer essas previsões, junta-se um grupo de peritos de modo a identificar acontecimentos emergentes, a sua probabilidade e quando é que ocorrerão. Os principais objectivos deste método inclui a criação de consensos e a identificação de opiniões opostas relativamente a futuros alternativos. Na maioria dos casos, chega-se a uma previsão consensual no final do processo. O método Delphi, sendo um dos métodos qualitativos mais conhecidos, é eficaz, uma vez que as sondagens estruturadas e independentes dos peritos fornecem estimativas não enviesadas de futuros alternativos.
Desde que foi desenvolvido na RAND Corporation, na década de 50, o método Delphi tem sido utilizado para facilitar a elaboração de previsões assim como a tomada de decisões. Este método foi inicialmente criado como um procedimento capaz de ajudar peritos a obterem melhores previsões, do que poderiam obter através de reuniões de grupo tradicionais. A sua estrutura foi criada de forma a ter acesso aos atributos positivos de grupos em interacção, como, por exemplo, o conhecimento de várias fontes e sínteses criativas. Ao mesmo tempo, o método Delphi permite contornar os aspectos negativos que muitas vezes levam a desempenhos sub-óptimos dos grupos, tais como os resultantes de conflitos sociais, pessoais ou políticos (Rowe, 2001, p. 126).
Na primeira ronda os peritos têm que responder por escrito a questões apresentadas, separadamente uns dos outros, ou seja, estes são respondidos independentemente. As respostas de cada perito são resumidas e devolvidas aos mesmos, com o objectivo de estes analisarem os resultados e modificarem os seus comentários para a ronda seguinte. De seguida, realizam-se três ou mais rondas da mesma forma. Assim que os administradores acharem que os peritos desenvolveram adequadamente as suas posições, estes podem trabalhar em conjunto para aperfeiçoar as suas respostas e projeções. Após a conclusão do processo, os patrocinadores devem conhecer as probabilidades de acontecimentos futuros de forma a aperfeiçoar o planeamento organizacional. A principal vantagem desta técnica de previsão assenta na imparcialidade com que os peritos por todo o mundo podem partilhar ideias e suposições (DeLurgio, 1998, p. 636).
O método Delphi possui quatro características fundamentais, nomeadamente o anonimato, a iteração, feedback controlado das opiniões dos peritos e agregação estatística das respostas dos membros do grupo. Para alcançar o anonimato devem-se utilizar questionários, nos quais os membros do grupo podem expressar as suas ideias individualmente, diminuindo, deste modo, os efeitos de pressões pessoais, a presença de indivíduos dogmáticos ou dominantes ou o efeito da maioria. Através das iterações dos questionários ao longo de várias rondas, os peritos têm a possibilidade de mudarem de opinião sem receio da opinião dos outros elementos anónimos do grupo. É de notar que o administrador informa os participantes das opiniões dos colegas anónimos entre cada iteração de um questionário. Este feedback é apresentado como um sumário estatístico da resposta do grupo, como por exemplo, a estimativa da média de quando um acontecimento futuro irá ter lugar. No final do processo, o administrador determina a opinião final do grupo, que é baseada na média estatística das opiniões da última ronda (Rowe, 2001, p. 126).
O método Delphi torna-se particularmente vantajoso em determinadas situações, como por exemplo, quando os peritos se encontram geograficamente dispersos e impossibilitados de se reunirem em grupo. Neste caso, esta técnica possibilita aos membros de diferentes organizações debaterem problemas e elaborarem previsões à distância. Outro caso onde a utilização deste método se torna útil, é quando existem desacordos entre indivíduos, os quais podem ser influenciados por conflitos de motivações, choques de personalidade ou jogos de poder. A gestão do processo de grupo e a garantia do anonimato são factores que devem ser tidos em conta para garantir o sucesso deste último caso. É de notar que peritos de diversas origens sem um historial de comunicação, são mais susceptíveis de terem diferentes perspectivas, terminologias e referenciais, podendo facilmente contribuir para que haja problemas na comunicação (Rowe 2001, p. 138).
Técnicas de previsão/Análise conjunta
A análise conjunta é um método baseado numa pesquisa, realizada por gestores, tendo em conta a perspectiva do cliente. Tem como objectivo auxiliar na tomada de decisões relativamente à criação de um novo produto e é, especialmente, utilizada na área do marketing, com o objectivo de quantificar a atitude dos clientes quando têm várias alternativas disponíveis no mercado (Wittink et al., 2001, p. 147).
Esta metodologia envolve a elaboração das questões e administração e análise das respostas, de modo a identificar quais as características que fariam o público-alvo optar por determinado produto em detrimento de um outro, como, por exemplo, o preço, os benefícios ou as características de determinado produto (Armstrong, 2001, p. 145).
Uma vez obtidos os dados relevantes a uma pesquisa, os investigadores conseguem ter uma visão geral sobre as preferências do consumidor. Estas são fundamentais para que os investigadores explorem o potencial do mercado para um novo produto, antes de tomarem qualquer decisão. No entanto, estas previsões dependem de vários factores, entre os quais a disponibilidade dos produtos que estão incluídos num cenário de mercado para cada cliente e a percepção do cliente relativamente a estes produtos (Wittink et al., 2001, p. 147-148).
É de notar que a complexidade prática envolvida nesta técnica torna difícil a obtenção de conjuntos de resultados fiáveis, por parte dos investigadores (Wittink et al., 2001, p. 147).
A análise conjunta teve origem na psicologia matemática, na qual os investigadores estavam interessados em determinar as condições em que poderiam obter hard output a partir de soft input. Quando este método começa a ser utilizado por empresas, pretendia-se determinar a importância dos atributos e o preço dos produtos. Posteriormente, foi usado para simular as preferências dos clientes e prever respostas do mercado relativamente a mudanças nos produtos da empresa ou das concorrentes (Armstrong, 2001, p. 145-146).
Técnicas de previsão/Análise conjunta/Pesquisa de mercado
Logística/Técnicas de previsão/Análise conjunta/Pesquisa de mercado
Técnicas de previsão/Análise conjunta/Pesquisa de mercado/Pesquisa qualitativa
Logística/Técnicas de previsão/Análise conjunta/Pesquisa de mercado/Pesquisa qualitativa
Técnicas de previsão/Análise conjunta/Pesquisa de mercado/Pesquisa quantitativa
Logística/Técnicas de previsão/Análise conjunta/Pesquisa de mercado/Pesquisa quantitativa
Técnicas de previsão/Metodologia bootstrap
A metodologia bootstrap é um sistema pericial que traduz as regras de um perito para um modelo quantitativo. Esta tradução é efectuada por regressão das previsões do perito em relação à informação que este usou. Na realidade, esta metodologia infere o modelo do perito através da análise das previsões realizadas pelos mesmos (Armstrong, 2001, p. 171).
Esta ferramenta torna-se, particularmente, útil quando existem poucos dados históricos ou quando estes têm pouca qualidade e é mais apropriada para situações complexas, nas quais as opiniões dos peritos inspiram pouca confiança. Caso seja necessário elaborar várias previsões, a metodologia torna-se económica. Permite, também, identificar enviesamentos nas previsões dos peritos, assim como revela a maneira como os mehores peritos as efectuam.
Alguns estudos mostram que a metodologia bootstrap melhorou a qualidade das decisões na produção em empresas.
Na metodologia bootstrap, os peritos efectuam previsões sobre situações reais ou simuladas e são utilizados meios estatísticos para inferir os modelos de previsão. Esta metodologia utiliza as previsões dos peritos como variável dependente e as pistas como variáveis causais. O modelo é normalmente estimado a partir da regressão dos mínimos quadrados (Armstrong, 2001, p. 173):
...
De maneira a desenvolver uma metodologia bootstrap é necessário seguir determinados princípios (Armstrong, 2001, p. 173-177):
- Incluir todas as variáveis que o perito possa usar;
- Quantificar as variáveis causais;
- Utilizar os melhores peritos;
- Verificar se as variáveis estão correctas;
- Estudar mais que um perito;
- Utilizar peritos com ideias diferentes;
- Utilizar uma amostra suficientemente grande de stimulus cases;
- Utilizar stimulus cases que cobrem a maioria das possibilidades razoáveis;
- Utilizar stimulus cases que apresentem ligeiras intercorrelações, mas que sejam realistas;
- Utilizar análises simples para representar o comportamento;
- Efectuar uma monitorização formal.
A metodologia bootstrap apresenta previsões mais fiáveis do que a opinião simples dos peritos especialmente quando (Armstrong, 2001, p. 188):
- O problema de previsão é complexo;
- As relações de bootstrap podem ser estimadas com confiança;
- Os peritos têm vastos conhecimentos sobre as relações;
- A alternativa é obter previsões de peritos com pouco experiência.
A metodologia bootstrap é uma técnica com uma certa utilidade, visto que é simples, tem um baixo custo associado e os resultados são bastante fiáveis.
Técnicas de previsão/Analogias
Logística/Técnicas de previsão/Analogias
Técnicas de previsão/Extrapolação
Logística/Técnicas de previsão/Extrapolação
Técnicas de previsão/Redes neuronais
As redes neuronais artificiais são baseadas em modelos matemáticos simples da forma expectável do funcionamento do cérebro humano. Quando aplicadas a séries cronológicas, permitem criar um modelo de previsão não linear. A previsão por redes neuronais apesar de requerer,geralmente, um número de observações mais elevado do que outros métodos, permite o ajuste de modelos mais flexíveis e complicados. Os analistas que usam este método adoptam uma terminologia bastante diferente da usada por outros métodos em técnicas de previsão, o que conduz a alguma confusão. Por exemplo, em vez de modelo, parâmetros e cálculo de parâmetros tem-se rede, pesos e treino da rede, respectivamente. Uma rede neuronal pode ser vista como uma rede de unidades parecidas com os neurónios organizada por camadas. A camada inferior consiste num conjunto de unidades de input enquanto que, a camada superior consiste num conjunto de unidades de output. As unidades de cada camada estão ligadas às unidades das camadas superiores(Makridakis et al., 1998, p. 435-439).
A especificação de uma rede neuronal é feita através dos seguintes componentes:
- Arquitectura. Número de camadas e unidades na rede e a forma de ligação.
- Funções de activação. Descrevem como cada unidade combina os inputs para gerar um output.
- Função custo. Medida de exactidão da previsão, por exemplo, a Estimativa dos Mínimos Quadrados (MSE).
- Algoritmo de treino. Procura os valores dos parâmetros que minimizam a função custo.
O poder desta ferramenta pode ser visto quando se adicionam camadas intermédias que consistem em unidades não lineares escondidas entre os inputs e os outputs.
A resposta de uma unidade é denominada de valor de activação. A escolha da função de activação não linear recai, normalmente, numa combinação de uma função linear dos inputs seguida de uma função squashing não linear denominada sigmoid. Por exemplo, os inputs de uma unidade escondida, podem ser combinados linearmente para dar:
que, por sua vez, é um input de uma função não linear:
Um benefício da função sigmoid é o facto de reduzir o efeito de valores extremos de input, conferindo, desta forma, um certo grau de robusteza à rede.
A camada de input de uma rede consiste, normalmente, em tantas variáveis explicativas quanto razoavelmente possível em adição a valores desfasados da série cronológica. Para dados sazonais, é prática geral ter tantos inputs desfasados quantos os períodos da sazonalidade. O número de unidades na camada de output corresponde ao número de variáveis a prever.
Uma desvantagem dos métodos de redes neuronais é o facto de não permitirem muita compreensão dos dados uma vez que não existe um modelo explícito. Permitem uma abordagem black box à previsão. Por outro lado, pode funcionar em situações onde uma abordagem baseada num modelo explícito falhe. De facto, as redes neuronais são encaradas como uma esperança em adaptar irregularidades e características incomuns na série cronológica em estudo.
Técnicas de previsão/Previsão baseada em regras
A previsão baseada em regras, Rule Based Forecating (RBF), é um sistema pericial que utiliza o conhecimento do domínio para combinar as previsões de vários métodos de extrapolação, ou seja, utiliza decisões estruturadas para adaptar os métodos de extrapolação às situações e o conhecimento sobre previsões adquirido pela investigação ao longo da última metade do século XX. As ponderações que se devem atribuir às previsões são feitas através da utilização de regras de produção (if-then). Para identificar as características da situação e ajustar as ponderações de maneira a coincidir as características com os pressupostos subjacentes aos métodos, recorre-se à parte condicional (if) das regras (Armstrong et al., 2001, p. 260).
Quando esta técnica se baseia no conhecimento do domínio e este for importante, a série temporal tiver um bom comportamento, houver uma forte tendência nos dados e o horizonte de previsão for dilatado, torna-se particularmente útil. As previsões RBF têm um erro associado, que em condições ideais é um terço menor do que o da combinação de pesos iguais, e não se verificando é idêntico ao atingido com a utilização de outros métodos. Algumas das regras da RBF podem ser utilizadas conjuntamente com procedimentos de extrapolação tradicionais (Armstrong et al., 2001, p. 259).
A metodologia RBF baseia-se em três aspectos fundamentais, recolha do conhecimento, formulação das regras e o ajuste dos elementos. Relativamente à recolha do conhecimento, deve-se utilizar a perícia na elaboração de previsões para obter conhecimento sobre as regras e protocolos para identificar conhecimentos sobre as regras. Na formulação das regras devem-se considerar os seguintes aspectos: considerar a tendência e a amplitude separadamente, utilizar métodos de extrapolação simples, combinar previsões, utilizar modelos diferentes para previsões a curto e longo prazo e amortecer a tendência à medida que o horizonte temporal aumenta. Os ajustes efectuados aos elementos da RBF devem ser feitos tanto nas regras associadas ao if, como nas do then. Nas regras associadas ao if deve-se decompor as séries temporais caso seja possível elaborar previsões tão bem como para as séries alvo, recorrer às características dos dados históricos das séries temporais e utilizar o conhecimento do domínio para descrever as condições que afectaram ou afectarão as séries temporais e para ajustar as observações aos eventos. Por sua vez, as regras associadas ao then necessitam de recorrer á extrapolação de todas as tendências para reforçar as séries, atribuir pouca importância a tendências em séries opostas, não utilizar a tendência histórica caso as tendências esperadas sejam opostas às tendências estimadas historicamente, utilizar uma estimativa conservadora da tendência caso as tendências básica e recente sejam inconsistentes, efectuar o ajuste dos pesos da extrapolação ao intervalo de tempo das séries e da estimativa do nível na direcção implícita nas forças causais, e por fim deve-se dar mais peso à última observação quando se estima os níveis para um modelo a curto prazo, particularmente na presença de descontinuidades(Armstrong et al., 2001, p. 260-272).
A maior desvantagem desta técnica é o facto de apresentar um custo elevado relativamente aos métodos normais de extrapolação. Todavia, esta consegue ser menos dispendiosa que os métodos econométricos. Uma outra desvantagem desta técnica está relacionada com o facto de utilizar dados históricos, uma vez que implica que as regras impostas tenham de ser cuidadosamente calibradas para esses dados (Armstrong et al., 2001, p. 275).
Os resultados empíricos obtidos em múltiplos conjuntos de séries temporais demonstram que a RBF apresenta previsões mais precisas do que as extrapolações obtidas pelos métodos tradicionais (Armstrong et al., 2001, p. 259).
Técnicas de previsão/Sistemas periciais
Logística/Técnicas de previsão/Sistemas periciais
Técnicas de previsão/Integração, ajustamento e combinação
Logística/Técnicas de previsão/Integração, ajustamento e combinação
Sistemas de informação
Etapas de desenvolvimento - 9 fases | ||||||||
---|---|---|---|---|---|---|---|---|
Início: ![]() |
Básico: ![]() |
Criação: ![]() |
Desenvolvimento: ![]() |
Maturação: ![]() |
Revisão: ![]() |
Desenvolvido: ![]() |
Finalização: ![]() |
Abrangente: ![]() |
Introdução
Custo logístico
Processamento de encomendas
Rastreabilidade (RMBeatriz)
Indicadores de desempenho
Valor Económico Acrescentado (EVA)
Indicadores AECOC
Taxa de rotação dos stocks
Indicadores de utilização de recursos: pessoas
Indicadores de utilização de recursos: equipamentos
Indicadores de controlo de gestão: movimento
Indicadores de controlo de gestão: movimento/Movimento por operação
- Distância média por movimento
Sistemas de informação/Introdução
Sistema de informação logística é uma ferramenta que interliga as atividades logísticas num processo integrado. Este processo integrado é constituído por quatro níveis de funcionalidade: transacções, controlo de gestão, analise de decisão e planejamento estratégico (Bowersox et al., 1996, p. 194).
Papel da Informação na Logística
O fluxo de informações é um elemento de grande importância nas operações logísticas. Pedidos de clientes e de ressuprimento, necessidades de estoque, movimentações nos armazéns, documentação de transporte e faturas são algumas das formas mais comuns de informações logísticas.
Antigamente, o fluxo de informações baseava-se principalmente em papel, resultando em uma transferência de informações lenta, pouco confiável e propensa a erros. O custo decrescente da tecnologia, associado a sua maior facilidade de uso,permitem aos executivos poder contar com meios para coletar, armazenar, transferir e processar dados com maior eficiência,eficácia e rapidez.
A transferência e o gerenciamento eletrônico de informações proporcionam uma oportunidade de reduzir os custos logísticos através da sua melhor coordenação. Além disso, permite o aperfeiçoamento do serviço baseando-se principalmente na melhoria da oferta de informações aos clientes.
Desde a sua criação, a logística foca-se na eficiência do fluxo de bens ao longo dos canais de distribuição. O fluxo de informação era, muitas vezes, menosprezado, porque nem sempre foi visto como de vital importância para o cliente. Para além disso, a velocidade das trocas de informação era limitada à velocidade de circulação do papel.
A informação exacta e atempada, é vista como sendo de importância crítica para o projecto de sistemas logísticos por três razões (Bowersox et al., 1996, p. 186):
- os clientes têm necessidade de observar informações sobre o estado da encomenda, disponibilidade do produto, tempo de entrega e facturação, sendo como tal, estes elementos necessários de um conglomerado total do serviço prestado;
- com o objectivo de se reduzir os stocks ao longo da cadeia de abastecimento, os gestores aperceberam-se que a informação pode ser eficiente na redução dos mesmos e das necessidades de mão-de-obra;
- a informação aumenta a flexibilidade em relação ao como, quando e onde devem os recursos ser aplicados para ganhar vantagem estratégica.
Um exemplo de posicionamento estratégico baseado em tecnologia de informação é o caso de empresas de entrega expressa. A Fedex foi a primeira a oferecer serviço de entrega para o dia seguinte em 1973 nos Estados Unidos. No final dos anos 80,com elevados investimentos em TI, ela passou a ter o controle de todo o ciclo do pedido do cliente. Com isso podia manter total rastreabilidade do pedido. Atualmente seu sistema processa 63 milhões de transações por dia, o que equivale a 3 milhões de pacotes entregues. A UPS, maior empresa americana deste segmento, investiu US$ 1.5 bilhão entre os anos de 1986 e 1991 para atingir o mesmo patamar de sua concorrente com relação aos serviços prestados.
Outro exemplo de como a informação tem grande importância na logística é a interação entre fabricantes e varejistas no gerenciamento da cadeia de suprimentos, promovida no Brasil pelo Movimento ECR Brasil. Com tal prática, algumas redes varejistas começam a disponibilizar informações do ponto de venda para seus fornecedores de modo que estes sejam responsáveis pelo ressuprimento automático dos produtos. Isto reduz consideravelmente o custo com estoque dos varejistas e possibilita aos fabricantes ter melhor previsibilidade da demanda, propiciando uma utilização de recursos mais racionalizada.
Funcionalidade da informação
Como dito anteriormente, os sistemas logísticos constituem processos integrados constituidos por 4 níveis de funcionalidade: Transação, controlo de gestão, analise de decisão e planeamento estratégico, podendo ser por vezes representados graficamente em forma de pirâmide. O nível mais básico, a transação, inicia e registra atividades logísticas individuais, tais como entrada de encomendas, seleção de encomendas, envio de encomendas, preços, faturação e inquéritos de clientes. O segundo nível, controlo de gestão, foca-se nos relatórios e medições de índices de desempenho. Estes índices de desempenho são necessários para poder fornecer à gestão um feedback sobre os níveis de serviço e utilização de recursos. O terceiro nível, análise de decisão, foca-se na decisão de aplicações para assistir os gestores a identificar, avaliar e comparar estratégias logísticas e alternativas táticas. O quarto e o último nível, planeamento estratégico, tem como objetivo o suporte de informação ao desenvolvimento e melhoramento de estratégias logísticas (Bowersox et al., 1996, p. 187-188).
Sistema Transacional
É a base para as operações logísticas e fonte para atividades de planejamento e coordenação. Através de um sistema transacional, informações logísticas são compartilhadas com outras áreas da empresa, tais como: marketing, finanças, entre outras.
Um sistema transacional é caracterizado por regras formalizadas, comunicações interfuncionais, grande volume de transações e um foco operacional nas atividades cotidianas. A combinação de processos estruturados e grande volume de transações aumenta a ênfase na eficiência do sistema de informações.
A partir dele, ocorre o principal processo transacional logístico: o ciclo do pedido. Com isso, todas as atividades e eventos pertencentes a este ciclo devem ser processados: entrada de pedidos, checagem de crédito, alocação de estoque, emissão de notas, expedição, transporte e chegada do produto ao cliente. Informações sobre tais atividades/eventos, devem estar prontamente disponíveis, visto que o status do pedido é uma questão cada vez mais necessária para um bom serviço ao cliente.
A falta de integração entre operações logísticas é um problema comumente encontrado em sistemas transacionais que não estão sob um sistema de gestão integrada. Isto pode ocorrer basicamente em três instâncias:
- Entre atividades logísticas executadas dentro da empresa;
- Entre instalações da empresa;
- Entre a empresa e outras pertencentes à cadeia de suprimentos ou prestadores de serviços logísticos.
Controle Gerencial
Este nível permite com que se utilize as informações disponíveis no sistema transacional para o gerenciamento das atividades logísticas. A mensuração de desempenho inclui indicadores: financeiros, de produtividade, de qualidade e de serviço ao cliente.
De maneira geral, existe grande carência de indicadores / relatórios de desempenho nas empresas brasileiras. Entre os principais fatores estão a ausência de um sistema transacional que possua todas as informações relevantes e de visão sobre as vantagens de controlar as operações logísticas.
- Um exemplo disso, é a mensuração da disponibilidade de produtos, ou seja, indicadores que apontem o percentual de pedidos que foram entregues completos;
- Outro indicador bastante importante para avaliar o nível de serviço prestado ao cliente é o lead time. Nem sempre as empresas possuem informações sobre a data de chegada ao cliente. No entanto, existem casos nos quais as empresas conseguem obter tal informação, mas não a utilizam de forma sistemática para avaliar o seu desempenho e de seu transportador (transit time).
A presença de relatórios que tratam exceções são fundamentais para um bom gerenciamento, visto que as operações logísticas se caracterizam pelo intenso fluxo de informações. Por exemplo, um sistema de controle proativo deve ter capacidade de prever futuras faltas no estoque com base nas previs ões de demanda e recebimentos previstos.
Um conceito cada vez mais utilizado nas empresas é o de Data Warehouse (DW). Como o nome sugere, armazena dados históricos e atuais de várias áreas da empresa em um único banco de dados com o objetivo de facilitar a elaboração de relatórios. O processo de desenvolvimento de um DW fornece uma oportunidade para a empresa rever e formalizar objetivos,planos e estratégia.
Apoio à Decisão
Esta funcionalidade caracteriza-se pelo uso de softwares para apoiar atividades operacionais, táticas e estratégicas que possuem elevado nível de complexidade. Sem o uso de tais ferramentas, muitas decisões são tomadas baseadas apenas no feeling, o que em muitos casos aponta para um resultado distante do ótimo. Entretanto, se elas forem usadas, existe significativa melhoria na eficiência das operações logísticas, possibilitando, além do incremento do nível de serviço, reduções de custos que justificam os investimentos realizados.
Existem diferenças entre as aplicações de ferramentas de apoio à decisão. Algumas são operacionais, pois estão voltadas para operações mais rotineiras, tais como: programação e roteamento de veículos, gestão de estoque, etc. Por outro lado,existem ferramentas que atuam mais tática e estrategicamente, tais como: localização de instalações, análise da rentabilidade de clientes e etc. A aplicação destas ferramentas vai depender principalmente da complexidade existente nas atividades logísticas e de seu custo/benefício.
Ferramentas que tendem a ser mais operacionais, devem estar inteiramente conectadas com o sistema transacional, de modo que os inputs sejam informações atualizadas e no formato adequado. Em geral, as empresas que não possuem um sistema integrado enfrentam problemas na implementação destas ferramentas no que diz respeito à conectividade com o sistema utilizado. Em ambos os tipos de ferramentas de apoio à decisão, exige-se que o nível de expertise dos usuários seja elevado para lidar com as dificuldades na implementação e utilização. Caso contrário, existe necessidade de treinamento específico, o que ocorre na maioria dos casos.
Planejamento Estratégico
No planejamento estratégico as informações logísticas são apoio para o desenvolver e aperfeiçoar a estratégia logística. Com frequência, as decisões tomadas s ão extensões do nível de apoio à decisão, embora sejam mais abstratas, menos estruturadas e com foco no longo prazo. Como exemplo, podemos citar as decisões baseadas em resultados de modelos de localização de instalações e na análise da receptividade dos clientes à melhoria de um serviço.
Princípios
Os sistemas de informação logística têm que incorporar seis princípios/características de modo a serem capazes de cumprir as necessidades de informação dos gestores e suportar adequadamente o planeamento e operação da empresa (Bowersox et al., 1996, p. 190-192):
Disponibilidade
Primeiro que tudo, a informação logística tem que estar disponível de uma forma consistente. A rapidez de disponibilidade é necessária para conseguir responder às necessidades dos clientes e à gestão de decisões. Esta rapidez é critica pois, os clientes necessitam frequentemente de aceder ao nível de stock e ao estado das encomendas.
A descentralização das operações logísticas exige que a informação esteja disponível e possa ser atualizada em qualquer lugar num país, ou mesmo no mundo. Desta forma, a disponibilidade da informação pode contribuir para a redução da incerteza dos tempos de planeamento e operação .
Rigor
A informação logística deve ser rigorosa de modo a poder refletir tanto o estado atual como o periódico das actividades de forma a refletir tanto as encomendas dos clientes como o nível dos stocks. O rigor é definido como a relação entre a informação registrada pelo sistema de informação logística e os níveis ou estados físicos atuais.
Oportuno
Existem momento certos em que a informação é necessária, e como tal a informação logística tem que ser disposta oportunamente de modo a fornecer um feedback útil à rápida gestão. Considera-se como momento oportuno, o atraso entre a ocorrência da atividade e a disponibilidade da informação no sistema logístico.
Exceção
Estes sistemas de informação tem que ser baseados em exceções de modo a conseguirem enfatizar problemas e oportunidades. As operações logísticas incluem frequentemente um largo número de clientes, produtos, fornecedores e fornecedores de serviços.
Flexibilidade
Têm de ser flexíveis de modo a conterem capacidade para cumprir as necessidades tanto dos utilizadores do sistema como dos clientes. Os sistemas de informação logística têm que ser capazes de fornecer informação à medida das necessidades de clientes específicos.
Formato apropriado
Estes sistemas têm que ter o formato apropriado, pois têm que fornecer relatórios logísticos com uma disposição que seja perceptível, contendo a informação, estrutura e sequência correcta.
Algumas ferramentas de TI utilizadas na Logistica
Sistemas de Informações Logísticas
Atualmente observa-se, uma significativa inclinação do desenvolvimento de sistemas integrados de gestão para aplicação na cadeia de suprimentos, visto que todos os processos de negócios internos já foram integrados, restando apenas obter vantagem competitiva da integração da cadeia de suprimentos (fornecedores, compradores, etc).
Com isso, passa a ser possível a integração com as demais unidades de um grupo empresarial por meio de EDI, com compartilhamento (parcial) da base de dados. Para tal os maiores desafios encontrados são: sistemas geograficamente distantes e distintos, com hardwares diversos, necessidade intensiva de sistemas de telecomunicações, bases de dados diversas, operando em estruturas organizacionais e culturas empresariais diversas.
A seguir comentaremos sobre algumas ferramentas integradas de gestão aplicadas a cadeia de suprimentos.
WMS (Warehouse Management System)
O Sistema de Gerenciamento de Armazéns, chamado de WMS, é uma tecnologia utilizada em armazéns onde ele integra e processa as informações de localização de material, controle e utilização da capacidade produtiva de mão-de-obra, além de emitir relatórios para os mais diversos tipos de acompanhamento e gerenciamento.
O sitema prioriza uma determinada tarefa em função da disponibilidade de um funcionário informando a sua localização no armazém. Com este recurso ocorre um aumento na produtividade quando diferentes tipos de tarefas são intercaladas.
Este sistema tem capacidade de controlar o dispositivo de movimentação de material feito por Veículos Guiados Automaticamente (AGVs) e fazer interface com um Sistema de Controle Automatizado do Armazém (WACS) que tem a função de controlar equipamentos automatizados como as esteiras e os sistemas de separação por luzes e carrosséis.
Com uma ferramenta desse porte a empresa passa a ter um ganho na produtividade com a economia de tempo nas operações de embarque e desembarque, transporte e estocagem de mercadoria e ainda controlar o estoque de produtos no seu armazém. Podendo ainda permitir que o gerente de logística controle as operações de armazém apenas de longe observando apenas se o funcionamento do sistema está adequado às operações logísticas.
Em paralelo ao WMS existe o WCS que é um Sistema de Controle de Armazém e não um gerenciador se diferenciando assim do WMS em alguns aspectos. O WCS não oferece uma variedade de relatórios para auxiliar no gerenciamento das atividades; não tem flexibilidade de hardware; a customização é limitada a mudança de campos e nomes, e a instalação deste sistema não pode ser feita de forma modular, somente integral. A contrapartida de todos esses aspectos negativos é que ele oferece um ótimo acompanhamento e controle das atividades (se limitando a controle) e existe um custo reduzido de software e hardware requerido para a implementação dessa solução.
RFID – Radio Frequency Identification
Identififcação via Radio Freqüência é, relativamente, uma das mais novas tecnologias de coleta automática de dados. Inicialmente surgiu como solução para sistemas de rastreamento e controle de acesso na década de 80. Uma das maiores vantagens dos sistemas baseados em RFID é o fato de permitir a codificação em ambientes não favoráveis e em produtos onde o uso de código de barras, por exemplo, não é eficiente.
Este sistema funciona com uma antena, um transmissor e um decodificador. Esses componentes interagem através de ondas eletromagnéticas transformando-as em informações capazes de ser processadas por um computador
A principal vantagem do uso de sistemas RFID é realizar a leitura sem o contato como no código de barras. Você poderia, por exemplo, colocar o transmissor dentro de um produto e realizar a leitura sem ter que desempacota-lo, ou por exemplo aplica-lo em uma superfície que será posteriormente coberta de tinta ou graxa.
Esse sistema pode ser usado para controle de acesso, controle de tráfego de veículos, controle de bagagens em aeroportos, controle de containers e ainda em identificação de pallets. O tempo de resposta é baixíssimo, tornando-se uma boa solução para processo produtivos onde se deseja capturar as informações com o transmissor em movimento.
Rastreamento de Frotas com Tecnologia GPS – Global Positioning System
Rastreamento é o processo de monitorar um objeto enquanto ele se move. Hoje em dia é possível monitorar a posição ou movimento de qualquer objeto, utilizando-se de equipamentos de GPS aliados a links de comunicação. O casamento GPS + comunicação é necessário pois o receptor GPS localiza sua própria posição; esta deve ser transmitida via canal de comunicação para uma central que fará efetivamente o monitoramento. Esta tecnologia é comumente conhecida como AVL (Automatic Vehicle Location).
GPS é um sistema de posicionamento mundial formado por uma constelação de 24 satélites que apontam a localização de qualquer corpo sobre a superfície terrestre. Um aparelho receptor GPS recebe sinais desses satélites determinando sua posição exata na Terra, com precisão que pode chegar à casa dos centímetros.
A tecnologia GPS é bem conhecida hoje, e comercialmente viável, tendo inclusive fornecedores de equipamentos consolidados e preços formados. As variáveis que efetivamente determinam o custo e o modo de operação do rastreamento de veículos são canal de comunicação entre o veículo e a central de monitoramento e o pacote de serviços oferecidos por esta central.
A ligação feita entre a central de comunicação e o ponto rastreado pode ser feita via telefonia celular que tem seus aparelhos baratos para a solução que oferece, e tem restrições como qualquer outra solução que é estar acessível apenas onde tem cobertura de telefonia celular e o custo da comunicação ainda é alto.
Outra opção é a comunicação via rádio. Esta modalidade é muito simples de implantar, tem um custo de implantação baixo, onde não há custo de comunicação, tendo que fazer a regulamentação com a ANATEL (no Brasil).
Com a possibilidade de rastrear veículos a empresa pode saber onde se encontra o veículo que está fazendo determinada entrega e fazendo um link com o sistema via web a empresa pode colocar a disposição do cliente a localização da entrega.
Código de Barras
O sistema surgiu da idéia de se criar um mecanismo de entrada de dados mais rápida e eficiente, vendo que com o passar do tempo mais microcomputadores estavam sendo fabricados com um grande potencial em armazenamento e processamento de dados.
A leitura de código de barras exige que sejam utilizados alguns aparelhos específicos e que são adotados conforme a necessidade da empresa. Alguns desses aparelhos são os leitores (caneta ótica, slot reader, leitor CCD, pistola laser, scanner omnidirecional e o leitor automático de documentos), os decodificadores (decodificador para teclado, decodificador para interface serial e decodificador para joystick) e impressoras especiais (software para impressão e impressoras profissionais). As impressoras matriciais não têm funcionalidade para esse fim. As impressoras jato de tinta e laser não estão adaptadas para comportar rolos de etiquetas e papel contínuo. Por isso é que foram desenvolvidas impressoras profissionais para impressão de código de barras.
Existe uma padronização mundial para a leitura de código de barras. Para cada produto ou objetivo da identificação existe um tipo de código. Por exemplo:
O EAN – 13, EAN – 8 e UPC são utilizados na unidade de consumo, ou seja, na embalagem do produto que o consumidor final esta comprando. Exemplo: 1 litro de leite em caixa; O EAN/DUN – 14 (SCC - 14) / UCC/EAN 128 são utilizados nas caixas que embalam as várias unidades desses produtos unitários. Exemplo: um engradado contendo 12 litros de leite em caixa;
O UCC/EAN - 128 são usados nos pallets dentro dos galpões de supermercados ou distribuidores. Estes levam no código de barras Identificadores de Aplicação (AI).
O código de barras, comprovadamente, tem uma margem de erro menor que a coleta de dados feita manualmente, sendo assim a maneira mais eficaz de coletar dados em termos velocidade da informação, facilidade de migração para o sistema de controle de estoque e facilidade da adoção da prática do VMI (citado na seção 3.10).
EDI (Electronic Data Interchange)
O EDI, ou Intercâmbio Eletrônico de Dados é um sistema que auxilia diretamente, principalmente, a rotina dos vendedores agilizando o processo de comunicação com a empresa na transmissão de dados. Todas as informações que um vendedor precisa coletar e transferir para a empresa em um segundo momento, ele faz de forma on line evitando assim a demora no in put do pedido e ele ainda tem a possibilidade de consultar o estoque da empresa e informar ao cliente a possibilidade de disponibilizar a mercadoria.
Com a implantação desse sistema com sucesso podemos detectar imensuráveis benefícios trazidos por ele à sua empresa. Consegue-se com ele reduzir custos administrativos, reduzir o estoque (considerando que estoque parado é capital improdutivo, então temos ainda uma economia significativa para investimentos dependendo da área comercial da empresa), reduzir custos e desgastes com o cliente com os itens faltantes, pois se a tecnologia permite transmissão de dados on-line temos a informação acurada e instantânea da posição de estoque. Outros benefícios é que o sistema ainda faz com que o índice de divergências na entrega e no recebimento de mercadorias seja próximo de zero, e permite o melhor gerenciamento de rotas de transporte.
Toda essa tecnologia a disposição do profissional de vendas faz com que ele se sinta mais valorizado e aumente sua produtividade se dedicando a área fim da empresa – as vendas. E tão importante quanto aumentar as vendas para a empresa é o fato de que, tanto pela tecnologia de software e hardware envolvida quanto pelo corpo funcional há um ganho no valor agregado da empresa.
VMI – Vendor Managed Inventory
O VMI ou Estoque Administrado pelo Fornecedor, é uma ferramenta muito importante principalmente para a cadeia de suprimentos que pretende ou já trabalha com o JIT (Just-in -Time). O principal objetivo desta técnica é fazer com que o seu fornecedor, através de um sistema de EDI, verifique a sua real necessidade de produto, no momento certo e na quantidade certa. Este recurso tem uma maior funcionalidade para as empresas que um grande número de fornecedores e possui um amplo mix de produtos. A integração permite que se faça, de acordo com o forecast uma mudança de planejamento de reabastecimento, pois a informação chega ao seu fornecedor em tempo real. O nível de detalhamento é tanto que, detectada a demanda de produto acabado, o software se encarrega de traçar planos para a produção, planejamento de abastecimento e distribuição para os depósitos.
ECR (Efficient Consumer Response)
O ECR, Resposta Eficiente ao Cliente, não é um sistema e nem é uma técnica, é um conjunto de práticas desenvolvidas em conjunto com fabricantes, distribuidores e varejistas com o objetivo de obter ganhos por eficiência nas atividades comerciais e operacionais entre as empresas prestando assim um serviço de qualidade ao consumidor final.
As grandes redes de varejistas como Wall Mart, por exemplo, tem centenas de fornecedores, outra infinidade de produtos diferentes e precisa de uma cadeia de suprimentos totalmente integrada para poder oferecer aos seus clientes o produto na prateleira. Para isso acontecer é necessário que a rede adote algumas práticas de reengenharia de processos e Benchmarking ,inclusive utilizado-se da tecnologia de informação. Sendo as mesmas, premissas para começar a pensar em integração e gerenciamento da cadeia de suprimentos.
Os requisitos para se por em prática a filosofia do ECR e fazer os check outs nas saídas das mercadorias das lojas (PVs) e ter o controle do estoque no fornecedor. Como o volume de produtos é muito grande, tanto o fornecedor quanto o varejista, precisa utilizar uma coleta de informação que seja acurada e rápida tendo a sua disposição o código de barras. E o controle do estoque do ponto de venda feita pelo fornecedor é usada a ferramenta de VMI co transmissão de dados via EDI, onde temos precisão e rapidez na operação.
A cadeia produtiva ideal passa por alguns sistemas de informação em uma ordem lógica:
==
Referências
Ligações externas
- Em português
- Sociedade Brasileira de Computação - SBC
- Associação Portuguesa de Sistemas de Informação - APSI
- Periódico Científico Ciência da Informação
- Curso de Sistemas de Informação
- Comissão de Processo Seletivo / UFLA da Universidade Federal de Lavras
- Em inglês
- Association for Information Systems - AIS
- Association for Computing Machinery - ACM
- European Research Center for Information Systems - ERCIS
- Departamento de Sistemas de Informação da London School of Economics - LSE
Sistemas de informação/Custo logístico
Etapas de desenvolvimento - 9 fases | ||||||||
---|---|---|---|---|---|---|---|---|
Início: ![]() |
Básico: ![]() |
Criação: ![]() |
Desenvolvimento: ![]() |
Maturação: ![]() |
Revisão: ![]() |
Desenvolvido: ![]() |
Finalização: ![]() |
Abrangente: ![]() |
Custo logístico é qualquer custo relacionado com a logística de uma empresa, entre os quais se podem destacar os custos de armazenagem, das existências (stock), das rupturas de stock, de processamento de encomendas e de transporte. Os custos logísticos são, geralmente, os segundos mais importantes, só ultrapassados pelos custos da própria mercadoria. Por isso, saber gerir esses custos pode ser crucial para a sobrevivência da empresa (Ricarte, 2002). A gestão destes custos é feita através do planeamento de custo ou do pré-cálculo de custo pois estes permitem determinar os padrões de custo de produção ou produto/mercadoria (Chiavenato, 1991, p. 130). O gestor logístico é responsável pela localização geográfica das matérias-primas, dos produtos em processamento e dos produtos acabados onde estes são pretendidos, ao menor custo possível (Bowersox et al., 1996, p. 4).
O principal objectivo da logística é atingir um determinado nível de serviço de cliente ao menor custo total possível. A logística envolve trabalho detalhado e complexo. Os gestores logísticos são responsáveis pelo planeamento e administração deste trabalho. A logística procura criar valor para o cliente ao menor custo total. A Logística existe para satisfazer as necessidades do cliente, facilitando as operações de produção e marketing. A nível estratégico, os gestores logísticos procuram atingir o nível de qualidade de serviço ao cliente, previamente acordado, através da mais avançada competência operacional. O desafio é equilibrar o nível de serviço esperado e os custos de forma a atingir os objectivos do negócio. A missão do sistema logístico é medido em termos do custo total e do seu nível de serviço. A medição do nível de serviço está relacionada com a disponibilidade de existências, capacidade operacional e qualidade de esforço. Os custos logísticos estão directamente relacionados com o nível de serviço pretendido. De uma forma geral, quanto melhor o nível de serviço pretendido, mais elevado o custo logístico total. A chave para um desempenho logístico eficiente é desenvolver um esforço equilibrado entre o nível de serviço e o custo total dispendido (Bowersox et al., 1996, p. 6, 8-9 e 20).
Segundo Bowersox et al. (1996, p. 5), para uma empresa, os custos logísticos representam, geralmente, 5 a 35% das vendas, dependendo do tipo de negócio, da localização e do rácio peso/valor dos produtos e materiais. A logística representa um dos maiores componentes de custo de uma empresa, sendo apenas excedida pelo custo dos materiais na produção ou das mercadorias vendidas no comércio por grosso ou a retalho. Embora seja dispendiosa, a logística é vital para o sucesso de um negócio.
O custo logístico e a economia
Impacto do desenvolvimento de novas tecnologias no custo logístico
O número de armazéns do sistema logístico
Factores que afectam o custo logístico
Análise do custo logístico total
Outros custos relacionados com a logística
Modelos de optimização do custo logístico
Sistemas de informação/Custo logístico/Introdução
Logística/Sistemas de informação/Custo logístico/Introdução
Sistemas de informação/Custo logístico/O custo logístico e a economia
De acordo com Coyle et al. (2003, p. 34-35), numa escala macro, o custo logístico absoluto, de um modo geral, aumenta com o crescimento da economia. Se o número de bens e serviços produzidos e consumidos aumentar, verifica-se um aumento do custo total relacionado com as actividades logísticas. A eficiência de um sistema logístico pode determinar-se através da relação do custo logístico total com o Produto Interno Bruto (PIB). Ao exprimir o custo logístico como percentagem do PIB, uma redução na percentagem traduz um aumento na eficiência do sistema logístico. Esta redução no custo logístico relativo permite uma maior competitividade das empresas, já que tem um impacto directo no custo da produção de bens.
Sistemas de informação/Custo logístico/Impacto do desenvolvimento de novas tecnologias no custo logístico
O desenvolvimento de novas tecnologias influencia o sector da logística. No início dos anos 90, o desenvolvimento de microprocessadores revolucionou a logística. Os processadores de dados de baixo custo foram particularmente significativos para as operações logísticas. Mais tarde, através da combinação de software avançado com hardware a baixo custo, o gestor logístico passou a ter um auxiliar de grande poder para efectuar as transacções, controlar o desempenho e apoio às decisões. Os recursos informáticos possibilitaram um nível de desempenho logístico nunca antes alcançado. Permitiram a gestão da logística como um processo integrado, desde o momento da procura, por parte do cliente, até à distribuição do produto acabado.
O desenvolvimento de microprocessadores foi acompanhado por um desenvolvimento de tecnologias de informação, tal como o EDI e o fax. Esta melhoria na troca de informação originou novas estratégias para atingir um melhor desempenho logístico (JIT, QR e CR, entre outros) e permitiu uma redução do custo logístico (Bowersox et al., 1996, p. 15-16).
Sistemas de informação/Custo logístico/O número de armazéns do sistema logístico
De acordo com Coyle et al. (2003, p. 297), decidir qual o número de armazéns que um sistema logístico deve possuir é uma das tarefas mais importantes do gestor logístico. Esta decisão deve, de um modo geral, basear-se na compensação entre custos.
Verificou-se, então, que o aumento do número de armazéns num sistema logístico afecta o custo de distribuição. O aumento do número de armazéns provoca, por um lado, uma diminuição do custo de transporte e do custo de vendas perdidas, e, por outro lado, um aumento do custo das existências e do armazenamento. Agrupando as mercadorias a receber por cada armazém de modo a corresponderem a um vagão ou camião completo, as tarifas de transporte são mais baixas, diminuindo o custo de transporte. Por outro lado, o aumento do número de armazéns aproxima os armazéns do cliente e da área de mercado, reduzindo tanto a distância como o custo de transporte. O custo de armazenamento aumenta pois o espaço total aumenta sempre com um maior número de armazéns.
Sistemas de informação/Custo logístico/Factores que afectam o custo logístico
Etapas de desenvolvimento - 9 fases | ||||||||
---|---|---|---|---|---|---|---|---|
Início: ![]() |
Básico: ![]() |
Criação: ![]() |
Desenvolvimento: ![]() |
Maturação: ![]() |
Revisão: ![]() |
Desenvolvido: ![]() |
Finalização: ![]() |
Abrangente: ![]() |
Os autores Coyle et al. (2003, p. 63-69) consideram que os custos logísticos são afectados por factores relacionados com a competitividade, o produto e as localizações, para melhor explicar o papel estratégico da logística numa empresa.
Sistemas de informação/Custo logístico/Factores que afectam o custo logístico/Competitividade
A competitividade é frequentemente interpretada como concorrência entre preços de venda. Apesar de este ser um factor a ter em conta, em diversos mercados, o nível de serviço é uma importante forma de competitividade. Por exemplo, se uma empresa pode garantir ao cliente a entrega dos produtos num período de tempo mais curto, então o cliente pode minimizar o seu custo de existências. Através da melhoria do nível de serviço, a empresa aumentou a sua competitividade (Coyle et al., 2003, p. 63-65).
- 1. Período de aprovisionamento
Considerado como o intervalo de tempo que decorre desde que o cliente decide fazer uma encomenda até ao momento da sua recepção, o período de aprovisionamento afecta o nível das existências. Quanto menor o período de aprovisionamento, menor o nível de existências necessário e menor o custo. Uma empresa pode melhorar o nível de serviço através da redução do período de aprovisionamento do cliente.
- 2. Substituibilidade
A substituibilidade afecta a importância do nível de serviço: quanto maior for a substituibilidade, maior deve ser o nível de serviço correspondente. Caso ocorra ruptura de stock de um produto similiar a outros produtos existentes no mercado, o cliente pode optar por um dos produtos concorrentes em vez de esperar o reabastecimento do produto que pretendia. Por outro lado, uma empresa pode reduzir o custo de ruptura de stock aumentando o nível das existências ou investindo no transporte.
- 3. Efeito das existências
Ao aumentar o custo das existências (seja por aumentar o nível médio de stock ou por aumentar o número de encomendas), as empresas conseguem reduzir o custo de ruptura de stock. Isto é, existe uma relação inversa entre o custo de ruptura de stock e o custo das existências. É, no entanto, frequente as empresas estarem dispostas a aumentar o custo das existências apenas enquanto este aumento provocar uma redução maior no custo de ruptura de stock, isto é, até ao ponto em que o benefício marginal e o custo marginal se igualam.
- 4. Efeito do transporte
Um aumento do custo de transporte reflecte-se numa diminuição do custo de ruptura de stock. O aumento do custo de transporte pode fazer-se através da aquisição de um serviço de transporte de qualidade superior, por exemplo, passar de um meio de transporte marítimo para um meio de transporte ferroviário, de um meio de transporte ferroviário para um meio de transporte rodoviário ou mesmo do rodoviário para o aéreo. Um custo de transporte mais elevado pode ser ainda originado por viagens mais frequentes, transportando menores quantidades a taxas mais elevadas. Mais uma vez, as empresas estão geralmente dispostas a fazê-lo até ao ponto de igualdade entre o custo marginal de aumento do custo de transporte e o benefício marginal da diminuição do custo de ruptura de stock.
É de notar que, embora o efeito das existências e o efeito do transporte tenham sido analisados separadamente, é comum as empresas conjugarem o aumento do custo das existências e o aumento do custo de transporte, de forma a reduzir o custo de ruptura de stock. Além disso, um aumento no custo de transporte poderá levar a uma redução do custo das existências devido à posse de menores quantidades e períodos de posse mais curtos. Estes factores de competitividade interagem entre si, razão pela qual devem ser geridos como um todo e não como factores isolados.
Sistemas de informação/Custo logístico/Factores que afectam o custo logístico/Produto
Um número considerável de factores relacionados com o produto afecta o custo logístico e a importância da logística. Entre os mais importantes, tem-se: o valor, a densidade, a fragilidade e, ainda, a necessidade de cuidados especiais de movimentação (Coyle et al., 2003, p. 66-68).
- 1. Valor
O valor do produto, normalmente, afecta os custos logísticos, nomeadamente, os custos de armazenagem, os custos das existências, de transporte, embalagem e até de movimentação.
As tarifas de transporte reflectem o risco associado à movimentação dos produtos. Há, muitas vezes, uma maior probabilidade de danificação no caso de produtos de maior valor. Os custos de reembolso, por parte da empresa de transporte, caso esses produtos se danifiquem, são mais elevados. As empresas de transporte tendem a cobrar taxas mais elevadas para produtos de maior valor, já que os seus clientes têm geralmente capacidade de as pagar. Assim, quanto maior o valor do produto, maior o custo de transporte.
O custo de armazenagem e os custos das existências também aumentam com o valor do produto. Produtos de maior valor implicam maior capital investido nas existências, com custos de capital total mais elevados. Além disso, o risco associado à armazenagem de produtos de maior valor aumenta o possível custo de obsolescência e amortização. Por último, os custos de armazenagem aumentam com o valor do produto, uma vez que quanto maior o valor, mais complexos são os requisitos de armazenamento.
É de notar que o custo de embalar o produto é também superior, no caso de produtos com valor mais elevado, dado que a empresa tem de recorrer a materiais mais resistentes e protectores. Os equipamentos de movimentação desses produtos são também, frequentemente, mais sofisticados. As empresas, geralmente, estão dispostas a investir nesses equipamentos, de forma a minimizar o tempo de movimentação e diminuir a probabilidade de danificação do produto.
- 2. Densidade
Outro factor que afecta os custos logísticos é a densidade do produto, isto é, o quociente peso/volume. Um produto que tenha um peso baixo em relação ao volume que ocupa tem uma densidade baixa.
A densidade influencia os custos de transporte e de armazenagem: à medida que a densidade do produto aumenta, os custos de transporte e de armazenagem tendem a diminuir. Ao estabelecer as suas taxas, as empresas de transporte têm em conta o peso total que os seus veículos têm capacidade para transportar, já que exprimem as suas taxas em unidades monetárias por unidade de peso. Desta forma, estas empresas podem atribuir taxas mais baixas quanto se trata de produtos com densidade elevada, já que é possível caber mais peso num veículo. A densidade também afecta os custos de armazenagem. Quanto maior a densidade, menor o custo de armazenagem: com produtos de maior densidade é possível o armazenamento de mais peso por unidade de volume, isto é, verifica-se uma utilização mais eficiente do espaço de armazém disponível.
- 3. Fragilidade
Quanto maior a fragilidade do produto, mais elevados serão os custos de transporte e armazenagem. Produtos mais susceptíveis de serem danificados têm taxas de transporte mais elevadas, porque as empresas de transporte esperam uma maior probabilidade de o produto ser danificado no transporte. Por outro lado, os custos de armazenagem são elevados, seja para cobrirem as situações em há, de facto, uma danificação do produto, seja pela implementação de medidas ou requisitos extra, de forma a evitar que isso aconteça.
- 4. Necessidades especiais de manuseamento
Este factor está relacionado com o anterior, embora seja algo distinto. Alguns produtos podem necessitar de cuidados especiais ao serem manuseados, o que se vai reflectir nos custos logísticos, nomeadamente através do aumento do custo de armazenagem e do custo de transporte. Dentro dos requisitos especiais de manutenção pode-se destacar, por exemplo, veículos especiais de transporte, refrigeração e aquecimento.
Sistemas de informação/Custo logístico/Factores que afectam o custo logístico/Localização
Os factores relacionados com a localização de pontos fixos no sistema logístico, em relação ao mercado e a localização dos fornecedores, são extremamente importantes (Coyle et al., 2003, p. 68-69).
As localizações influenciam os custos logísticos, nomeadamente os custos de armazenagem e de transporte, sendo que estes tendem a aumentar com o aumento da distância entre os pontos do sistema logístico.
- Exemplo:

No exemplo apresentado na Figura 1, a empresa B tem 1,50€ de vantagem no custo de produção (CP), em relação à empresa A. A empresa B produz a 7,00€ por unidade e a empresa A a 8,50€ por unidade. A empresa B, contudo, tem um custo de 1,35€ com o transporte de matéria-prima (0,60€ + 0,75€) e um custo de 3,50€ com o transporte do produto para o mercado M, tendo um custo total unitário de transporte de 4,85€. A empresa A tem um custo de 0,90€ com o transporte de matéria-prima e um custo de 1,15€ com o transporte do produto para o mercado, tendo um custo total unitário de transporte de 2,05€. A vantagem de 2,80€ no custo de transporte da empresa A compensa a desvantagem de 1,50€ no custo de produção. A empresa B poderá desejar procurar estratégias alternativas para o seu sistema logístico, de forma a competir mais eficazmente em M. Por exemplo, a empresa B pode ter o custo unitário de 3,50€ em resultado do transporte como carga fraccionada (transporte de baixo volume do produto para o mercado). A empresa pode considerar a hipótese de utilizar um armazém em M e efectuar o transporte por via férrea de vagões inteiros, a custo de transporte mais baixo.
Sistemas de informação/Custo logístico/Análise do custo logístico total
Em 1956, Lewis, Culliton e Steele apresentam uma monografia acerca da economia do transporte aéreo, na qual defendem uma nova perspectiva do custo logístico. Introduzem uma visão integrada da logística e o conceito de custo total logístico. Segundo aqueles autores, o custo total logístico deve incluir todos custos necessários para responder aos requisitos de um sistema logístico. As empresas devem concentrar-se na redução do custo total logístico, mesmo que isso implique que alguns componentes do custo não tenham o menor valor possível. Segundo Coyle et al. (2003, p. 13), a diminuição do custo total de um sistema pode fazer-se através de uma avaliação de combinações alternativas de meios de transporte, número e dimensão de armazéns, localização de fábricas e armazéns e níveis das existências, entre outros. O conceito de custo total desencadeou o estudo acerca da inter-relação dos custos funcionais. Esta nova visão veio revolucionar a logística, já que, até à data, as empresas procuravam atingir o menor valor possível em cada componente do custo logístico, sem dar grande relevância ao custo total. Os gestores frequentemente procuravam reduzir os custos funcionais, tal como o de transporte, esperando que dessa forma fosse alcançado o menor custo total (Bowersox et al., 1996, p. 10-12 e 643 e Coyle et al., 2003, p. 13).
De um modo geral, o conceito de análise do custo total defende a afectação dos custos com base nas actividades, contestando a prática comum de usar a contabilidade tradicional por esta dificultar a identificação das actividades do sistema logístico que correspondem ao maior custo. A afectação dos custos segundo a contabilidade tradicional agrupa os custos em contas tais como salários, rendas e serviços públicos, não identificando a responsabilidade pelos custos, das diversas operações da empresa. Por seu lado, a afectação dos custos com base nas actividades procura relacionar os custos relevantes com as actividades desenvolvidas de valor acrescentado. O conceito fundamental do agrupamento dos custos com base nas actividades defende que as despesas devem estar associadas à actividade que consome um recurso, em vez de estar associadas a determinada organização ou centro de custos, de forma a que o gestor logístico tenha a informação necessária para determinar se determinado cliente, encomenda, produto ou serviço é rentável. É importante referir que, além da identificação dos custos de cada actividade, devem também ser afectados aos factores que influenciam os respectivos custos, de forma a facilitar a avaliação de alternativas (Bowersox et al., 1996, p. 643 e 645-646).
Os custos referentes a cada actividade podem ser divididos em custos directos, indirectos e despesas gerais. Os custos directos ou operacionais provêm directamente do desempenho logístico; os custos indirectos resultam da repartição dos recursos pelas várias operações logísticas; as despesas gerais estão relacionadas com os gastos com iluminação e aquecimento, por exemplo, indispensáveis para todas as unidades organizacionais. O modo como os diversos custos são classificados influencia toda a análise do sistema, sendo, portanto, de extrema importância. Por último, deve ser identificado o período de tempo durante o qual os custos em análise foram acumulados. Este processo apresenta alguma complexidade, já que muitas operações, desde a encomenda até à distribuição do produto final, são realizadas em antecipação da venda (Bowersox et al., 1996, p. 646-647).
A análise de custo total é muitas vezes focalizada apenas no custo das existências e no custo de transporte. Estes custos podem ser definidos num formato suficientemente geral para abranger as relações entre as actividades e os custos de funcionamento dos componentes logísticos com elas relacionados. Nesta abordagem, o custo total das existências inclui os custos de posse e de encomenda: impostos, armazenagem, capital, seguros, obsolescência e, ainda, controlo das existências, preparação das encomendas e comunicações, entre outros. O custo total de transporte inclui a contratação dos transporte e todos os custos decorrentes dos vários modos de transporte, incluindo os respectivos custos administrativos. Esta abordagem justifica-se pelo facto de estas duas categorias de custos caracterizarem as dimensões temporais e espaciais de uma operação logística e por representarem, geralmente, 80 a 90 por cento dos custos totais de um sistema logístico (Bowersox et al., 1996, p. 649).
Segundo Coyle et al. (2003, p. 60), as abordagens mais elementares de análise de sistemas logísticos baseados no conceito de custo total são a análise a curto prazo ou estática e a análise a longo prazo ou dinâmica. Estes métodos comparam dois ou mais sistemas logísticos alternativos, calculando qual deles tem o menor custo total em determinada situação concreta.
- Análise a curto prazo ou estática
Numa análise a curto prazo é considerada uma situação momentânea e os custos dos vários centros de actividade. A informação referente aos custos é avaliada para cada um dos sistemas alternativos em análise. Em seguida, é seleccionado o sistema que corresponde ao menor custo total, na condição de que este esteja de acordo com as restrições impostas pela empresa ao sistema logístico. Este método analisa os custos associados a um sistema logístico apenas num determinado instante no tempo ou para um determinado nível de produção (Coyle et al., 2003, p. 60).
- Análise a longo prazo ou dinâmica
Numa análise a longo prazo, o sistema óptimo é determinado com base no cálculo matemático do ponto de igualdade entre os sistemas em questão. Os sistemas podem ser representados por uma equação linear do tipo , em que y representa o custo total, a os custos fixos, b os custos variáveis por unidade e x a quantidade de produto. Obtendo a informação relativa aos custos de cada sistema, podem determinar-se as equações e fazer a representação gráfica. Pode, então, determinar-se o ponto de igualdade dos sistemas e verificar qual o sistema com o menor custo total, em função da quantidade de produto. Se não houver intersecções entre as equações dos vários sistemas em análise, a escolha deverá recair sobre o sistema cuja recta, para qualquer quantidade de produto, apresenta sempre menor custo total.
No caso de se considerarem três ou mais sistemas simultaneamente, a dois deles pode corresponder um ponto de intersecção, enquanto que o outro sistema tem sempre um custo total mais elevado. Se ocorrerem intersecções das três rectas correspondentes aos sistemas, verifica-se, geralmente, a existência de dois pontos relevantes de intersecção ou de indiferença. Uma terceira intersecção verificar-se-á para um custo total maior do que alguma outra função dos custos e não será relevante (Coyle et al., 2003, p. 61-63).
- Exemplo
A Tabela 1 ilustra uma análise estática. Neste caso, a empresa utiliza um itinerário ferroviário desde a fábrica e do armazém da fábrica até aos clientes. No armazém da fábrica, são embalados e depois transportados produtos químicos, por via ferroviária, para o cliente. Um outro sistema proposto utilizaria um armazém orientado para o mercado. Os produtos seriam transportados da fábrica até ao armazém próximo do mercado, embalados e enviados para o cliente. Em vez de transportar todos os produtos por via ferroviária, a empresa transportá-los-ia por via marítima até ao armazém, aproveitando as tarifas reduzidas do transporte de carga a granel. Depois de serem embalados, os químicos seriam, então, transportados, por via ferroviária, do armazém até ao cliente.
Custo logístico da fábrica | Sistema 1 | Sistema 2 | |||||
Embalagem | 500 | 0 | |||||
Armazenagem e movimentação | 150 | 50 | |||||
Custo de posse das existências | 50 | 25 | |||||
Administrativos | 75 | 25 | |||||
Custo fixo | 4200 | 2400 | |||||
Custo de transporte | |||||||
Para o armazém perto do mercado | 0 | 150 | |||||
Para o cliente | 800 | 100 | |||||
Custo de armazenagem | |||||||
Embalagem | 0 | 500 | |||||
Armazenagem e movimentação | 0 | 150 | |||||
Custo de posse das existências | 0 | 75 | |||||
Administrativos | 0 | 75 | |||||
Custo fixo | 0 | 2400 | |||||
Custo total | 5775 | 5950 | |||||
Neste exemplo, há um compromisso entre a redução nos custos de transporte e o aumento na armazenagem. Se a análise for estritamente estática (para o nível de produção em questão), o sistema proposto (Sistema 2) é mais dispendioso que o sistema utilizado actualmente (Sistema 1). Assim, a não ser que a análise forneça informação adicional favorável ao sistema proposto, a empresa continuará a utilizar o sistema actual.
Há, contudo, duas razões para seleccionar o sistema proposto. Em primeiro lugar, não é fornecida informação quanto aos requisitos de serviço do cliente. O novo armazém orientado para o mercado pode fornecer um melhor serviço ao cliente e, portanto, aumentar as vendas e o lucro, compensando parte do custo mais elevado do Sistema 2. Em segundo lugar, se for feita uma análise dinâmica ao exemplo (ver Figura 1), pode verificar-se que, embora o Sistema 1 corresponda a um menor custo para um nível de produção de 50 000 unidades, o Sistema 2 passa a ser menos dispendioso por volta das 70 500 unidades. Assim, uma empresa que esteja numa situação de rápido crescimento das vendas pode querer planear, desde já, uma mudança para o Sistema 2. O tempo de preparação do novo armazém pode necessitar que o planeamento se inicie imediatamente.

A análise dinâmica permite, ainda, calcular, matematicamente, o ponto de igualdade dos dois sistemas, em vez de apenas fazer a sua estimativa graficamente. Para tal, começa-se com a equação de uma recta (). Neste caso particular, representa os custos fixos e o custo variável por unidade. A variável será o nível de produção. Se se pretende determinar o ponto de igualdade dos dois sistemas, deve-se inserir a informação relativa aos custos e igualar as duas equações. Como se mostra abaixo, os dois sistemas são iguais quando o nível de produção é de aproximadamente 70 500 unidades, o que corresponde a um ponto de indiferença entre os dois sistemas:
Sistema 1
Custo total = custo fixo + custo variável por unidade x número de unidades
Sistema 2
Ponto de indiferença
Sistemas de informação/Custo logístico/Outros custos relacionados com a logística
- Qualidade
Segundo Courtois et al. (1997, p. 250-251), um produto de qualidade aumenta a competitividade de uma empresa. Um investimento na qualidade pode conduzir à fidelização dos clientes e à diminuição dos custos de produção. Além disso, permite eliminar as despesas suplementares relacionadas com produtos não-conformes, tais como os custos de garantia e do serviço pós-venda. Os problemas de não qualidade podem levar a determinadas ocorrências aleatórias na produção, tais como:
- níveis de existências elevados, para ter a capacidade de substituir um produto defeituoso;
- atrasos nas entregas devido à necessidade de verificação da qualidade num determinado lote;
- desmontagem de produtos acabados, caso seja detectado algum defeito.
Todas as ocorrências acima mencionadas impedem a redução do nível das existências e comprometem a competitividade da empresa. A organização global da empresa deve, assim, ser pensada numa óptica de Qualidade Total (Courtois et al., 1997, p. 271).
De facto, um dos aspectos que mais revolucionou a logística foi a aceitação a nível global do Total Quality Management (TQM). Segundo este conceito, a própria logística deve seguir padrões de qualidade exigentes e procurar, continuamente, atingir zero defeitos. Os custos logísticos uma vez gastos, não podem ser recuperados: se a qualidade falha, o desempenho logístico tem, geralmente, de ser invertido e repetido (Bowersox et al., 1996, p. 42).
- Previsão da procura
De acordo com Courtois et al. (1997, p. 67), o ideal seria uma empresa produzir exactamente os produtos que os seus clientes vão, efectivamente, consumir. Uma empresa, independentemente da sua actividade e tipologia comercial, deve apoiar-se em sistemas de previsão fiáveis, de forma a tomar decisões que levem ao seu bom funcionamento e à sua longevidade.
Compreender o comportamento do consumidor tem um papel importante no funcionamento de uma empresa. A previsão da procura - isto é, do volume ou número de unidades que irão ser produzidas, transportadas ou vendidas - influencia o planeamento e a coordenação de um sistema logístico. Os consumidores têm a oportunidade de comparar preços, qualidade e serviço de várias empresas, exigindo produtos a preços competitivos e com qualidade. De facto, os requisitos logísticos para servir os clientes têm vindo a aumentar, levando algumas empresas a melhorar a sua capacidade de resposta ao cliente, por exemplo, funcionando vinte e quatro horas por dia, sete dias por semana (Bowersox et al., 1996, p. 222 e Coyle et al. 2003, p. 5).
Sistemas de informação/Custo logístico/Modelos de optimização do custo logístico
Existem vários modelos que podem auxiliar o gestor logístico quanto à escolha da configuração da rede logística. Estes modelos são muito abrangentes, podendo ser aplicados a vários problemas: localização de fábricas, centros de distribuição, fluxos de informação e materiais dentro do sistema logístico, entre outros. Estas técnicas procuram facilitar a comparação entre o funcionamento e o valor da relação custo/serviço, da rede logística actual, com redes logísticas alternativas. Dentro destes modelos, encontram-se os modelos de optimização. Os modelos de optimização baseiam-se em procedimentos matemáticos exactos, que garantem uma solução óptima para a formulação matemática do problema. Isto é, pode ser provado, matematicamente, que a solução obtida com o modelo é a solução óptima. Os modelos de optimização têm em conta as restrições do sistema e seleccionam a melhor solução, dentro das alternativas possíveis, recorrendo a técnicas como a programação matemática. Muitos modelos de optimização estão incorporados em programas para computador que podem ser adquiridos pelas empresas. Como exemplo destes modelos, pode indicar-se o modelo da quantidade económica de encomenda (EOQ). Este modelo fornece uma resposta específica para o equilíbrio entre o custo de encomendar e o custo do nível médio das existências, permitindo identificar a frequência de encomendas e o tamanho de lote a encomendar que correspondem ao menor custo total das existências (Bowersox et al., 1996, p. 254 e Coyle et al., 2003, p. 516-517). As vantagens e desvantagens do uso de técnicas de optimização são tratadas nas abordagens deste tema. Ver, por exemplo, Coyle et al. (2003, p. 517 e 519):
- o utilizador tem a garantia de que encontra de facto a melhor solução possível, para as condições e dados considerados;
- os modelos de optimização têm geralmente capacidade para lidar com sistemas com um grau de complexidade elevado;
- a análise efectuada por estes modelos revela-se muito eficiente, já que todas as alternativas são exploradas;
- pode explorar-se quais os efeitos da variação de determinados factores do sistema no custo total, já que o modelo recalcula a solução óptima para cada situação apresentada;
- comparando a utilização de modelos de optimização com modelos heurísticos, verifica-se por vezes uma diferença significativa entre o lucro e os custos num caso e noutro.
Quanto a desvantagens, pode referir-se que na maioria das situações, a aplicação destes modelos requer recursos informáticos. Além disso, o uso da técnica de programação linear é limitado, já que implica que a formulação do problema seja determinística e possível de ser aproximada linearmente. A técnica de programação linear por si só não permite a consideração de custos fixos e custos variáveis de funcionamento logístico de uma instalação.
Sistemas de informação/Processamento de encomendas
O processamento de encomendas representa várias actividades incluídas no ciclo de encomendas do cliente. Dependendo do tipo de encomenda, estas actividades necessitam de um determinado tempo para serem completadas. Mais concretamente, as actividades são (Ballou, 2006, p. 122):
Preparação da encomenda
Transmissão da encomenda
Atendimento da encomenda
Aviamento da encomenda
Relatório da situação da encomenda
Exemplo de processamento de uma encomenda
Sistemas de informação/Processamento de encomendas/Preparação da encomenda
Da preparação da encomenda fazem parte todas as actividades relacionadas com a recolha de informações acerca dos produtos e serviços pretendidos e com a sua requisição formal para que sejam adquiridos. O preenchimento de formulários, a determinação da disponibilidade de existências e a transmissão da encomenda a um encarregado de vendas podem também fazer parte da preparação da encomenda. Com o desenvolvimento da tecnologia, estas actividades passaram a estar muito facilitadas.
Existem várias ferramentas que são uma grande ajuda, tais como: o código de barras, que nos dá a descrição dos produtos pretendidos, incluindo o tamanho e quantidade; os páginas Web dos fornecedores com informação acerca dos seus produtos ou até a possibilidade de fazer as encomendas online; ou os computadores das empresas, que através da troca electrónica de dados, geram encomendas directamente, evitando as faltas de existências.
Estas tecnologias vão, aos poucos, eliminando várias tarefas, que anteriormente tinham de ser feitas manualmente, tornando o tempo de preparação da encomenda mais curto e reduzindo, assim, o tempo de ciclo da encomenda do cliente (Ballou, 2006, p. 122-123).
Sistemas de informação/Processamento de encomendas/Transmissão da encomenda
Quando a encomenda já foi efectuada, a primeira actividade a efectuar no ciclo de processamento é a transmissão de informações. Esta actividade passa por transmitir os documentos do ponto de origem da encomenda para o fornecedor. Esta transmissão pode ser realizada manualmente, por serviço postal ou entregue por funcionários; ou electronicamente, por telefone para números gratuitos, por fax, comunicações via satélite, Electronic Data Interchange (EDI) e através da Internet.
O tempo para a transmissão de informações varia conforme o método utilizado, sendo a transmissão via postal o método mais lento e o transmissão electrónica o método mais rápido. As características de desempenho que têm de ser pesadas para a escolha do método a utilizar são a rapidez, a confiabilidade e a precisão, que devem ser comparadas com o seu preço e custo de operação. A relação entre o desempenho e as receitas são ainda o maior desafio.
Uma grande dúvida é qual é o melhor método a utilizar entre a EDI e a Internet. Se, por um lado, a EDI é o método mais seguro, pois não há risco de fuga de informações, é muito mais dispendioso do que a Internet. Apesar de haver uma grande quantidade de empresas a utilizar o EDI, o aperfeiçoamento e aumento da segurança da Internet tem como consequência a troca de informações via EDI e Internet deixarem de ser diferenciáveis (Ballou, 2006, p. 123).
Sistemas de informação/Processamento de encomendas/Atendimento da encomenda
Antes de se poder aviar uma encomenda, há várias tarefas que têm de ser realizadas: verificar a exactidão das informações na encomenda, tais como, a descrição, quantidade e preço dos artigos; conferir se há disponibilidade dos itens encomendados em armazém; tratar dos documentos correspondentes a encomendas pendentes ou canceladas, conforme o caso; verificar a situação de crédito do cliente; transcrever as informações da encomenda de acordo com o necessário; e facturar a encomenda. Estas tarefas são indispensáveis e podem ainda surgir outras tarefas de preparação adicionais, antes da encomenda estar em condições de ser aviada. Já existem sistemas automatizados para realizar estas tarefas.
Os avanços tecnológicos assumem grande importância no atendimento das encomendas. Os códigos de barras, leitores ópticos e computadores trouxeram enormes benefícios para estas actividades. Estima-se que estas tecnologias permitiram reduzir, substancialmente, o total de gastos das empresas, nas suas cadeias logísticas. O sector da saúde é um bom exemplo, pois o uso de códigos de barras nos seus produtos reduziu, de forma drástica, os custos logísticos.
O atendimento das encomendas também sofreu uma grande mudança com a utilização dos computadores, que substituíram as contagens de existências e acções de transcrição manuais. Desta forma, os templos de ciclo das encomendas foram muito reduzidos.
A distribuição de tarefas no atendimento de encomendas, o seu agrupamento, os limites de quantidade e o momento de entrada das encomendas afectam o tempo de ciclo, ou seja, se uma equipa de vendas se organizar e realizar várias tarefas simultaneamente, pode conseguir reduzir o tempo de ciclo da encomenda. A imposição de uma quantidade mínima de encomenda pode reduzir os custos de transporte. Juntando várias encomendas da mesma região, pode ser criada uma rota de transporte eficiente (Ballou, 2006, p. 123-125).
Sistemas de informação/Processamento de encomendas/Aviamento da encomenda
No aviamento realizam-se as seguintes tarefas: adquirir os itens retirando-os das existências, produzindo-os ou comprando-os; embalá-los para embarque; programar o embarque das entregas; e preparar a documentação para o embarque. Algumas destas actividades podem ser realizadas paralelamente às do atendimento da encomenda, reduzindo assim o tempo de ciclo.
As prioridades de aviamento estabelecidas têm influência no tempo total de processamento. Nem todas as empresas definem regras para a entrada e processamento de encomendas, o que gera atrasos significativos nas encomendas dos clientes. A definição de prioridades de aviamento evitam que os atrasos se dêem relativamente às encomendas dos clientes mais importantes. Algumas regras de priorização:
- primeira a ser recebida, primeira a ser processada;
- a encomenda de menor tempo de processamento;
- as encomendas com ordem de prioridade especificada;
- primeiro as encomendas menores e menos complexas;
- as encomendas com menor prazo de entrega;
- as encomendas com menos tempo até à data de entrega.
A escolha das regras de prioridade tem a ver com os critérios de justiça para os clientes. O aviamento das encomendas, independentemente de ser a partir de existências ou da produção de artigos, é somado ao tempo de ciclo da encomenda na mesma proporção do tempo de recolha, embalagem e produção. Quando não há existências para satisfazer uma encomenda, ocorre o parcelamento do embarque. A probabilidade de ocorrer parcelamento é relativamente elevada, mesmo com níveis de existências elevadas, pois a probabilidade de a encomenda não estar disponível nas existências é igual ao produto da probabilidade de disponibilidade de cada item. Deste modo, o tempo de processamento da encomenda poderá ser maior do que o esperado.
Para evitar entregas parciais e grandes demoras na informação sobre a situação das encomendas, deve-se reter a encomenda até à reposição dos itens em falta. Evidentemente, esta não é uma boa opção do ponto de vista do cliente, deve, portanto, ser uma opção ponderada entre os custos de informação e de transporte e o benefício na manutenção do nível dos serviços. Esta decisão requer procedimentos de processamento sofisticados, dos quais depende a eficiência da entrega. (Ballou, 2006, p. 125).
Sistemas de informação/Processamento de encomendas/Relatório da situação da encomenda
A última actividade do processamento de encomendas pretende manter os clientes informados acerca de quaisquer atrasos que possam ocorrer. As etapas deste processo são o acompanhamento e localização das encomendas ao longo de todo o seu ciclo; e a comunicação ao cliente da localização da encomenda, bem como, a previsão da data da sua entrega. Esta actividade não tem influência no tempo de ciclo do processamento da encomenda, porque é feita paralelamente às outras actividades.
A tecnologia tem grande influência no acompanhamento da situação das encomendas. Por exemplo, as empresas de transporte de encomendas conseguem informar os seus clientes da localização dos produtos que transportam através de códigos de barras com leitura a laser e uma rede mundial de computadores e software projectado de propósito para estas empresas, que é aperfeiçoado constantemente. Estes sistemas de informação conseguem identificar quem recebeu determinada encomenda, assim como a sua localização física e temporal (Ballou, 2006, p. 125-126).
Sistemas de informação/Processamento de encomendas/Exemplo de processamento de uma encomenda
O processamento de encomendas é feito nas mais variadas situações. Este exemplo, refere-se a uma encomenda industrial. Uma parte das actividades pode ser automatizada, no entanto, a maioria é feita manualmente. Um fabricante produz mangueiras, válvulas e conectores para uso industrial, de acordo com as especificações do cliente. Processa uma média de 50 pedidos por dia, tem um tempo de ciclo total entre 15 e 25 dias e um tempo de ciclo de processamento entre 4 e 8 dias. O sistema de processamento de encomendas foi projectado da seguinte forma (Ballou, 2006, p. 125-127):
- As encomendas do cliente são recebidas via postal ou telefónica na sede da empresa, do vendedor ou directamente do cliente. As encomendas não são feitas pela Web porque os clientes têm receio que sejam vistas pela concorrência. Não é usado o sistema electronic data interchange (EDI).
- Quando a sede recebe uma encomenda por telefone, esta é transcrita, resumidamente, por um funcionário para um formulário. As encomendas são encaminhadas, diariamente, para o gerente das vendas.
- O gerente das vendas analisa as encomendas e redige instruções para as encomendas dos clientes com necessidades diferenciadas.
- As encomendas são enviadas para os funcionários encarregues de as preparar, que as transcrevem para os formulários da empresa.
- As encomendas são enviadas para o departamento de contabilidade, onde é analisado o crédito do cliente, passando, de seguida, para o departamento de vendas para conferir os preços.
- O departamento de processamento de dados introduz as informações das encomendas no computador para serem transmitidas à fábrica, que faz uma verificação geral da encomenda.
- O representante do serviço ao cliente confere a encomenda, transmitindo-a à fábrica adequada. Uma notificação é enviada ao cliente por correio electrónico, confirmando o recebimento da encomenda.
Sistemas de informação/Rastreabilidade

A rastreabilidade é a capacidade de traçar a história, aplicação ou localização de um determinado produto ou produtos através de identificação (Figura 1). No que diz respeito a produtos, pode identificar a origem dos materiais ou componentes, a história de produção do produto ou ainda a distribuição e localização do produto depois de pronto (Olsen, 2009).<br.>
O significado da palavra rastreabilidade não está presente no dicionário da língua portuguesa, uma vez que é uma palavra composta pelo verbo rastrear, que tem por significado «seguir o rasto ou a pista de, investigar, inquirir, indagar» e pelo substantivo feminino habilidade, que tem por significado «qualidade de hábil» (Rodrigues, 2007, p. 16).
A mundialização dos mercados comerciais veio criar uma grande dificuldade na identificação da origem das matérias-primas e das condições em que a produção dos alimentos é realizada, tornando-se a rastreabilidade num instrumento fundamental. Esta indicação permite definir a responsabilidade de cada um dos intervenientes na produção e ainda, no caso de surgir um problema de saúde pública, identificar todo o lote contaminado e, se necessário, retirá-lo do mercado. Consequentemente, é possível uma intervenção rápida por parte das autoridades competentes (SOS, [2010]).
Os parceiros comerciais vêem-se obrigados a estabelecer a rastreabilidade, quer pela qualidade, quer pela legislação de um sector específico, o que faz com que seja de extrema importância nas indústrias. Antes de se implementar um sistema de rastreabilidade, deve-se ter em conta um aspecto muito importante que é a selecção do método de identificação. Para que um sistema seja eficiente, deve poder adaptar a rastreabilidade sem restrições, ou seja, deve ser independente do método de identificação (RQ LABELS, [200?]).
A rastreabilidade é identificação, este é um ponto que deve ficar esclarecido. O sistema de rastreabilidade deve ser obrigatoriamente configurado para que se realize um registo sobre todas as operações possíveis de alterar factores de qualidade de um produto.
Um bom sistema de rastreabilidade deve ter algumas características fundamentais, tais como:
- Flexibilidade: A implantação do sistema numa indústria pode-se tornar complicado pois cada empresa tem um método de trabalho diferente e máquinas diferentes. Apenas se consegue flexibilidade através de componentes modulares.
- Fácil manuseamento: Deve haver a capacidade para se conseguir um fácil manuseamento do sistema na indústria, com terminais que facilitem as instruções técnicas ao funcionário e nos escritórios deve existir um sistema de configuração e consulta simples.
- Nível de rastreabilidade facilmente configurável: O nível de rastreabilidade (fixo pela empresa) contribui com valor acrescentado para o produto, mas deve ser aplicado ao menor custo possível. Os processos e passos necessários para rastrear devem ser definidos pelos sistemas, uma vez que cabe à empresa fixar um nível de rastreabilidade equilibrado.
- Ser uma potente ferramenta de gestão: O sistema de rastreabilidade deve ajudar na tomada de decisões e na optimização de recursos.
- Capacidade de consulta de dados por parte dos clientes: Concluído e rastreado o processo produtivo, o cliente tem que conhecer os dados do produto que vai adquirir. Torna-se então fundamental que o sistema tenha um método para proporcionar tais dados. Existindo maior segurança e fidelização por parte do cliente, o produto adquire um valor acrescentado.
A rastreabilidade não garante a segurança alimentar, no entanto, a clareza perceptível e necessária para medidas de controlo eficazes é uma mais-valia que pode e deve ser utilizada pelos vários intervenientes no processo. Permite um maior controlo da rotulagem, de forma a gerar valor acrescentado, e aumenta a confiança dos consumidores (Fontes, 2004, p. 43).
Etapas de desenvolvimento - 9 fases | ||||||||
---|---|---|---|---|---|---|---|---|
Início: ![]() |
Básico: ![]() |
Criação: ![]() |
Desenvolvimento: ![]() |
Maturação: ![]() |
Revisão: ![]() |
Desenvolvido: ![]() |
Finalização: ![]() |
Abrangente: ![]() |
Rastreabilidade e tecnologias da informação
Unidades de expedição
Processo de rastreabilidade GS1
Sistema de rastreabilidade no sector alimentar
Sistemas de informação/Rastreabilidade/Introdução
Logística/Sistemas de informação/Rastreabilidade/Introdução
Sistemas de informação/Rastreabilidade/Rastreabilidade e tecnologias da informação
Rastreabilidade e tecnologias da informação (TI) são conceitos inseparáveis que permitem o acesso a toda a informação relacionada com o tratamento e com o lançamento de produtos. Existem softwares de apoio à gestão que são adaptáveis a qualquer sector de actividade e ao mesmo tempo possíveis de configuração para diversos periféricos, tais como «PDA» (Personal Digital Assistant) ou terminais de leitura óptica.
Existe uma possibilidade de gerir eficientemente as cadeias de valor multi-sectorial através do acesso à informação relativa ao percurso físico dos produtos, isto através da implementação de sistemas de identificação, tais como: unidades de expedição; bens tangíveis ou localizações e serviços. Com a implementação de várias soluções de armazenagem e logística, em comunicação em linha com o módulo de lotes e datas de validade, é possível, de uma forma rigorosa e ao pormenor, o controlo total de qualquer informação sobre a rastreabilidade dos produtos, sem deixar de parte os processos de recepção, armazenamento ou produção e expedição.
Acredita-se que o tratamento do processo de rastreabilidade terá um efeito de causalidade que irá ser visível nos intervenientes da cadeia de valor, ou seja, na produção e distribuição. Tal facto vai permitir um aumento exponencial da eficiência e produtividade da empresa (ARTSOFT, [2008]).
Sistemas de informação/Rastreabilidade/Unidades de expedição
<br.> As unidades de expedição são itens que não se destinam a ser vendidos directamente ao consumidor. Uma unidade de expedição pode ser um produto simples ou um conjunto de produtos embalados de modo a facilitar o manuseamento, armazenagem, encomenda, preparação ou expedição.
O código EAN-14 ou ITF-14 (Figura 1) consiste no EAN do produto precedido de uma variante logística de 1 dígito, sendo esta diferente para cada nível de embalagem e composta por um dígito de 0 a 9 escolhido pelo fabricante de acordo com as suas necessidades específicas (Rodrigues, 2007, p. 44-45):
- 0: Este valor converte o símbolo ITF-14 directamente no código EAN-13. No entanto não se considera 0 como uma variável logística, logo não se deve utilizar.
- 2: Utiliza-se para os códigos internos do utilizador, para circulação limitada de unidades de despacho. As unidades de despacho com esta variável logística só podem usar-se dentro de um circuito fechado sob a responsabilidade do utilizador que deve garantir que a sua circulação se limite à própria empresa, evitando assim que este código possa ser lido fora do seu domínio.
- 1 e 3 a 6: Estas variáveis logísticas são definidas pelo produtor como indicador de quantidade determinada, distinta da quantidade da unidade de consumo EAN-13. Desta forma, para uma unidade de consumo EAN-13, a variável logística, VL = 1 pode significar «Cartão de 24 unidades de consumo» e VL = 3 significa «Cartão de 48 unidades de consumo». Os produtores têm a responsabilidade de informar os seus clientes do valor que usam para cada variável logística de modo a que esta expresse a quantidade de unidades de consumo para cada DUN-14.
- 7 e 8: Processa-se de forma igual ao caso anterior, mas o produtor reserva estes valores para indicar que a unidade de despacho contem outras unidades de despacho.
- 9: Indicador de quantidade variável. O valor VL = 9 indica ao leitor, entenda-se por leitor um computador/scanner, que deve ler no seguimento do símbolo ITF-14, um segundo símbolo ITF de 6 dígitos conhecido como ADDENDUM ADD-ON, que identificará quantidades variáveis da unidade de consumo EAN-13.
Sistemas de informação/Rastreabilidade/Processo de rastreabilidade GS1
O processo de rastreabilidade GS1 é composto de 5 sub-processos e 18 passos (Rastreabilidade, [2009]):
Sub-Processos:
- Planear e Organizar;
- Alinhar Dados Mestre;
- Registar Dados;
- Requerer Rastreabilidade;
- Usar Informação.
Os sub-processos aplicados estão envolvidos numa série de passos sequenciais, que vão ser aplicados com o fim de garantir a disponibilidade de informação, baseando-se na ligação entre os parceiros comerciais de modo a que sejam cumpridas certas funcionalidades entre eles ao longo da cadeia de abastecimento. Tais processos visam todas e quaisquer necessidades do consumidor final.
- Planear & Organizar
O sub-processo 1 determina a forma de gerir as ligações entre as entradas, as fases de rastreio internas e as saídas. É uma fase de pré-requisito que determina como se atribuem, recolhem, partilham e mantêm os dados de rastreabilidade.
Este sub-processo inicia-se quando os parceiros comerciais tomam a decisão de garantir a rastreabilidade de produtos e é dividido em 2 passos importantes:
- Passo 1 – Atribuição, recolha, partilha e manutenção dos dados de rastreabilidade.
Baseia-se numa decisão sobre o sistema de identificação que se deve utilizar, bem como o transporte de informação.
- Passo 2 – Determinação das ligações entre as entradas, os processos internos, as saídas e como gerir essas ligações.
É neste passo que se vai garantir uma correcta conexão entre os artigos de entrada e de saída através do registo e manutenção de informação relativa aos mesmos. É um procedimento interno, pode ser entendido como rastreabilidade interna.
O sub-processo 1 termina quando os dois passos anteriores estão decididos, tem-se então o resultado de um plano para implementar um sistema de rastreabilidade.
- Alinhar dados mestre
No sub-processo 2 determina-se de que forma se vai atribuir a identificação às partes envolvidas e à localização física dos artigos.
Consegue-se garantir uma paridade adequada entre os dados de rastreabilidade e os artigos comerciais originados. Isto porque os parceiros comerciais conseguem compor os dados dos artigos de forma incisiva.
- Passo 3 – Atribuir identificação ao parceiro:
Parceiros comerciais devem estar claramente identificados com o GLN (Global Location Numbers).
- Passo 4 – Atribuir identificação aos locais físicos:
Qualquer localização interna ou externa que necessite ser detectada deve conter imperativamente identificação, podendo ser feito a um nível abrangente (localização do armazém), ou ao nível do detalhe dentro do armazém, mais propriamente identificação precisa da célula, através do GLN.
- Passo 5 – Atribuir identificação aos activos da empresa:
Qualquer activo, que precise de ser localizável, deve ser claramente e globalmente identificado, pelo GIAI (Global Individual Asset Identifier) e pelo GRAI (Global Returnable Asset Identifier), isto no caso desse activo ser retornável.
- Passo 6 – Atribuir identificação aos artigos comerciais:
Qualquer artigo comercial que precise de ser localizável, deve ser imperativamente identificado com um GTIN (Global Trade Item Number). Esta identificação aplica-se a qualquer nível de hierarquia do produto.
- Passo 7 – Trocar dados mestre:
Na troca de dados mestre tem que se assegurar uma afectação adequada de toda a informação importante.
Uma vez alcançado o total e correcto alinhamento de dados mestre (Figura 1), dá-se por terminado o sub-processo 2.
- Registar dados de rastreabilidade
O sub-processo 3 estabelece como atribuir e aplicar a identificação de artigos localizáveis e ainda como recolher, partilhar e armazenar os dados de rastreabilidade durante o fluxo físico (Figura 2).
Este sub-processo inicia-se quando existe necessidade de responder a um processo gerido por vendas, isto é, quando se cria inventário adicional directa ou indirectamente.
- Passo 8 – Atribuir identificação a um artigo localizável aquando da sua criação:
A identificação do artigo de ser única e atribuída aquando da sua concepção física. Deve ser decidido qual o nível de rastreabilidade do artigo e posteriormente o conjunto de dados que serão passíveis de troca entre os parceiros comerciais.
Quando o artigo localizável é um artigo comercial:
Normalmente qualquer identificação de artigo deve ser realizada através do GTIN («Global Trade Item Number»), no entanto para que se aplique o sistema de rastreabilidade, esta identificação não é suficiente, pelo que é necessário adicionar mais informação ao artigo. Esta informação consiste no número de série, SGTIN («Serialized Global Trade Identification Number»).
Quando o artigo localizável é uma unidade logística:
A identificação é feita através do SSCC («Serial Shipping Container Code»).
- Passo 9 – Associar a identificação ao item através do transportador de identificação ou de um documento de acompanhamento, aquando de uma modificação:
Sempre que um artigo é modificado/transformado, este deve anexar uma identificação da ocorrência no próprio artigo, caso não seja possível deverá existir um documento anexado ao artigo com tais modificações, para efeitos de identificação.
- Passo 10 – Aquando do envio e recepção, capturar a identificação do item ou do activo social que o contém a partir do transportador de identificação:
Todas as fontes e destinos de artigos localizáveis, devem recolher a identificação do item ou do activo.
- Passo 11 – Recolher, por qualquer método, todos os dados inclusivé informação de rastreabilidade de fontes internas e externas:
Deve ser fornecido pela origem do artigo, qualquer forma de reunir e associar toda e qualquer informação relevante para o artigo.
- Passo 12 – Partilha de informação de rastreabilidade através de qualquer meio possível.
- Passo 13 – Armazenar os dados de rastreabilidade:
O armazenamento de dados de rastreabilidade conclui-se quando o artigo é entregue no ponto final de venda de produtos, ou ainda quando o artigo é destruído. Entenda-se por destruído a saída do processo de rastreabilidade.
O objectivo adquirido através deste sub-processo é a capacidade que os parceiros de rastreabilidade obtém de conseguir identificar os artigos enquanto estes se movem ao longo de uma cadeia de abastecimento.
- Requerer rastreabilidade
Este é um sub-processo determinante na rastreabilidade, uma vez que pode ser iniciado um pedido de rastreabilidade por parte dos parceiros de rastreabilidade devido a uma queixa das autoridades ou do consumidor como consequência a um produto com defeito, podendo levar à recolha ou retirada desse produto do mercado (Figura 3).
A rastreabilidade deve funcionar um passo à frente e um passo atrás na cadeia de abastecimento, sendo que o pedido de rastreabilidade pode originar pedidos vários niveis abaixo ou acima da cadeia de abastecimento.
Passo 14 – Iniciar um pedido de rastreabilidade:
O parceiro comercial que pretenda iniciar um pedido de rastreabilidade tem que fornecer alguns dados para que a fonte de rastreabilidade consiga encontrar toda a informação relativa ao artigo pretendido. Os dados fornecidos devem ser os seguintes: Identificação do artigo; identificação do parceiro ou os seus atributos; identificação do local; data e hora; período de tempo e processo de identificação.
Passo 15 – Recepção do pedido de rastreabilidade:
Receber e identificar de forma correcta os requisitos de pedido, uma vez que o pedido pode dar origem a outras solicitações de rastreabilidade posteriores a outros parceiros.
Passo 16 – Enviar a resposta ao pedido de rastreabilidade.
Passo 17 – Receber a resposta ao pedido de rastreabilidade.
- Usar informação
Este sub-processo inicia-se quando parceiros de negócio decidem usar a informação, permitindo o uso dos processos anteriores para eventuais necessidades.
Passo 18 – Actuar.
O objectivo do sub-processo é permitir o uso da restrabilidade e cumprir os requisitos legais, de forma que todos os passos de rastreabilidade estão inseridos nos requerimentos legais de negócio.
- Tabela 1. Grelha de verificação para a implementação de rastreabilidade
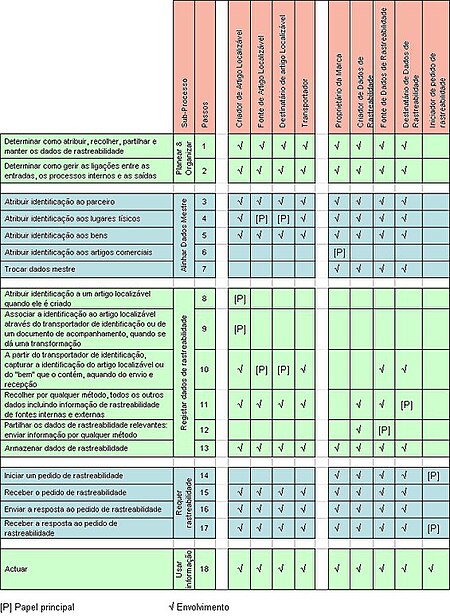
Sistemas de informação/Rastreabilidade/Sistema de rastreabilidade no sector alimentar
Etapas de desenvolvimento - 9 fases | ||||||||
---|---|---|---|---|---|---|---|---|
Início: ![]() |
Básico: ![]() |
Criação: ![]() |
Desenvolvimento: ![]() |
Maturação: ![]() |
Revisão: ![]() |
Desenvolvido: ![]() |
Finalização: ![]() |
Abrangente: ![]() |
Um bom sistema de rastreabilidade no sector alimentar deve englobar os seguintes objectivos primários: cumprimento da legislação de segurança alimentar; melhoria da imagem e da qualidade, ou seja, certificação de processos de produção; e melhoria do processo produtivo com uma gestão eficiente e uma produção óptima.
Para que o sistema de rastreabilidade seja um investimento rentável ao nível de todas as empresas do mercado, inclusive para as pequenas e médias empresas, estes objectivos têm que ser congregados de forma a que coloque a empresa numa posição proveitosa e lucrativa face à concorrência.
Para efeitos de rastreabilidade, o sistema considera os seguintes elementos: pedidos de compra; provedores; identificadores; salas/câmaras; produtos; operários; fórmulas/procedimentos; desmanchas/divisões; operações gerais; pedidos de venda/expedição e ainda clientes.
Em suma, a informação que o sistema dispõe é a da fábrica na totalidade, tal facto permitirá optimizar a produção dispondo de forma imediata a informação de todos os pedidos de compra, venda, o estado dos pedidos e os «stocks» existentes dos diferentes produtos, entre outros.
De forma a existir uma comunicação eficiente com outros sistemas existentes, o sistema de rastreabilidade deve ser integrado e ajustado à empresa (RQ LABELS, [200?]).
Características fundamentais
Rastreabilidade e qualidade alimentar
Autenticidade
Melhorar a cadeia de abastecimento
Sistemas de informação/Rastreabilidade/Sistema de rastreabilidade no sector alimentar/Características fundamentais
Identificação não é rastreabilidade. São duas palavras com significados diferentes. A identificação é um óptimo investimento a fazer para implantar um bom sistema de rastreabilidade, no entanto não é o único, ainda que a identificação seja um meio para conseguir a rastreabilidade. Todos os sistemas de rastreabilidade devem ter como componentes essenciais a identificação e os módulos central; distribuído nas instalações; de consulta e administração; e ainda de publicação (RQ LABELS, [200?]).
- Identificação
A identificação dos produtos/animais é fundamental para o funcionamento do sistema de rastreabilidade, realizando-se através de alguns métodos existentes actualmente:
- Etiquetas com códigos de barras: Os códigos de barras identificam os elementos a rastrear. Essa identificação é realizada recorrendo ao código interno facilmente gerado pelo sistema. Este permite controlar a rastreabilidade e gerar etiquetas de forma automática, no entanto não permite directamente a identificação de animais, mas apenas a documentação e os produtos embalados, o que proporciona uma grande flexibilidade ao método de etiquetas com códigos de barras.
- Etiquetas com Chip RFId: Chip implantado em animais que possui um código único, facilmente aplicável e editável ao longo de todo o processo, é implantado na orelha, ficando presente durante toda a existência do animal. A descodificação do número pode ser efectuada com um leitor electrónico ou através de identificação visual caso seja impressa no chip (Figura 1). Este tipo de etiqueta não se perde, possui garantia de certeza e é bastante fiável na identificação.
- Bolo: Bolo de cerâmica constituído por um micro chip interno que possui um número de identificação único. É um método fácil de aplicar, o que garante um factor de confiança na identificação. É necessário um leitor electrónico para realizar a sua descodificação.
- Leitores
Existem alguns tipos de leitores para além da leitura visual, dos quais merecem distinção os seguintes: Módulos de leitura estáticos de chips RFId; módulos de leitura portáteis (permite adicionar dados ao leitor electrónico) e o mais conhecido leitor de código de barras.
Sistemas de informação/Rastreabilidade/Sistema de rastreabilidade no sector alimentar/Rastreabilidade e qualidade alimentar
No que se refere à escolha alimentar, torna-se importante estudar a qualidade do ponto de vista do consumidor. Isto porque é o consumidor que decide Quando, Onde, Como e O Que comprar ou não comprar, comer ou não comer (Fontes, 2004, p. 17-42).
As relações entre as características de um produto, os motivos de compra e os atributos evidenciados, experimentados e acreditados da qualidade são factores que motivam o consumidor a adquirir um bem alimentar. São atributos evidenciados aqueles em que é possível, por parte do consumidor, avaliar a qualidade no local e momento da aquisição, como, por exemplo, a marca, preço, embalagem e rotulagem. Os atributos experimentados, como o próprio nome sugere, são aqueles que são avaliados após a compra, como, por exemplo, o sabor de um alimento. Por outro lado, nos atributos acreditados, o consumidor não tem a capacidade de julgar por si o produto, ou seja, vai basear-se na opinião de outras pessoas, como, por exemplo, o modo de produção.
Existe um aumento da importância da dimensão acreditada em relação à dimensão evidenciada e experimentada, sendo que a percepção da qualidade se encontra interligada à comunicação. A rastreabilidade pode constituir uma forma de diferenciar atributos acreditados. A credibilidade da fonte e a motivação e habilidade do receptor para processar informação são os principais determinantes de uma comunicação persuasiva.
- Credibilidade
Torna-se complicado e problemático comercializar bens alimentares baseados na dimensão acreditada, por exigir a concepção de meios para aumentar a credibilidade, nomeadamente um sistema de rastreabilidade eficaz. Muitos dos atributos considerados, nomeadamente os biológicos, são essencialmente acreditados, podendo ser vistos com algum cepticismo, daí os consumidores exigirem rastreabilidade.
É importante existir rastreabilidade no seio da cadeia logística, de forma a garantir a credibilidade da informação nos rótulos sobre os atributos acreditados. O comportamento ao longo da cadeia pela qual o produto passa influencia a credibilidade. Para tal sistema funcionar, é necessário proteger a cadeia de potenciais riscos, o que só é possível se todas as partes se empenharem e cooperarem, ou seja, funcionarem de forma íntegrada.
Uma vez que existe credibilidade, a informação torna-se mais útil e alvo de maior procura. Fornecer mais informação, no entanto, pode conduzir a um aumento da probabilidade de utilização errada.
- Vantagens da rastreabilidade
As vantagens no sector alimentar são os benefícios potenciais para os consumidores, o sector privado e o sector público.
No que diz respeito aos consumidores, os benefícios que obtêm são essencialmente não visíveis, ao contribuir para uma maior segurança alimentar, retirando eficazmente do mercado os produtos numa situação de risco. Permite ainda que se evitem alimentos ou ingredientes por razões de alergia, intolerância ou estilos de vida, ou seja, existe o acesso a informação exacta e permite ainda que, quando face a produtos concebidos de formas diferentes, o cliente realize um processo de escolha.
O sector privado, apresenta alguns benefícios, tais como: o diagnóstico de problemas na produção; o cumprimento da legislação relevante; possibilita o acesso à informação anexada sobre produtos, processos associados e ingredientes; minimização dos custos associados a uma retirada de produto do mercado; criação de produtos diferenciados e ainda, preservação da identidade de produtos.
No sector público, as vantagens apresentadas são: protecção da saúde publica através da retirada eficaz de produtos dos pontos de venda; obtenção de informação desejada por parte das autoridades de forma a facilitar o fácil desempenho das suas funções; prevenção de fraude nos casos onde os métodos analíticos não podem ser utilizados como prova de autenticação; controlo de doenças dos animais através de uma rápida identificação das fontes da doença e possíveis contactos perigosos.
- Custos da rastreabilidade
Os custos que incidem em cada agente são difíceis de estimar uma vez que são utilizadas várias técnicas/sistemas de rastreio. Pode afirmar-se, contudo, que dependendo do poder de mercado, os custos incidem desproporcionalmente em todos os agentes da cadeia alimentar, resultado da capacidade de transferir custos. A extensão dos custos varia significativamente entre sectores e agentes, variando com o tipo de tecnologia utilizada, a quantidade de informação abrangida e a complexidade da cadeia alimentar.
Sistemas de informação/Rastreabilidade/Sistema de rastreabilidade no sector alimentar/Autenticidade
<br.> A autenticidade de um produto significa a certeza de que este provém das fontes referidas, sem ser alvo de alterações, ou seja, significa que corresponde à expectativa associada. Existem várias metodologias analíticas utilizadas na determinação da autenticidade, mas normalmente baseiam-se em quatro importantes: métodos imunológicos, análise sensorial, análise microscópica e métodos de ADN (Ácido desoxirribonucleico) (Rodrigues, 2007, p. 3-7).
- Óleos
Composição em ácidos gordos, esteróis, triglicéridos, vitaminas, tocoferóis, tocotrienóis e estigmastadienos. São utilizados para despistar as características dos óleos e para verificação da autenticidade. Existe um controlo da autenticidade em azeites e com denominação de origem protegida.
- Produtos cárneos
Existe uma falsificação nos produtos cárneos através de adição de substâncias com menor valor comercial, por exemplo, água, amido ou gelatina. Para detecção deste género de adulteração subsiste uma verificação da presença de marcadores de produto genuíno.
- Género animal
A União Europeia importa e exporta carne com uma diferença de 130€ por cada 100 kg de carne, dependendo se estas provem de fêmeas ou machos, sendo que a última é considerada de mais alta qualidade. Este tipo de carne é controlada pelo método PCR (Polymerase Chain Reaction). Acontece o mesmo com as empresas comerciais que pagam preços muito mais altos pela carne de machos. A Medigenomix é um laboratório que realiza testes para determinar o género do animal através do ADN da carne através do mesmo método PCR como requerido pela EC-regulation.
- Bebidas alcoólicas
A falsificação de bebidas alcoólicas ocorre particularmente em bebidas com alto valor comercial como, por exemplo, os whiskies importados (Tabela 1).
No entanto, também existem bebidas alcoólicas nacionais susceptíveis de serem falsificadas, como as aguardentes.
Normalmente as bebidas alcoólicas falsificadas são produzidas através da adição de água às bebidas autênticas, ou ainda por mistura de álcool, aroma ou corantes, como o caramelo.
Tipo de Produto | Total | Aprovados | Falsificados | Falsificados (%) | |
Whisky nacional | 141 | 27 | 114 | 81 | |
Whisky importado | 266 | 108 | 158 | 59 | |
Vodka | 71 | 25 | 46 | 65 | |
Conhaque | 4 | 1 | 3 | 75 | |
Conhaque de gengibre | 41 | 8 | 33 | 80 | |
Amargo | 16 | 2 | 14 | 88 | |
Rum | 2 | 2 | 0 | -- | |
Aperitivo | 6 | 4 | 2 | 33 | |
Licor | 8 | 7 | 1 | 13 | |
Gim | 2 | 2 | 0 | -- | |
Tequila | 5 | 5 | 0 | -- | |
Total | 608 | 217 | 391 | ||
Não existe nenhum tipo de controlo nas matérias-primas que são utilizadas no processo de falsificação, o que pode causar potenciais riscos para a saúde humana quando ingeridas. Isto pode suceder devido à presença do metanol ou de outras matérias que têm valores acima dos limites impostos pela legislação em vigor.
Existem ainda componentes secundários (aldeídos, álcoois, ácidos) que são formados durante o processo de produção de uma bebida alcoólica. Estes ainda que em concentrações mais baixas, na ordem dos 0,5%, são igualmente importantes na fixação da qualidade do produto final.
Nas bebidas falsificadas, ou ainda denominadas de clandestinas, o metanol (constituinte natural presente nas bebidas alcoólicas) é submetido a uma mistura com o álcool não potável, o que eleva bastante a percentagem de valor presente na bebida, valor este que se situa muito acima dos impostos pela legislação. Como é de prever, este fenómeno conduz a sérios problemas de saúde.
O teor máximo de metanol obtido pelo processo de fabricação dos diferentes tipos de bebidas alcoólicas pode atingir até 1 grama por 100 ml de álcool anidro. Ou seja, bebidas com concentrações de metanol acima deste valor podem tratar-se de falsificações.
- Arroz basmati
O arroz basmati tem um aroma particular e os seus grãos têm uma forma característica, e sendo um produto de qualidade e reconhecido, atrai preços elevados. A falsificação do arroz tem sido frequentemente citada, identificada através da forma dos grãos de arroz. Um estudo efectuado pela agência FSA (Food Standards Agency), no ano de 2003, mostrou que num total de 363 amostras examinadas, 62 das amostras continham arroz falsificado.
Há dezasseis variedades de arroz que têm aprovação internacional para serem identificados como Basmati, sendo que uma mistura até 20% com outras espécies é aceite. No entanto, a FSA promove uma campanha para se impor um limite de 7%.
É necessário estabelecer um sistema exaustivo de rastreabilidade nas empresas do sector alimentar e do sector dos alimentos para animais, de modo a possibilitar retiradas do mercado de forma orientada e precisa, ou a informar os consumidores ou os funcionários responsáveis pelos controlos, evitando-se assim a eventualidade de perturbações desnecessárias em caso de problemas com a segurança dos géneros alimentícios.
Sistemas de informação/Indicadores de desempenho
Etapas de desenvolvimento - 9 fases | ||||||||
---|---|---|---|---|---|---|---|---|
Início: ![]() |
Básico: ![]() |
Criação: ![]() |
Desenvolvimento: ![]() |
Maturação: ![]() |
Revisão: ![]() |
Desenvolvido: ![]() |
Finalização: ![]() |
Abrangente: ![]() |
Certa vez um esperançoso vendedor perguntou a um comprador de uma fábrica metalúrgica, «Que tipo de brocas é que precisa na sua empresa?», ao que o comprador respondeu: «Eu não preciso de broca nenhumas, o que eu preciso é de buracos!»
Do mesmo modo, engenheiros e gestores ao considerarem a aquisição de equipamentos e sistemas de movimentação de material devem perceber que o que devem realmente comprar é maior produtividade. A natureza de um sistema de movimentação de material – quer se trate de camiões, transportadores, guindastes ou outros tipos de equipamentos – é a de um meio para um fim, e esse fim é melhor produtividade. Assim, qualquer avaliação de planos alternativos de movimentação de material deve de considerar como cada alternativa irá afectar a produtividade da instalação ou operação a que se destina.
A necessidade de melhorar a produtividade tornou-se uma questão importante na indústria e promete ser uma preocupação constante. À medida que os recursos disponíveis e localizações desejáveis são cada vez mais limitados, a necessidade de «obter o máximo com o que se tem» torna-se uma necessidade. Qualquer sistema dentro de uma fábrica deve de trabalhar de forma eficiente de modo a reduzir o custo de produção e ser competitivo.
Alguns indicadores de desempenho relacionados com a configuração das instalações e actividades de movimentação de material são usados como medidas de desenvolvimento de um sistema. Estes indicadores podem ser calculados para diversos tipos de configurações apresentados em tabelas para ajudar a determinar qual a melhor configuração, e sugere, quais os desempenhos que devem de ser monitorizados nas operações de movimentação de material. Esses indicadores não constituem uma lista exaustiva e uma organização pode desenvolver outros indicadores que identifiquem mais claramente os factores com que se preocupa e que mais adequados às situações específicas de uma fábrica ou indústria.
Há poucos valores padrão e aceitáveis para esses indicadores, ao nível da indústria, que possam ser comparados com os obtidos numa empresa em particular, ainda que esteja a ser efectuado trabalho por algumas sociedades e associações profissionais para desenvolver padrões de produtividade. Esses indicadores podem ser mais úteis para estabelecer tendências e identificar a necessidade de medidas correctivas, uma vez que podem fornecer informações úteis de forma contínua sobre o desempenho do sistema. As comparações também podem ser feitas com outras fábricas da mesma indústria, ou em instalações onde são efectuadas operações semelhantes de movimentação de material.
É necessário ter o cuidado de assegurar que os indicadores de desempenho utilizados são razoáveis e reflectem um desempenho positivo. Alguns indicadores de desempenho são realizados com uma estratégia de curto prazo, o que é desvantajoso para uma organização cujo seu ponto de vista seja de longo prazo. As decisões importantes a ser realizadas numa empresa devem de ter em conta os indicadores de desempenho.
Os dados necessários para calcular os indicadores de desempenho devem estar prontamente disponíveis, como tal inicialmente a recolha de informação pode dar alguns problemas. A cooperação interdepartamental é essencial na formação e recolha de dados para que sejam superadas as dificuldades iniciais de identificar e quantificar as informações necessárias para o cálculo dos indicadores de desempenho. O processo de recolha de dados é um contributo para os profissionais movimentação de material de maneira que os auxilia a identificar problemas associados às operações e instalações numa área de produção.
A monitorização periódica dos indicadores de desempenho é efectuada para confirmar se valores estão dentro do aceitável. Qualquer grande flutuação de período para período é um sinal claro de que o sistema está a funcionar com problemas e que precisa de uma investigação e controlo. O desempenho de um sistema depois de instalado e posto a funcionar é verificado analisando as tendências, ou mudanças dos indicadores de desempenho. Se os aumentos de desempenho são alcançados, o sistema é considerado como cumprindo os objectivos. Caso contrário, a limpeza ou modificação do sistema é necessário para atingir os níveis desejados de desempenho.
A movimentação de material não pode ter soluções «tapa buracos», têm de ser medidas que tenham a capacidade de resolver um problema imediato através da instalação de um equipamento. De modo contrário, devem ser assentes numa abordagem sistemática e utilizar um sistema sólido de pensamentos.
Valor Económico Acrescentado (EVA)
Indicadores AECOC
Taxa de rotação dos stocks
Indicadores de utilização de recursos: pessoas
Indicadores de utilização de recursos: equipamentos
Indicadores de controlo de gestão: movimento
Movimento por operação
- Distância média por movimento
Sistemas de informação/Indicadores de desempenho/Valor Económico Acrescentado (EVA)
O Valor Económico Acrescentado, Economic Value Added (EVA) é o excesso do resultado operacional, após os impostos, relativamente à rendibilidade exigida pelos credores e accionistas. Consiste, portanto, no valor absoluto da diferença entre a rendibilidade do capital investido e o custo médio do capital, ou seja, a rendibilidade exigida pelos investidores. Por outras palavras, é o resultado líquido deduzido do custo do capital próprio (miCPM, 2004). A fórmula básica deste valor é (Medeiros, 2002, p. 37):
EVA = (Rendibilidade do capital investido − Custo do capital investido) × Capital investido
Esta medida financeira de desempenho pode ser aplicada em qualquer empresa do sistema logístico. Para orientar as estratégias de crescimento de um sistema logístico é importante ter em atenção os seguintes aspectos: aumento de produtividade, maximização de receitas, minimização de custos, utilização dos activos e estratégia de investimento. Neste contexto, o EVA revela-se uma ferramenta importante de gestão.
O EVA é calculado a partir da variação de lucros económicos de dois períodos de avaliação numa empresa. Tendo em conta uma nova concepção do EVA, que compara o fluxo de caixa incremental com a média do risco ajustado do custo do capital, apenas quando o custo económico do projecto é excedido pelo fluxo de caixa é que as empresas adicionam valor.
O cálculo deste indicador tem importância na avaliação dos resultados finais duma empresa do sector logístico. A aplicação do conceito de EVA na cadeia logística pode ser baseada no desempenho financeiro de cada componente do sistema que, através do cálculo de variáveis envolvidas, poderá ser positivo (criação de valor) ou negativo (destruição de valor) (Kato, 2003, p. 117-118).
Para uma melhor compreensão da aplicação deste conceito, suponha-se o caso duma empresa que possua um capital de 200 milhões e um custo de capital de 10%, sendo, portanto, a sua taxa de rendibilidade desejada de 20 milhões. Se ela ganhar 100 milhões, o seu EVA será de 80 milhões. Embora estes cálculos exijam pequenas mudanças nas contas da empresa, o raciocínio é relativamente fácil de ser compreendido (Medeiros, 2002, p. 2).
A Figura 1 demonstra o princípio de funcionamento do EVA:

Sistemas de informação/Indicadores de desempenho/Indicadores AECOC
A Associação Espanhola de Codificação Comercial (AECOC) é uma das maiores associações empresariais espanholas, com mais de 24 mil associados, em que fabricantes e distribuidores trabalham conjuntamente com o intuito de proporcionar mais valor aos consumidores.
Criada para impulsionar a introdução do código de barras em Espanha, esta associação também tem uma importante contribuição nos sistemas de logística e transporte, prestando serviços de consultoria, formação e investigação, não só nessas áreas, mas também no marketing, comércio electrónico - transferência electrónica de dados (EDI), codificação-identificação e segurança alimentar e nutricional. Com o objectivo de identificar o desempenho nestas áreas, a AECOC associa várias empresas que contribuem com cerca de 20% para o PIB espanhol. Esta interacção tornou-se uma multi-parceria nos sectores mais diversos, tais como alimentar, têxteis, ferramentas e bricolage, produtos farmacêuticos, desportos e saúde. Em cada um destes sectores a AECOC procura detectar oportunidades de melhoria e impulsionar práticas de eficiência (AECOC, [2009]). É neste sentido que as recomendações AECOC para a Logística (RAL) apresentam indicadores para o nível de serviço e eficiência, medidos periodicamente (AECOC, 2003).
- Indicador de eficiência
KPI 1 - Aplicação da Ficha Logística RAL
O indicador de eficiência tem como objectivo medir o nível de aplicação da ficha RAL como medida de eficiência entre distribuidores e fornecedores. A fórmula geral utilizada é a seguinte:
Aplicação da Ficha Logística RAL (%) = (Facturação com a ficha RAL / Total da facturação) × 100
Com a facturação em valor do preço de venda e periodicidade semestral.
Existem ainda outras fórmulas de cálculo, consoante a avaliação seja realizada pelo distribuidor ou pelo fornecedor.
Avaliação realizada pelo distribuidor:
Aplicação da Ficha Logística RAL (%) = (Número de fornecedores com a ficha RAL / Número total de fornecedores) × 100
Sempre que a avaliação é realizada pelo fornecedor:
Aplicação da Ficha Logística RAL (%) = (Número de clientes com a ficha RAL / Número total de clientes) × 100
- Indicadores de serviço
Os indicadores de serviço dividem-se em: Entregas a Tempo, Entregas Completas, Qualidade da Entrega/Recepção e Tempo de Descarga.
KPI 2 - Entregas a Tempo
O indicador Entregas a Tempo mede o nível de cumprimento mensal da data e hora de entrega acordada entre o fornecedor e distribuidor, com uma margem de ± 15 minutos:
Entregas a Tempo (%) = (Número de encomendas entregues a tempo / Número total de encomendas entregues) × 100
KPI 3 - Entregas Completas
As Entregas Completas permitem conhecer o nível de cumprimento mensal da entrega das quantidades encomendadas pelo distribuidor ao fornecedor, tanto a nível das unidade como a nível das linhas da encomenda:
Entregas Completas (%) (unidades) = (Número de unidades recebidas / Número total de unidades encomendadas) × 100
Entregas Completas (%) (linhas da encomenda) = (Número de linhas da encomenda recebidas / Número total de linhas da encomenda) × 100
KPI 4 - Qualidade da Entrega/Recepção
A qualidade da entrega/recepção permite conhecer o nível de ocorrências no acto de entrega/recepção, podendo ser medida tanto pelo distribuidor, como pelo fornecedor.
Qualidade medida pelo distribuidor:
Encomendas com ocorrências (%) = (Número de linhas da encomenda com ocorrências / Número total de linhas da encomenda) × 100
Quando a qualidade é medida pelo fornecedor:
Encomendas com ocorrências (%) = (Número de encomendas devolvidas total ou parcialmente / Número total de encomendas) × 100
KPI 5 - Tempo de Descarga
O indicador Tempo de Descarga (tempo que decorre entre a entrega da documentação à chegada, até à saída do cliente com a documentação já assinada) tem como objectivo determinar o nível de cumprimento mensal de duas horas ou menos de tempo de descarga:
Encomendas Descarregadas a Tempo (%) = (Número de encomendas descarregadas em duas horas ou menos / Número total de encomendas entregues) × 100
Sistemas de informação/Indicadores de desempenho/Taxa de rotação dos stocks
Segundo Malheiro ([2005], p. 1-2), a taxa de rotação dos stocks, um dos indicadores de gestão mais eficazes, baseia-se na relação entre o movimento anual e o stock médio, ou seja, o número de vezes que o stock médio roda por ano. Por outras palavras, este indicador traduz as necessidades de n meses que o stock é capaz de satisfazer.
Imagine-se, por exemplo, que a empresa Agape, uma das maiores fabricantes mundiais de impressoras, mantém um stock relativo a três meses da produção, ou de venda. Logo, pode afirmar-se que a sua taxa de rotação dos stocks é 4.
O cálculo da taxa de rotação dos stocks, para uma única referência de produtos, baseia-se na seguinte fórmula (em quantidades):
Taxa de rotação dos stocks = Consumo médio anual / Stock disponível
No caso de existir mais do que uma referência de produtos, o indicador é calculado da seguinte forma (em valor monetário):
Taxa de rotação dos stocks = Valor do consumo médio anual / Valor do stock disponível
Considerando agora um conjunto de artigos diferentes ou as suas classificações possíveis, isto é, produtos acabados, produtos em vias de fabrico ou matérias-primas, pode calcular-se a taxa de rotação dos stocks do seguinte modo:
Taxa de rotação dos stocks = Custo das vendas / Valor do stock médio agregado
Com o valor do stock médio agregado relativo às unidades mantidas em stock, num determinado período de tempo.
Apesar de a taxa de rotação dos stocks ser muito importante na tomada de decisões relativas ao nível de stock a manter num determinado período, não é condição suficiente. É essencial saber prever as eventuais irregularidades de consumo e os atrasos nos prazos de entrega dos fornecedores. Além disso, é importante comparar o capital investido em stocks na mesma empresa, ao longo do tempo, ou entre empresas do mesmo sector.
Sistemas de informação/Indicadores de desempenho/Indicadores de utilização de recursos: pessoas
Etapas de desenvolvimento - 9 fases | ||||||||
---|---|---|---|---|---|---|---|---|
Início: ![]() |
Básico: ![]() |
Criação: ![]() |
Desenvolvimento: ![]() |
Maturação: ![]() |
Revisão: ![]() |
Desenvolvido: ![]() |
Finalização: ![]() |
Abrangente: ![]() |
De acordo com White Jr. (1985, p. 323), se a produtividade for definida como a produção por homem-hora, o único recurso tido em conta são as pessoas. Os dois métodos tradicionais usados no aumento da produtividade são a substituição do trabalho por capital ou tecnologia e o desenvolvimento de métodos de trabalho mais eficientes. Enquanto o aperfeiçoamento dos métodos e das tecnologias contribuiu para a melhoria da produtividade na produção, há uma oportunidade considerável para melhorias nas áreas da movimentação de materiais e armazenagem. Poucas organizações têm desenvolvido novos métodos e padrões de trabalho para a movimentação de materiais e armazenagem, apesar de ambas utilizarem mão de obra intensivamente. Além desses dois métodos para melhorar a produtividade, esta pode ser também aumentada por melhorias na gestão. Estar ocupado não significa, necessariamente, ser produtivo, logo é necessária uma boa gestão que garanta que as pessoas estão a ser produtivas.
As medidas que são utilizadas para avaliar a utilização de pessoas na movimentação de materiais são a:
Mão de obra na movimentação de materiais; a
Mão de obra directa na movimentação de materiais; e a
Perda de mão de obra directa em movimentações
Sistemas de informação/Indicadores de desempenho/Indicadores de utilização de recursos: pessoas/Mão de obra na movimentação de materiais
O indicador de mão de obra na movimentação de materiais mede a proporção da força de trabalho atribuída a tarefas de movimentação de materiais, podendo basear-se tanto nos custos directos do pessoal envolvido, como no número de pessoas, isto é (White Jr., 1985, p. 323-325):
Indicador de mão de obra na movimentação de materiais = Pessoal destacado para tarefas de movimentação de materiais / Total da mão de obra directa
Este indicador, usado como um sinal de monitorização, permite obter gráficos que devem ser actualizados mensalmente, de modo a detectar alterações que possam ocorrer. Caso essas alterações se verifiquem, devem ser investigadas as respectivas causas. É aconselhável considerar este indicador como uma meta para ser usada na avaliação de planos alternativos de produção.
Considere-se, por exemplo, que foi efectuada uma análise a uma determinada fábrica. Para o cálculo do indicador de mão de obra directa na movimentação de materiais, os custos anuais envolvidos foram avaliados da seguinte forma:
- Trabalho dos operadores de equipamentos de movimentação de materiais..................................254,85€
- Actividades relacionadas com a movimentação de materiais......................................................235,15€
- Actividades de apoio..............................................................................................................178,72€
- Custo total de mão de obra em movimentação de materiais.......................................................668,72€
Se o custo total da folha de pagamentos anual é 5 857,90€, a mão de obra na movimentação de materiais foi de:
(668,72 / 5 857,90) × 100 = 11,41%
Sistemas de informação/Indicadores de desempenho/Indicadores de utilização de recursos: pessoas/Mão de obra directa na movimentação de materiais
White Jr. (1985, p. 325) define o indicador de mão de obra directa na movimentação de materiais como a proporção do tempo de mão de obra directa dispendido na movimentação de materiais, ou seja:
Tempo despendido na movimentação de materiais pela mão de obra directa (h) / Tempo total de mão de obra directa (h)
Podendo, também ser calculado da seguinte forma:
Mão de obra directa na movimentação de materiais (UM) / Mão de obra directa total (UM) [proporção]
Geralmente, é preferível manter um valor baixo para este indicador. As alternativas disponíveis para reduzir este valor consistem no uso de mão de obra indirecta na movimentação de materiais e na eliminação ou redução da quantidade de movimentações de materiais necessárias, recorrendo à mecanização ou automação das actividades de movimentação.
É importante, não só o estabelecimento de níveis de referência, como também uma observação mensal que permita avaliar o desempenho, com base numa estimativa de valores obtida por amostragem.
Exemplo de aplicação: Na empresa XPTO foram recolhidas amostras em 5 departamentos: I, II, III, IV e V. Das 1 050 observações escolhidas aleatoriamente, verificou-se 190 vezes o envolvimento da mão de obra directa na realização de tarefas de movimentação de materiais. Os resultados estão resumidos na seguinte tabela:
Dep. | Número de trabalhadores directamente envolvidos |
Número de observações |
Número de movimentações de materiais |
Movimentação de materiais (4)/(3) |
Folha de pagamentos anual |
Mão de obra na movimentação de materiais (5)x(6) |
(1) | (2) | (3) | (4) | (5) | (6) | (7) |
-Percentagem- | ----UM---- | ----UM---- | ||||
I | 35 | 210 | 30 | 14,29 | 510 | 72,88 |
II | 45 | 290 | 44 | 15,17 | 735 | 111,50 |
III | 20 | 90 | 16 | 17,28 | 190 | 33,78 |
IV | 50 | 330 | 75 | 22,73 | 860 | 195,48 |
V | 25 | 130 | 25 | 19,23 | 275 | 52,88 |
Total | 175 | 1050 | 190 | 18,10 | 2570 | 465,05 |
Nota: 1 050 observações não são suficientes para fazer afirmações categóricas sobre a percentagem de movimentações de materiais de cada departamento. O exemplo serve apenas para demonstrar a aplicação matemática deste indicador:
Mão de obra directa na movimentação de materiais = (465,05 / 2 570) × 100 = 18,10%
Para cada departamento, o indicador de mão de obra directa na movimentação de materiais é, portanto, a percentagem de movimentação de materiais dada na coluna 5.
Baseado nos resultados do estudo, verifica-se que o departamento IV deve ser mais estudado e devem ser aplicadas tentativas para reduzir o custo da movimentação de materiais.
Sistemas de informação/Indicadores de desempenho/Indicadores de utilização de recursos: pessoas/Perda de mão de obra directa em movimentações
Para tornar o conceito de perda de mão de obra directa na movimentação de materiais mais prático, foi desenvolvido o indicador de perda de mão de obra directa em movimentações, com base no seguinte quociente (Apple, 1977, p. 432):
Tempo de movimentação de material perdido pela mão de obra directa (h) / Tempo total de mão de obra directa (h)
Sistemas de informação/Indicadores de desempenho/Indicadores de utilização de recursos: equipamentos
Etapas de desenvolvimento - 9 fases | ||||||||
---|---|---|---|---|---|---|---|---|
Início: ![]() |
Básico: ![]() |
Criação: ![]() |
Desenvolvimento: ![]() |
Maturação: ![]() |
Revisão: ![]() |
Desenvolvido: ![]() |
Finalização: ![]() |
Abrangente: ![]() |
Na opinião de John T. Burns, presidente da Sperry Vickers, «O capital para a aquisição de equipamentos pode ser a chave para o aumento da produtividade», sendo este ponto de vista compartilhado por muitos líderes empresariais. Logo, com o aumento do custo da mão de obra e da variedade de equipamentos confiáveis, pode ser utilizada uma grande parte do capital na compra de equipamentos de movimentação de material. Estes equipamentos permitem que o material possa ser movido mais rapidamente, com mais precisão e menos perdas. Além disso, contribuem para uma mais alta e mais profunda armazenagem em corredores mais estreitos e longos. Tanto o material como o equipamento podem ser monitorizados através de um controlo em tempo real.
Apesar da disponibilidade de sistemas de remoção e armazenamento automatizado, automated storage and retrieval systems (AS/RS), carros e tractores com piloto automático, digitalizadores a raio laser controlados por computadores, existe cada vez mais uma necessidade de aumentar significativamente a produtividade usando equipamentos menos sofisticados.
O nível de sofisticação de pessoas e equipamentos necessários depende das necessidades. Portanto, as características e necessidades de cada material, bem como a capacidade da mão de obra disponível, podem indicar a combinação de equipamentos a utilizar.
Entre os factores a serem considerados na selecção de equipamentos de movimentação de material e armazenagem estão os seguintes: características dos materiais, requisitos de movimentação, requisitos da armazenagem, custos e poupanças, salvamento, confiança, manutenção, operação, flexibilidade, adaptabilidade, compatibilidade, expansão, contracção, mobilidade, capacidade, modularidade, segurança, requisitos de controlo, layout, limitações das instalações, gestão de uma atitude de trabalho e prazos de entrega.
A selecção de equipamentos está relacionada com a selecção do vendedor ou fornecedor. No caso do vendedor, a selecção baseia-se numa série de factores relacionados com a selecção de equipamentos, considerando, ainda, a reputação, capacidade de manutenção ou serviço, proximidade e cobertura dada por outras linhas de equipamento (White Jr., 1985, p. 326-327).
Relativamente à utilização de equipamentos, deve-se ter em conta uma série de indicadores de desempenho:
Utilização de equipamento
Percentagem de ocupação
Disponibilidade
Flexibilidade da linha de produção
Flexibilidade do posto de trabalho
Sistemas de informação/Indicadores de desempenho/Indicadores de utilização de recursos: equipamentos/Utilização de equipamento
De acordo com White Jr. (1985, p. 327-328), o indicador de utilização de um equipamento fornece uma indicação da medida em que o equipamento está a ser utilizado em relação ao seu potencial máximo. Saber a utilização do equipamento é essencial para que se possam tomar decisões sobre a necessidade de desenvolver melhores sistemas de movimentação, de modo a aumentar a utilização dos equipamentos.
Na maioria dos casos, o objectivo adequado consiste no aumento da utilização de um equipamento de produção até um valor de pelo menos 90%. Contudo, se a capacidade de produção de uma máquina for muito superior aos requisitos de produção de qualquer ordem de produção individual, são preferíveis produções curtas e setups frequentes, em vez da produção de grandes quantidades de produtos.
Os registos de produção disponíveis e de preferência precisos, estudos de amostragem de trabalho ou estudos de tempos podem determinar a utilização de equipamentos. Este indicador deve de ser utilizado para determinar se as medidas adicionais para aumentar a produção se justificam.
Portanto, o indicador de utilização do equipamento de produção é dado por:
Utilização do equipamento de produção = (Produção real / Capacidade teórica)
Sistemas de informação/Indicadores de desempenho/Indicadores de utilização de recursos: equipamentos/Percentagem de ocupação
Segundo White Jr. (1985, p. 328-330), uma das avaliações difíceis é determinar a utilização de equipamentos de movimentação de material. Estes podem ser de diferentes tipos, consoante a função a que se destinam. Por exemplo, as gruas e os guindastes são usados para diferentes fins sendo, portanto, apropriado o uso de diferentes medidas de desempenho.
A carga total também é definida de diversas formas, em alguns casos a capacidade de carga pode ser determinada pelo peso da carga, e em outros casos é determinada pelo seu tamanho.
A utilização dos equipamentos de movimentação pode ser obtida por amostragem de trabalho. Através da recolha de observações aleatórias do equipamento, pode ser determinado, não só o seu estado de ocupação ou ociosidade, como também a percentagem de utilização da sua capacidade de carga, no momento da observação. A capacidade de carga é uma função do peso e da velocidade.
A medida de utilização de equipamentos de movimentação permite saber se estes se encontram sobre ou subutilizados. Considera-se que um equipamento de movimentação se encontra ocupado se estiver a ser carregado, descarregado ou em movimento, com ou sem carga. A percentagem de tempo em que o equipamento de movimentação está ocupado designa-se por percentagem de ocupação.
Enquanto que para os equipamentos de produção é desejável maximizar a sua utilização, o mesmo não se pode dizer para algumas classes de equipamentos de movimentação, por exemplo empilhadoras e gruas, em que são preferíveis percentagens de ocupação reduzidas. A explicação para esta diferença deve-se, sobretudo, ao facto dos equipamentos de movimentação de materiais serem normalmente usados para prestar serviços. A necessidade de equipamentos de movimentação é, normalmente, aleatória e os tempos necessários para executar um serviço de movimentação também são, muitas vezes, aleatórios. Num ambiente essencialmente aleatório, conforme aumenta a percentagem de ocupação, o número de cargas à espera de serem movimentadas aumenta exponencialmente. Mediante tais condições, considera-se razoável uma percentagem de ocupação que corresponda a um valor entre 65 e 75%.
Como tal se não existir um ambiente aleatório, é provável que possam ser usados tractores/reboques ou transportadores e veículos sem condutor, em vez de empilhadores
Considere-se o exemplo de uma empilhadora, em que foi realizado um estudo de amostragem de trabalho. Das 25 observações recolhidas, 4 representavam o estado de ociosidade da empilhadora.
A percentagem de ocupação de empilhadora calculou-se, então, da seguinte forma:
Percentagem de ocupação = (Número de observações em que o equipamento está ocupado / Número total de observações) × 100 = (21 / 25) × 100 = 84%
Sistemas de informação/Indicadores de desempenho/Indicadores de utilização de recursos: equipamentos/Disponibilidade
A disponibilidade é a percentagem de tempo em que um equipamento está disponível para exercer a sua função, excluindo o tempo em que esteve parado para manutenção ou por outro motivo qualquer. Este indicador apresenta algumas dificuldades no que diz respeito ao que deve ou não ser considerado na sua determinação, pois envolve directamente áreas que utilizam equipamentos com vista à obtenção de benefícios, ou seja, áreas de produção.
Uma vez que a área de produção apresenta objectivos que devem ser cumpridos num determinado período de tempo, qualquer contratempo relacionado com os equipamentos serve de justificação para o facto de essas metas não serem atingidas. Independentemente de o equipamento ter estado parado para manutenção ou devido a uma avaria, considera-se que a sua inactividade pode gerar prejuízo para a organização em causa.
Relativamente à determinação da disponibilidade, são diversas as formas de cálculo e os raciocínios usados nas diversas áreas que constituem uma empresa. Apesar dos diferentes interesses envolvidos, deve haver um consenso entre todas as áreas, tendo em conta que qualquer uma pretende ter os equipamentos disponíveis para funcionar 24 horas por dia, de modo a contribuir com a obtenção de lucros para a empresa. Portanto, todos os factores que impossibilitem o funcionamento dos equipamentos, independentemente da área responsável, devem ser considerados no cálculo deste indicador, tendo em conta que os accionistas da empresa que investem num equipamento não o querem ver parado.
Tendo em conta os diferentes métodos usados no cálculo da disponibilidade, algumas empresas consideram que os equipamentos devem ter um calendário de funcionamento baseado no calendário da empresa, para que todas as intervenções que ocorram dentro desse horário possam ser consideradas como tempo indisponível. Em contrapartida, outras empresas incluem o tempo em que os equipamentos estiveram parados para manutenção no cálculo deste indicador. Por outro lado, existem empresas que acham que os equipamentos devem estar disponíveis 24 horas por dia, independentemente do horário de trabalho da organização, mas incluem determinadas intervenções da área de produção, como por exemplo troca de turnos, tempos de setup e falta de material, no cálculo da disponibilidade (JC, 2008).
Pode definir-se o cálculo do indicador de disponibilidade de um equipamento da seguinte forma (Chiaradia, 2004):
Disponibilidade (%) = ((Tempo útil de trabalho - Tempo de paragens não programadas) / Tempo útil de trabalho) × 100
Em que o tempo útil de trabalho representa a diferença entre o tempo total disponível de trabalho do equipamento e o tempo de paragens programadas pela produção, como por exemplo: tempo de descanso, limpeza do equipamento, manutenções programadas, entre outros.
Sistemas de informação/Indicadores de desempenho/Indicadores de utilização de recursos: equipamentos/Flexibilidade da linha de produção
O indicador de flexibilidade da linha de produção é satisfatoriamente usado como uma medida de flexibilidade dum equipamento numa linha de produção, em relação ao fluxo duma peça. Este pode calcular-se da seguinte forma:
Indicador de flexibilidade da linha de produção = a / b
Em que:
a = Número de máquinas ou postos de trabalho a realizarem operações na peça em consideração, concebidas/os de maneira a poderem ser deslocadas/os para um novo local na mesma linha de produção, num turno de trabalho;
b = Número total de máquinas ou postos de trabalho a realizarem operações na peça em consideração, na linha de produção.
Neste contexto, uma máquina representa qualquer dispositivo imóvel com uma fonte de energia separada ou individual (Apple, 1977, p. 430-431).
Sistemas de informação/Indicadores de desempenho/Indicadores de utilização de recursos: equipamentos/Flexibilidade do posto de trabalho
O indicador de flexibilidade do posto de trabalho é uma medida muito utilizada na organização de máquinas e postos de trabalho, tendo em conta a utilização de homens e máquinas. Este pode calcular-se com base no seguinte quociente:
Indicador de flexibilidade do posto de trabalho = c / d
Sendo:
c = Número de máquinas ou postos de trabalho dentro da área em questão, concebidas/os de maneira a poderem ser deslocadas/os para qualquer outro local, num turno de trabalho;
d = Número total de máquinas ou postos de trabalho dentro da área em questão.
Neste caso, um posto de trabalho abrange toda a área coberta pelas ferramentas, equipamentos, máquinas e materiais em vias de fabrico, necessários para o desempenho de uma determinada operação (Apple, 1977, p. 430-431).
Sistemas de informação/Indicadores de desempenho/Indicadores de controlo de gestão: movimento
Etapas de desenvolvimento - 9 fases | ||||||||
---|---|---|---|---|---|---|---|---|
Início: ![]() |
Básico: ![]() |
Criação: ![]() |
Desenvolvimento: ![]() |
Maturação: ![]() |
Revisão: ![]() |
Desenvolvido: ![]() |
Finalização: ![]() |
Abrangente: ![]() |
De acordo com White Jr. (1985, p. 342-343), todo o controlo de movimento, fluxo e taxa de transferência está relacionado com o controlo do movimento de materiais, pessoas e equipamentos. A função primária da movimentação de materiais é mover materiais, tendo em conta que deve ser feito de uma forma organizada. O movimento por si só não é produtivo, portanto, para outras funções serem produtivas, os materiais devem ser movidos para o lugar certo à hora certa.
No controlo do movimento de material a preocupação será a precisão, pontualidade, velocidade, distância, tamanho e o número de movimentos realizados. Um movimento é necessário se a quantidade certa de material for entregue no lugar certo, sendo oportuno se chegar à hora certa. A eficiência das operações é uma função da razão da velocidade do movimento, da distância percorrida, do tamanho da carga e do número de movimentos necessários para prestar o serviço solicitado.
Do ponto de vista da medição da produtividade, é necessário que as medidas de controlo sejam significativas, facilmente compreensíveis e simples de calcular e utilizar. Por outro lado, estas devem exigir a entrada de dados que estejam imediatamente disponíveis. Relativamente ao controlo de movimento existem, frequentemente, sistemas de manutenção de registos que geram bilhetes de movimento, registos de viagem, etc., e fornecem um feedback sobre o desempenho do movimento. Para tais dados serem usados num programa de medição da produtividade, os registos também devem ser precisos.
Actualmente, a enorme variedade de equipamentos de movimentação de materiais disponíveis possibilita várias formas de movimentar material. Ao escolher, a pessoa pode deslocar-se para o local de armazenamento, ou então, o material armazenado pode ser movimentado até à pessoa. Enquanto que no primeiro caso é a pessoa que se desloca, no outro são os materiais que são movimentados. Como exemplos da deslocação de pessoas podem considerar-se order-picker trucks, walking, e aisle-captive, man-aboard storage/retieval (S/R) machines. Em contrapartida, a movimentação de materiais apresenta outras aplicações práticas, como por exemplo mini load S/R systems e S/R carousel conveyors.
Existem diversas medidas para controlar a movimentação de materiais, entre as quais o indicador de utilização de equipamentos de movimentação (pode ser encontrado em White Jr. (1985, p. 329)) e o índice de desempenho da taxa de transferência (pode ser encontrado em White Jr. (1985, p. 354)), ambos referentes ao movimento dos equipamentos de movimentação.
As duas medidas adicionais utilizadas no controlo da movimentação de materiais, baseadas no fluxo de material que se move através dos sistemas, são o:
Movimento por operação; e a
- Distância média por movimento
Sistemas de informação/Indicadores de desempenho/Indicadores de controlo de gestão: movimento/Movimento por operação
Segundo White Jr. (1985, p. 342-343), o indicador de movimento por operação mede a eficiência relativa do plano global de movimentação, centrando-se no número de movimentos, ao invés de como eles são executados. O material é acompanhado desde que chega à doca de recepção até que deixa a doca de expedição. O número de vezes em que o material é levantado e pousado é gravado e comparado com o número de vezes em que uma operação produtiva é realizada no material. No entanto, a atenção deve centrar-se no número de vezes em que o material é movimentado nos postos de trabalho e nas máquinas, durante o seu processo de fabrico.
Os movimentos são dispendiosos, não só porque consomem tempo e energia e requerem pessoas, equipamento e espaço, mas também porque aumentam a probabilidade de perda. Ao eliminar operações, simplificando e alterando a sua sequência, pode reduzir-se esse número de movimentos.
As interfaces entre as funções não são, tipicamente, bem planeadas. Em particular, as interfaces entre recepção e inspecção, inspecção e armazenamento, armazenamento e produção, fases de produção, produção e montagem, montagem e acondicionamento, acondicionamento e entreposto, entreposto e embalagem e embalagem e transporte, devem ser examinadas de perto para se determinar o número de vezes em que o material é movimentado.
O desenvolvimento de um diagrama de fluxo de processos de uma operação é uma ferramenta muito usada na melhoria de métodos de estudo. Esse diagrama retrata as operações, inspecções, atrasos, armazenamentos e movimentos ou transportes necessários para processar material através dum processo de produção. Logo, se os diagramas de fluxo de processos forem preparados antecipadamente, podem facilitar o cálculo do indicador de movimento por operação, através da seguinte fórmula:
Indicador de movimento por operação = Número total de movimentos / Número total de operações produtivas
Pode ser encontrado um exemplo do cálculo do indicador de movimento por operação em White Jr. (1985, p. 344-345).
Sistemas de informação/Distância média por movimento
Logística/Sistemas de informação/Distância média por movimento
Gestão do aprovisionamento
Etapas de desenvolvimento - 9 fases | ||||||||
---|---|---|---|---|---|---|---|---|
Início: ![]() |
Básico: ![]() |
Criação: ![]() |
Desenvolvimento: ![]() |
Maturação: ![]() |
Revisão: ![]() |
Desenvolvido: ![]() |
Finalização: ![]() |
Abrangente: ![]() |
Funções do aprovisionamento
Gestão de fornecedores
- Âmbito
- Processo de fornecimento
- Abordagens actuais
- Organização do aprovisionamento
- Abordagem estratégica
Integração das decisões de aprovisionamento e transporte
- Condições do frete FOB
- Intervenção do aprovisionamento nas actividades de transporte
- Factores de decisão na selecção do modo de transporte e transportador
- Organização para tomada de decisões sobre o transporte
- Integração contínua
Questões ambientais do aprovisionamento
Gestão do aprovisionamento/Funções do aprovisionamento
Funções do aprovisionamento
A importância do aprovisionamento
Em norma, as empresas negligenciam os custos do aprovisionamento devido à sua complexidade. Todos os processos inerentes a uma empresa como o marketing, produção e vendas são aspectos que exigem muita atenção e tiram ênfase ao aprovisionamento. Isto é de certa forma errado visto que os serviços e os materiais comprados representam 25 a 40 porcento do valor de venda do produto final. Uma área de custos tão grande não pode ser assim negligenciada.(Riggs, Robbins, 1997, p. 8)
Nos anos 30, o departamento de teoria laborais de Adam Smith criou uma maneira de organizar trabalho por funções para aumentar a eficiência dos operários. Esta organização criou o departamento da procura que foi concebido para aumentar a eficiência de uma empresa em 3 áreas:
- Compra de materiais e serviços;
- Eficiência dos operários por tarefa;
- Beneficiar de compras em larga escala.(Riggs, Robbins, 1997, p. 9)
O departamento do aprovisionamento teria uma equipe de pessoas para realizar as tarefas de compra como:
- Produzir ordens de compra;
- Planejar e receber materiais;
- Selecionar fornecedores;
- Negociação de termos;
- Pagamento de contas;
- Desenvolvimento de contratos. (Riggs, Robbins, 1997, p. 10)
Este método funcionou bem até aos anos 70, mas nesta década surgiu o conceito do indivíduo e o poder das equipas. Estes dois novos conceitos organizacionais mudaram a organização de vários aspectos na empresa como a contabilidade, serviços de informação e o próprio aprovisionamento. Estes novos conceitos nas antigas estruturas desequilibrou as organizações.(Riggs, Robbins, 1997, p. 9-10)
À medida que os indivíduos começaram a especificar mais e mais fornecedores, os departamentos responsáveis pela compra ficaram com a responsabilidade primária de processar ordens. Toda a atenção estava agora centrada em satisfazer as necessidades do indivíduo ou da equipa e perdeu-se foco em aspectos do aprovisionamento como a selecção de fornecedores, processo de compra e decisão de compra. Resumindo, a compra deixou de ser um acto administrativo favorável em demasiados negócios. Como resultado, grande parte dos negócios enfrentavam agora uma nova serie de problemas:
- A proliferação de fornecedores;
- Uma explosão de compras de baixo custo, resultando pouco tempo para estratégicas oportunidades de compra do lado dos fornecedores;
- Diversidade de fornecedores do mesmo produto com as mesmas características;
- A compra passou a ser um simples negócio transaccional sem qualquer gestão.(Riggs, Robbins, 1997, p. 11-12)
Estes problemas resultaram em custos adicionais ocultos. As milhares de compras a baixo custo, exigidas pelos indivíduos ou equipas, representavam no total entre 40 a 60% do valor das vendas. Estes custos ocultos e indirectos dariam azo a:
- Custos não competitivos para estas despesas;
- Altos custos de transacção;
- Negligência em tarefas administrativas como recepção de bens e auditorias.(Riggs, Robbins, 1997, p. 12)
O problema com tudo isto é a maximização do valor do dinheiro gasto em compras que foi esquecido. Na situação actual, onde todas as empresas procuram a maior redução de custos possível, o departamento de aprovisionamento não pode ser esquecido. O Aprovisionamento tem simples conceitos e ferramentas para reavaliar o comportamento de uma empresa na altura das compras. (Riggs, Robbins, 1997, p. 13)
O aprovisionamento na actualidade
Visto a necessidade emergente de evoluir o departamento do aprovisionamento, as empresas começaram a procurar hipóteses e opções para melhorar o desempenho do aprovisionamento. A gestão do aprovisionamento ganhou uma nova denominação:
- Gestão do aprovisionamento - metodologia usada para examinar todas as facetas da compra e do uso dos materiais e serviços comprados. Processo designado para maximizar o valor do dinheiro investido em materiais e serviços comprados. É um processo que visa criar estratégias para gerir a procura e o uso dos materiais e serviços. (Riggs, Robbins, 1997, p. 49)
São vários os aspectos que podem ser melhorados no aprovisionamento:
- O tempo de ciclo para compras;
- O tempo de ciclo para implementação de melhorias;
- Pessoal fora do departamento que realiza funções indirectas relacionadas com a compra;
- Pouca dedicação à procura de boas localizações para melhoria do fornecimento;
- Falta de foco na inovação;
- Falta de preocupação em encontrar fornecedores chave para satisfazer clientes chave de modo a descobrir bons negócios. (Riggs, Robbins, 1997, p. 14)
Na actualidade, os mercados estão em constante mudança. Os preços variam diariamente e, para todos os negócios, é necessário a empresa conseguir manter-se competitiva para conseguir manter, ou até mesmo, atingir o sucesso. É então essencial ter em conta o tempo quando estudamos o aprovisionamento de uma empresa. O tempo de implementação de novas estruturas, a inovação e a melhoria têm de ser rápidas. Já há muito tempo que o aprovisionamento deixou de ser apenas uma compra de um material e tentar pagar a dívida. Agora é uma questão de descobrir como é que os fornecedores nos conseguem inserir mais rapidamente no mercado e como é que a empresa consegue melhorar quando aí chegarmos. (Riggs, Robbins, 1997, p. 33-35)
É importante a criação de pontes entre os fornecedores e os clientes. A ausência desta ponte inibe a possibilidade de o cliente melhorar a eficácia do seu negócio. Um bom cliente com um bom negócio é fundamental para qualquer empresa.
Compradores tradicionais | Gestores de aprovisionamento |
---|---|
|
|
Tabela 1: Problemas relacionados com a compra. (Riggs, Robbins, 1997, p. 41)
Cada aprovisionamento e serviço requerem uma estratégia bem definida para a sua compra e uso. O novo papel do gestor do aprovisionamento é aceder ao mercado através de uma rede de bons fornecedores que:
- Satisfaçam todos os requisitos e benefícios;
- Tenham a melhor tecnologia, as melhores pratica e os melhores processos;
- Tenham as melhores estruturas de custos;
- Estejam actualizados com o mercado.
O gestor do aprovisionamento e o fornecedor criam uma estratégia para implementar um melhor sistema de entrega que inclua as melhores práticas para o uso e todos os processos de suporte e transacções.
O aprovisionamento gere todas as compras e serviços para reduzir custos e foca os fornecedores em melhorarias na qualidade, consistência e uso. (Riggs, Robbins, 1997, p. 50-52)
Tarefas do aprovisionamento
O aprovisionamento tem com principal propósito optimizar o valor final de um produto para o cliente. A gestão do aprovisionamento tem como objectivo:
- Identificar os melhores fornecedores;
- Analisar todas as indústrias relacionadas e as relações custo/uso;
- Revelar o custo da compra, recibo, inventário e pagamento;
- Determinar o impacto na utilidade e tempo gasto de operários;
- Relacionar o valor dos materiais e serviços com as necessidades e uso do cliente.
(Riggs, Robbins, 1997, p. 53-54)
A eficácia do aprovisionamento é medido em várias dimensões e não apenas no custo do material ou da aquisição. Entra em conta:
- O custo total, incluindo o custo da unidade, do inventario, descontos e impostos;
- Custos de utilização, gastos e qualidade;
- Custos do processo de compra;
- Tempo de ciclo entre o fornecedor e o cliente.
(Riggs, Robbins, 1997, p. 54-55)
Processo de Procura | Processo de melhoria contínua | Processo de inovação | |
---|---|---|---|
Conceitos chave |
|
|
|
Efeitos |
|
|
|
Benefícios |
|
|
|
Tabela 2: Processos base da gestão do aprovisionamento (Riggs, Robbins, 1997, p. 56)
A incerteza existente no meio industrial torna as decisões de aprovisionamento cada vez mais importantes, em particular para as matérias primas e componentes mais complexas e estratégicas. Os efeitos da decisão de compra a longo prazo são também um factor preocupante, perigoso e importante. O aprovisionamento de matéria prima ou componentes é caracterizado por:
- Incerteza no fornecimento;
- Dependência de fontes de "commodities" no estrangeiro;
- Tempos de entrega longos e variáveis;
- Falta de fontes de energia, ou aumentos no seu preço;
- Regulamentação governamental;
- Aumento da competição em termos globais.
Este ambiente em mudança contínua torna necessário que o aprovisionamento seja mais efectivo na sua tarefa de pesquisa no mercado de abastecimento. As condições existentes no mercado de abastecimento, como os preços, as condições de pagamento, os tempos de entrega e a disponibilidade, devem ser transmitidas às outras áreas da organização. Esta informação é vital para a formulação de decisões estratégicas e de decisões operacionais. (Arantes, 2005)
Matérias primas e componentes críticas devem ser identificadas, e planos de contingência devem ser elaborados para garantir a produção continua e a qualidade.O planeamento estratégico do Aprovisionamento passa então por:
- Identificação do aprovisionamento crítico - componentes com tecnologia proprietária, limitações de capacidade do fornecedor, existência de poucos fornecedores, disponibilidade de MP ao nível do fornecedor, componentes de elevado valor-incorporado, etc.;
- Aferição do risco - verificar a probabilidade de ocorrência do cenário mais pessimista e do mais optimista, e verificar o desempenho da organização nesses cenários;
- Desenvolvimento e implementação de uma estratégia - de modo a garantir que o abastecimento se dê sem interrupções e de uma forma que minimize o custo total, satisfazendo as necessidades determinadas.
O departamento de aprovisionamento não acrescenta valor ao produto final. É um custo necessário, pelo que deve este ser minimizado num perspectiva de custo total. OS custos que podem ser reduzidos são:
- Custos administrativos;
- Preço de aquisição;
- Custos de posse de existências;
- Balanceamento de volumes;
- Estabelecimento de relações a longo prazo com fornecedores.
Gestão do aprovisionamento/Gestão de fornecedores
Gestão de Fornecedores
Introdução
Na escolha dos fornecedores é necessário ter em atenção as necessidades e requisitos do cliente. O fornecedor mais competitivo tende a ter as seguintes características:
- Baixos custos de produção devido a inovação da produção e infraestruturas;
- Têm um bom controle de custos com processos de qualidade e cartas de controle de produção;
- Constante inovação e boa tecnologia com uma boa rede de aprovisionamento;
- São normalmente os primeiros a chegar ao mercado com novos e inovadores produtos.
A análise de indústrias e mercados permite encontrar os melhores fornecedores, não só pelo valor do material/serviço, mas também pelo potencial do fornecedor para a inovação da empresa. Essa inovação atinge-se por se criar uma ligação entre o fornecedor e o cliente, onde há uma procura pelo fornecedor que melhor corresponda às necessidades e requisitos do cliente. Há também uma procura pelo fornecedor inovador, que forneça materiais propícios à criação de novos produtos para a empresa poder estar sempre atualizada e na vanguarda. É também dado ênfase à capacidade burocrática do fornecedor e o seu sistema de transporte.
No final de toda a ponderação, será escolhido o fornecedor que obtenha a melhor classificação geral, de acordo com as necessidades da empresa, nos seguintes aspectos:
- Competitividade tecnológica;
- Menores custos;
- Boa posição no mercado e que controle a estrutura de custos;
- Rede de transportes.
(Riggs, Robbins, 1997, p. 59-60)
Sendo assim, o aprovisionamento tem com principal propósito optimizar o valor final de um produto para o cliente. No âmbito da gestão do aprovisionamento, a procura é definida pela pesquisa de fontes de fornecedoras que preencham todos os requisitos da entidade a aprovisionar. Esta processo terá três passos fundamentais:
- Pesquisa de fontes fornecedoras;
- Classificação das fontes fornecedoras;
- Seleção da fonte fornecedora.
Pesquisa de fontes fornecedoras
Existem fatores que delimitam a pesquisa de fornecedores. A busca de fornecedores pode ser mais abrangente ou mais contida dependendo:
- Das características do aprovisionamento - Estas características referem-se ao tipo de compra que irá ser efetuada. Poderá ser uma primeira compra, uma compra repetida ou até uma modificação das especificações da compra;
- Das exigências do cliente - A pesquisa de fornecedores terá de ter uma postura mais ou menos seletiva de acordo com as exigências do cliente em relação à qualidade do produto final;
- Do tempo da pesquisa - Terá de ser feita uma análise para se apurar quais as complicações relativamente ao tempo da pesquisa de novos fornecedores e o tempo de recorrer aos fornecedores habituais e, após essa análise, apurar os limites da pesquisa de novos fornecedores. (Sapo, 2004)
Classificação e seleção das fontes fornecedoras
A classificação dos fornecedores localizados na pesquisa terá em conta a localização e dimensão do fornecedor e as características especificadas pelo produtor, intermediário ou cliente. Esta classificação tem como objetivo avaliar aspectos específicos do fornecedor. (Sapo, 2004)
Normalmente, as categorias de aprovisionamento para a classificação são:
- Componentes;
- Matérias-primas;
- Matérias operacionais (consumíveis);
- Equipamento de apoio,
- Equipamento do processo;
- Serviços.
Após a classificação ser realizada, a avaliação do fornecedor segue uma hierarquia de especificações dadas pela empresa a ser aprovisionada. As especificações estão relacionadas com o preço, qualidade e entrega. A hierarquia de especificações exigida pelo cliente e a classificação dada aos fornecedores dão informações sólidas ao comprador na escolha da fonte abastecedora.
O comprador poderá avaliar e escolher o fornecedor com:
- Uma pontuação objectiva, onde seguirá a classificação e a hierarquia e escolher sem ponderações a fonte de aprovisionamento;
- Uma pontuação subjectiva, em que o comprador evitará erros de apreciação na classificação;
- Uma pontuação quantitativa, utilizando uma check list com as especificações do comprador ou números-índice de modo a medir o desenvolvimento do fornecedor.
Esta classificação e avaliação é extremamente importante e objectiva em relação às exigências do cliente, mas devemos sempre atender outros factores externos, como o tipo de fornecimento (simples ou múltiplo), as relações entre o comprador, o cliente e o fornecedor, a dimensão, expansibilidade e desenvolvimento das fontes de aprovisionamento. (Sapo, 2004)
Outro importante assunto no que trata selecionar uma fonte de aprovisionamento, é qual o número ideal de fornecedores. A resposta está no balanceamento entre os efeitos no custo total da compra e na segurança dos fornecimentos. No que toca a custos, escolher vários fornecedores poderá baixar o preço da aquisição, mas em contrapartida poderá aumentar outros custos como o transporte, e impossibilitaria a hipótese de desconto sobre grandes volumes. No entanto a segurança no fornecimento estará garantida, visto que a empresa a aprovisionar não estará dependente apenas de um fornecedor, assegurando assim o aprovisionamento.
No entanto, recorrer a uma única fonte abastecedora é por vezes a única solução. Em certos casos onde a empresa necessita de produtos com tecnologia complexa ou patenteados, a reputação do fornecedor é favorável ou quando o cliente exige um determinado fornecedor, o comprador ver-se-à obrigado a recorrer a um único fornecedor. O problema estará na falta de segurança no aprovisionamento e o facto de as quantidades exigidas pelo comprador não poderem ser altas, aumentando em certos casos o preço do produto a adquirir. (Sapo, 2004)
Total quality management
O preço é um fator bastante importante, mas também o é a qualidade. Atualmente, para muitos clientes, a qualidade é um fator altamente importante. O preço da aquisição não representa o custo total do produto, apenas uma parte do custo total onde se inserem outros custos como a maquinação, rupturas, tempos mortos, operações extra, etc.. O nível de qualidade deverá ser previamente calculado para as especificações poderem ser enviadas ao fornecedor. A qualidade dos materiais é da responsabilidade do departamento de aprovisionamento. (Arantes, 2005)
Just In Time
Just in time, JIT, é uma filosofia de fazer negócios. Visa a identificação e a eliminação de desperdícios ao longo do sistema produtivo. Sendo assim, o processo de melhoria contínua é facilmente aplicável com esta filosofia, tornando-se até, a parte central de toda a gestão. A implementação do JIT serve para produzir para uma procura conhecida, denomina-se a esta prática de "pull" de produção. JIT traz certos benefícios como:
- Redução de existências;
- Redução de tempos de produção;
- Aumento da qualidade dos produtos;
- Redução do espaço necessário para a produção do produto final.
Por sua vez, o sistema JIT está também muito dependente da qualidade e serviço do fornecedor. O esforço na redução de desperdícios inclui o fornecedor em toda a cadeia de abastecimento. Este sistema dificulta a escolha do fornecedor devido a complicações inerentes, tais como:
- Falta de cooperação por parte dos fornecedores;
- A qualidade deixa de ser inspecionada, e passa a ser estatística, daí a elevada importância de um fornecedor com boa qualidade de serviço e materiais;
- Os fornecedores têm de mostrar cartas de controlo de produção para prevenção de possíveis contratempos;
- As relações tem de ser cooperativas e coordenadas.
A seleção do fornecedor passa a ter em conta métodos de controlo de qualidade, proximidade física do fornecedor, flexibilidade e consistência no tempo de resposta.
A implementação de um ambiente JIT é facilitado pela existência de um único plano mestre de produção. Este é enviado ao fornecedor de modo a saber quais as componentes necessárias.
Um acordo de fornecimento JIT não permite variabilidade. A quantidade que o cliente espera será a quantidade exata que vai receber. Por esse motivo a existência de um contrato é necessário, poupando tempo em negociações e garantindo que a linha não pára! (Arantes, 2005)
Negociação
Na negociação trata-se de todos os aspectos burocráticos inerentes à aquisição. Neste processo iremos averiguar:
- O que se negocia;
- Como se negocia;
- Curvas de aprendizagem.
Por negociação entende-se qualquer forma de comunicação através da qual os participantes procuram explorar as sua forças relativas com vista a atingir fins específicos. Na área de aprovisionamentos o “que se negocia” não é mais do que um conjunto de tópicos relacionados com a compra:
- Modificação do preço;
- Processo de fixação dos preços;
- Descontos (quantidade, revenda ou financeiros);
- Condições de pagamento;
- Custos e condições de transporte;
- Alteração de datas ou de especificações;
- Acondicionamento, embalagem e distribuição;
- Fornecimento de amostras;
- Indemnizações, etc.
Como se negocia
A negociação compreende, geralmente, três fases: pré-negociação, negociação propriamente dita e pós-negociação. A pré-negociação compreende todas as ações preliminares à negociação propriamente dita, designadamente:
- Determinação de quem vai negociar;
- Local da negociação (se aplicável);
- Recolha de informações;
- Fixação de objetivos;
- Alinhamento de tácticas e estratégias.
Para a negociação propriamente dita, algumas técnicas podem ser utilizadas, tais como:
- Colocação de assuntos mais controversos no final da agenda, após obtenção de acordo em matérias mais consensuais;
- Utilização da informação a disponibilizar como meio de pressão sobre a parte contrária;
- Flexibilidade para efetuar concessões, ceder certas condições para ganhar outras, tenho em conta o custo de oportunidade.
A curva de aprendizagem ilustra o fenômeno da redução de horas de produção acumuladas à medida que aumenta o número de unidades produzidas (redução da hora de trabalho por unidade produzida).
A utilização das curvas de aprendizagem no processo de negociação pode ser importante (prazos de entrega e custo global de encomendas), sendo de evitar nos seguintes casos:
- Sempre que a aprendizagem não for constante;
- Sempre que a relação custo/volume não se afigure significativa face ao custo de análise da curva de aprendizagem.
Parcerias
Parcerias podem ser eficazes, eficientes e lucrativas em certos casos. Recorrer a uma pareceria depende de vários factores como a procura do cliente, consistência no fornecimento, continuidade na entrega e a posição do fornecedor no mercado. Uma parceria é um relacionamento de negócio feito à medida, baseado na confiança mútua, na partilha do risco e na partilha do valor gerado que resulta numa vantagem competitiva. Esta cooperação pode levar a resultados significativos devido a um melhor desempenho pelas duas empresas juntas. Este desempenho será superior ao obtido pelas firmas individualmente. (Arantes, 2005)
As parcerias com os fornecedores surgem devido a vários factores como:
- As pressões existentes:
- Ciclos de vida dos produtos cada vez mais curtos;
- Competição globalizada;
- Complexidade dos mercados;
As organizações, cada vez mais, não se aventuram sozinhas, o risco de se atrasarem perante o mercado é tão grande e perigoso, que uma boa parceria pode beneficiar ambos os lados. (Arantes, 2005)
Tipos de relacionamento
Existem vários tipos de relacionamento entre a empresa e o fornecedor. Dependendo da posição do fornecedor ou da empresa no mercado, das funções de cada uma, marketing, etc., as parcerias têm condições específicas:
- Transacional - pode ir de transações esporádicas até transações correntes, mas no entanto, não existe compromisso entre as organizações em termos de operação ou fornecimento de produtos específicos;
- Parceria tipo I - de curto prazo, as organizações coordenam minimamente as suas operações, geralmente apenas ao nível de uma área funcional apenas;
- Parceria tipo II - passagem da coordenação à integração de atividades. Existe mais do que uma área envolvida e, embora não seja vitalício,
são de longo prazo;
- Parceria tipo III - o nível de integração já é bastante elevado. Cada parte vê a outra parte como uma extensão da sua própria organização e não existe data para o fim da parceria;
- Joint Venture - há partilha da posse, o projeto é desenvolvido conjuntamente e pertence a ambos, mas as empresas continuam entidades separadas;
- Integração vertical - a montante ou a jusante, passa pela aquisição de um pelo outro. (Arantes, 2005)
Gestão do aprovisionamento/Gestão de fornecedores/Introdução
Logística/Gestão do aprovisionamento/Gestão de fornecedores/Introdução
Gestão do aprovisionamento/Gestão de fornecedores/Âmbito
Logística/Gestão do aprovisionamento/Gestão de fornecedores/Âmbito
Gestão do aprovisionamento/Gestão de fornecedores/Processo de fornecimento
Logística/Gestão do aprovisionamento/Gestão de fornecedores/Processo de fornecimento
Gestão do aprovisionamento/Gestão de fornecedores/Abordagens actuais
Logística/Gestão do aprovisionamento/Gestão de fornecedores/Abordagens actuais
Gestão do aprovisionamento/Gestão de fornecedores/Organização do aprovisionamento
Logística/Gestão do aprovisionamento/Gestão de fornecedores/Organização do aprovisionamento
Gestão do aprovisionamento/Gestão de fornecedores/Abordagem estratégica
Logística/Gestão do aprovisionamento/Gestão de fornecedores/Abordagem estratégica
Gestão do aprovisionamento/Integração das decisões de aprovisionamento e transporte
Integração das decisões de aprovisionamento e transporte
Introdução
Uma boa gestão de transportes é essencial para um aprovisionamento eficaz, eficiente e lucrativo. Tanto o transporte inbound, dos fornecedores, como o outbound, para os clientes, têm um impacto significativo nos custos, na qualidade e no serviço. É então bastante importante uma boa rede de transportes no aprovisionamento. (Logistics Bureau, 2003)
Tamanho da rede de transportes
É necessário determinar os requisitos óptimos para a rede de transportes, quer para o transporte do fornecedor, quer para o transporte para o cliente.
Os aspectos chave deste processo incluem:
- Quantificar a função do transporte;
- Calcular a quantidade de equipamento necessário para a realização do processo;
- Construção de modelos de capacidade e de utilização;
- Desenvolvimento detalhado dos modelos de custos, incluindo custo com o equipamento, trabalho, combustível, manutenção, etc.;
- Descobrir e avaliar opções relativas ao custo/benefícios e analisar os riscos. (Logistics Bureau, 2003)
Mapeamento da rede de transportes
O bom mapeamento é essencial para manter a qualidade do produto, para realizar um bom serviço e para controlar custos. O mapeamento da rede de transportes é ainda mais importante no caso de a viagem não for directa, viagem apenas entre fornecedor e empresa. No caso de a rede ter de passar por vários pontos, este é um aspecto fundamental na gestão dos transportes para o aprovisionamento. (Logistics Bureau, 2003)
Para assegurar que a frota é usada da maneira mais eficaz possível é necessário a realização continua de análises detalhadas através de testes à rota planeada e criação de diferentes cenários de entrega para avaliar hipóteses. (Logistics Bureau, 2003)
Esta análise à rota pode ser usada para testar factores como:
- O impacto da localização do cliente;
- O impacto da incerteza nos tempos de entrega;
- O impacto da necessidade de alteração do tipo e tamanho dos veículos na utilização e no custo;
- O impacto da estrutura de turnos dos condutores;
Opções de aquisição de uma rede de transportes
Por vezes, consoante a utilização dada à rede de transportes, a dinâmica do negócio, e à função da frota, um teste à opção de adquirir uma rede de transportes pode ser uma hipótese a considerar. Uma frota própria, híbrida ou mesmo adquirida por outsourcing pode ser a solução. Numa situação onde a tarefa de uma rede de transportes é já rotineira, com uma procura constante e com grande utilização, uma frota própria poderá trazer algumas vantagens. Considerando uma procura muito variável em termos de volume e de ponto de entrega, pode entrar em conta uma frota outsourcing. (Logistics Bureau, 2003)
Condições de frete
O frete visa o valor a pagar pelo serviço de distribuição de uma mercadoria. . Existem dois tipos de frete
- Frete FOB, a abreviatura da frase inglesa “Free On Board” que significa “Posto a Bordo”;
- CIF, a abreviatura da expressão inglesa “Cost, Insurance and Freight” que significa “Custo, Seguro e Frete”.
Na modalidade FOB, o remetente da mercadoria (exportador) é responsável pelos custos de transporte e seguro da carga apenas até esta ser embarcada. O comprador (importador) torna-se responsável pelo pagamento do transporte e do seguro a partir daí. Mais especificamente, o processo funciona da seguinte maneira: o exportador mantém sua responsabilidade pela mercadoria até esta entrar no navio no qual será levada até o porto de destino. Ao entrar no navio, todos os custos (seguro, frete) e responsabilidades são passados para o importador. (Fortaleza, 2008)
Nas operações mercantis de compra e venda, a Cláusula CIF inclui, no preço da mercadoria vendida, as despesas com seguro e frete
até o local de destino. Ou seja, constituem uma cláusula utilizada nas operações mercantis de compra e venda, pela qual o
preço da mercadoria vendida inclui despesas com seguro e frete até o local de destino. A Cláusula CIF estabelece o princípio de que cabe ao vendedor a obrigação de entregar a mercadoria ao comprador, no local em que este tem o seu estabelecimento, ou local que
indicar, ou no porto de destino, correndo por conta do vendedor as despesas com frete e seguro. Destaca-se que sendo o produto ou mercadoria transportada por embarcação, chegando esta ao porto de destino, as despesas de frete e seguro começam a correr por conta do comprador. Quando o transporte é terrestre, a responsabilidade do vendedor cessa no momento em que entrega a mercadoria ao transportador. (Fortaleza, 2008)
- Frete CIF: o pagamento deve ser feito pela empresa remetente da mercadoria;
- Frete FOB: o pagamento deve ser feito pelo destinatário da mercadoria.
Gestão do aprovisionamento/Integração das decisões de aprovisionamento e transporte/Introdução
Gestão do aprovisionamento/Integração das decisões de aprovisionamento e transporte/Condições do frete FOB
Gestão do aprovisionamento/Integração das decisões de aprovisionamento e transporte/Intervenção do aprovisionamento nas actividades de transporte
Gestão do aprovisionamento/Integração das decisões de aprovisionamento e transporte/Factores de decisão na selecção do modo de transporte e transportador
Gestão do aprovisionamento/Integração das decisões de aprovisionamento e transporte/Organização para tomada de decisões sobre o transporte
Gestão do aprovisionamento/Integração das decisões de aprovisionamento e transporte/Integração contínua
Gestão do aprovisionamento/Questões ambientais do aprovisionamento
Questões ambientais relativas ao aprovisionamento
Nos tempos actuais, a preservação e respeito pela natureza são cruciais. Não só pelo óbvio cuidado pelo ambiente e bem-estar da sociedade e natureza, mas também como marketing. A ideia de uma empresa limpa e cuidadosa é sempre favorável. Os clientes tendem a optar, actualmente, por empresas limpas e "verdes". Este factor cria uma certa pressão para melhorar esse aspecto para a empresa se manter competitiva no mercado. (Logistics Bureau, 2010)
É então necessário as empresas começarem a dar ênfase a boas práticas ambientais. No caso do aprovisionamento, o factor mais prejudicial é o transporte. As emissões de carbono e o barulho afectam tanto o ambiente como a comunidade. (Logistics Bureau, 2010)
A análise de impacto ambiental começa por avaliar certas áreas da rede de transportes como:
- Quantificar emissões de carbono das redes de distribuição;
- Testar métodos e modos diferentes de distribuição e quantificar a redução de emissões;
- Desenvolver planos para reduzir as emissões de carbono, modificando o uso do transporte.
Gestão de existências
Etapas de desenvolvimento - 9 fases | ||||||||
---|---|---|---|---|---|---|---|---|
Início: ![]() |
Básico: ![]() |
Criação: ![]() |
Desenvolvimento: ![]() |
Maturação: ![]() |
Revisão: ![]() |
Desenvolvido: ![]() |
Finalização: ![]() |
Abrangente: ![]() |
Introdução
Conceito de gestão de existências
Existências
Tipos de existências
Tipos de organizações e problemas de gestão de existências
Funções das existências
Classificação dos problemas de gestão de existências
- Componentes dos sistemas de existências
Custos das existências
- Conflito de objectivos
- Ciclo do fluxo das existências
- Considerações financeiras
- Influência nos ciclos económicos
Just in time
Técnicas de previsão
Sistemas de procura independente: modelos determinísticos
Modelo de quantidade fixa de encomenda
Modelo de quantidade económica de encomenda (QEE)
- Sistemas de procura discreta: modelos determinísticos
- Sistemas de procura independente: modelos estocásticos
- Alteração e limitações dos sistemas de existências
Encomendas únicas
Avaliação e medição de existências
Controlo de existências
Gestão de existências/Introdução
stocks ou Existências são acumulações de matérias-primas, fornecimentos, componentes, materiais em vias de fabricação e produtos acabados que surgem nos numerosos sectores de uma cadeia de produção e logística das empresas. Os stocks encontram-se normalmente nos armazéns, chão de fabrica, equipamentos de transporte de materiais e em armazéns de venda de produtos. O custo da manutenção dos stocks pode representar cerca de 20 a 40% do seu valor anual, logo a gestão de existências é uma mais valia a nível económico para a redução de custos. Apesar dos muitos avanços realizados para reduzir os níveis de stock pela integração de práticas como o just in time e redução de prazos o investimento anual em stock por parte dos fabricantes e vendedores, onde as vendas representam cerca de 99% do Produto Interno Bruto (PIB), representa cerca de 12% do PIB dos EUA.
Pode-se dividir a gestão de existências em 3 grandes partes:
- Stocks são vulgarmente geridos como produtos isolados que se encontram localizados em pontos exclusivos do armazenamento;
- O controle de stock visto como um agregado de existências, os gestores têm um grande interesse neste ponto em consequência da necessidade constante de controlar os níveis de existências;
- Gestão de Existências ao longo da cadeia de abastecimento.
Gestão de existências/Introdução/Existências
Existências são as quantidades armazenadas ou em processo de produção de quaisquer recursos necessários para dar origem a um bem (Filho, 2006, p. 62). Segundo Tersine (1988, p. 3), uma definição a atribuir às existências é a de material disponível num estado inactivo ou incompleto, a aguardar que seja vendido ou utilizado.
O controlo e a manutenção de existências é um problema comum a todas as organizações em qualquer sector da economia. Os problemas relacionados com as existências não se limitam a instituições com fins lucrativos, uma vez que estão igualmente presentes nas instituições sociais e/ou de índole não lucrativo. Os stocks existem transversalmente na sociedade e são uma realidade comum a explorações agrícolas, fábricas, grossistas, comerciantes a retalho, hospitais, igrejas, prisões, jardins zoológicos, universidades, e governos locais, regionais e nacionais. Na verdade, as existências são também relevantes na unidade familiar no que diz respeito à alimentação, vestuário, medicamentos e produtos de higiene pessoal, entre outros.
Numa base nacional agregada, o investimento total em existências representa uma parcela considerável do produto nacional bruto. Apesar deste problema existir desde sempre, o sector fabril privado apenas se começou a focar nos riscos e nos aspectos incertos dos stocks após a Segunda Guerra Mundial. Se, teoricamente, a gestão de stocks é a área das operações organizacionais mais desenvolvida, a prática mostra precisamente o contrário. Esta diferença diminui à medida que a gestão de materiais vai sendo incorporada na estrutura dos cursos das instituições educacionais (Tersine, 1988, p. 3).
Gestão de existências/Introdução/Tipos de existências
Segundo Tersine (1988, p. 4), as existências podem ser de:
- materiais de consumo corrente/consumíveis;
- matérias-primas;
- produtos em vias de fabrico;
- produtos acabados.
Os materiais de consumo corrente são consumidos durante o funcionamento normal de uma organização, embora não fazendo parte do produto final. Dos consumíveis típicos destacam-se lápis, papéis, lâmpadas, tinteiros para impressoras e artigos para a manutenção das instalações. Os materiais de consumo corrente nas fábricas são denominados MRO, de manutenção, reparação e operação.
De acordo com SENAC.DN (1998, p. 10), as matérias-primas são materiais necessários para a fabricação dos produtos onde são incorporados. Produtos em vias de fabrico são materiais que ainda se encontram na fase de produção, enquanto que produtos acabados são aqueles que já adquiriram a sua forma final, mas ainda não foram vendidos. Os tipos de materiais a serem mantidos em stock são muito diferentes, pois cada actividade produtiva tem necessidades específicas.
Gestão de existências/Introdução/Tipos de organizações e problemas de gestão de existências
Existem diferentes tipos de problemas de gestão de existências associados a diferentes tipos de organizações. Os problemas de gestão de existências podem ser delineados através da classificação das organizações como sendo de retalho, grossistas/distribuição e de fabrico/montagem. Dos sistemas de retalho, passando pelos grossistas aos de fabrico/montagem, os problemas associados aos stocks aumentam em magnitude e complexidade (Tabela 1).
Tipo de organização | Tipos de existências | |||
Consumíveis | Matérias primas |
Produtos em vias de fabrico |
Produtos acabados | |
| ||||
A. Sistemas de retalho | ||||
1. Venda de bens | * | * | ||
2. Venda de serviços | * | |||
B. Grossistas/distribuição | * | * | ||
C. Sistemas de fabrico/montagem | ||||
1. Sistemas de produção contínua | * | * | * | * |
2. Sistemas de produção intermitente | ||||
a. Abertos | * | * | * | |
b. Fechados | * | * | * | |
3. Projectos especiais | * | * | * | |
Os sistemas de retalho são organizações que fornecem bens e serviços ao consumidor final. O stock é comprado numa forma vendável e é utilizável sem processos ou conversões adicionais. Os sistemas que fornecem bens obtêm-nos de grossistas ou directamente das fábricas. Por exemplo, lojas que vendem produtos alimentares, ferramentas, e produtos consumíveis em vários departamentos. Estes sistemas deparam-se com problemas de stocks associados a materiais de consumo corrente e produtos acabados. Os retalhistas que fornecem serviços aos consumidores têm, apenas, problemas relacionados com materiais de consumo corrente. Organizações deste tipo incluem os hospitais, instituições financeiras, universidades e instituições penais.
Os sistemas de vendas por grosso/distribuição incluem as organizações que adquirem grandes quantidades de produtos manufacturados para distribuição aos retalhistas. Estas organizações não fornecem bens ao consumidor final, mas repartem o seu volume de compras, em pequenas quantidades, pelos retalhistas. Portanto, os sistemas de vendas por grosso/distribuição apresentam problemas de stocks limitados a produtos consumíveis e a produtos acabados.
Os sistemas de fabrico/montagem compreendem as organizações que adquirem matérias-primas e alteram a sua forma para criarem um produto acabado bem definido. Estes sistemas lidam com os problemas mais difíceis e complexos dos stocks e podem ser subdivididos em sistemas de produção contínua, intermitente e projectos especiais.
Os sistemas de produção contínua produzem um número limitado de produtos em grandes quantidades, em sequências fixas. As linhas de montagem para produção em massa são típicas destes sistemas. A instalação é concebida e dedicada, exclusivamente, aos seus produtos.
Os sistemas de produção intermitente envolvem a produção em lotes de muitos produtos diferentes, que partilham a capacidade de vários centros de trabalho. Uma operação intermitente aberta aceita encomendas de qualquer fonte, dentro das suas capacidades. Uma oficina aberta ao público é um exemplo de uma operação deste tipo. Operações intermitentes fechadas produzem bens apenas para um pequeno número de clientes limitada, num volume muito superior ao das operações abertas. Em complexidade, podem aproximar-se dos sistemas de produção contínua. Alguns exemplos são os de fabricantes de artigos com a marca do cliente, tal como para a Sears.
Os projectos especais são eventos com vida limitada e únicos, tais como o Projecto Apollo, satélites espaciais e estádios desportivos. Normalmente, os projectos especiais têm explicitados os seus objectivos ou número de produtos. Não há stock adicional de produtos acabados. As necessidades de matéria-prima são obtidas tendo em conta a quantidade de produtos acabados a produzir e a capacidade de produção é determinada de acordo com as especificações do contracto (Tersine, 1988, p. 4-6).
Gestão de existências/Introdução/Funções das existências
A existência de stocks deve-se ao facto de não haver um ajuste perfeito entre a procura e a oferta. Por várias razões e frequentemente, a oferta e a procura diferem, respectivamente, nas quantidades de stock fornecido e encomendado. Essas razões podem ser explicadas através de quatro factores: tempo, descontinuidade, incerteza e economia.
O factor tempo está relacionado com o longo processo de produção e distribuição necessário antes de um produto chegar ao consumidor final. Tempo é algo essencial para a realização de numerosas tarefas, tais como: a elaboração do plano de produção; a requisição de matérias-primas; o transporte dos materiais (tempo em trânsito) e a sua inspecção; a produção e a sua expedição para os armazenistas ou consumidores (tempo em trânsito). Como é normal, poucos consumidores estão dispostos a esperar tanto tempo para fazerem as suas compras. Os stocks permitem que uma organização reduza o tempo necessário para satisfazer a procura. Quando se dispõe de produtos imediatamente ou dentro de um período razoável, adquire-se boa reputação e consequentes benefícios por parte da organização.
O factor descontinuidade permite o tratamento de várias operações dependentes (retalho, distribuição, armazenagem, manufactura e aquisição) de uma forma independente e económica. A existência de stocks torna desnecessário que se ligue directamente a produção ao consumo ou que se force o consumo a adaptar-se às necessidades de produção. Os stocks libertam cada fase do processo de fornecimento-produção-distribuição da fase seguinte, possibilitando que cada uma opere mais economicamente. A existência de stocks de matérias-primas isola o fornecedor do consumidor; os stocks de produtos em vias de fabrico isolam os departamentos de produção uns dos outros; e os stocks de produtos acabados isolam os consumidores dos produtores. O factor descontinuidade permite a uma empresa a programação de muitas operações com um melhor nível de desempenho do que seria possível se estas fossem integradas dependendo umas das outras.
O factor incerteza refere-se aos eventos imprevisíveis que interferem nos planos iniciais de uma organização. Este factor inclui erros nas estimativas da procura; variações nos rendimentos da produção; avarias nos equipamentos, greves, acções da natureza, atrasos na expedição e mudanças climatéricas bruscas. Quando há stock disponível, a empresa encontra-se a salvo de casos como estes, que não foram planeados, nem previstos.
O factor economia permite que uma organização beneficie de alternativas de redução de custos, tais como a compra/produção de artigos em quantidades económicas. Uma das formas de reduzir os custos de um modo significantivo é a compra de grandes quantidades, com descontos de quantidade. Quando se encomendam produtos sem ter em conta o seu transporte e a dimensão do lote económico de encomenda, os custos por unidade podem tornar-se excessivos. A antecipação do aumento iminente dos custos dos materiais também influenciam positivamente a compra de artigos em grandes quantidades. Os stocks podem ser utilizados para manter a taxa de produção e estabilizar aos níveis de mão-de-obra em actividades temporárias ou sazonais.
Outra forma de explicar para que servem os stocks é através da introdução de classificações funcionais das existências. Todos os tipos de stock podem ser incluídos numa das seguintes categorias, com base na sua utilidade:
- Stock corrente;
- Stock de segurança;
- Stock de antecipação;
- Stock em trânsito;
- Stock de dissociação.
Stock corrente (também conhecido como stock cíclico ou do tamanho do lote) é o stock adquirido e mantido em antecipação às necessidades para que as encomendas possam ser feitas em lotes. O dimensionamento dos lotes é feito de modo a reduzir os custos de encomenda e de posse, obter descontos de quantidade ou beneficiar de tarifas de transporte mais baixas. Na generalidade, o stock corrente de uma organização é constituído pela quantidade média de stock resultante dos tamanhos dos lotes.
Stock de segurança (também denominado de stock tampão ou de flutuação) é o stock mantido em reserva para fazer face às incertezas da oferta e da procura. O stock de segurança é a média das existências durante os ciclos de reposição de modo a evitar a ruptura do stock.
Stock de antecipação (stock sazonal ou stock de estabilização) é um stock acumulado para fazer face aos picos de procura sazonal, greves, períodos de encerramento para férias ou deficiências na capacidade de produção. Este stock é adquirido com antecedência em relação às necessidades, para equilibrar a produção e estabilizar os níveis de mão-de-obra.
Stock em trânsito ou de produtos em curso de fabrico é o stock posto em trânsito para compensar o tempo que o material leva a chegar como matéria-prima, a percorrer o processo de produção e que leva a entregar o produto acabado. Externamente, este stock encontra-se em camiões, navios e carruagens ou em oleodutos. Internamente, este stock encontra-se a ser processado ou a ser movimentado entre centros de trabalho.
Stock de dissociação é o stock acumulado entre actividades ou fases dependentes de forma a reduzir a necessidade de operações sincronizadas. Esta é uma forma de isolar uma fase do sistema das outras fases, havendo, portanto, maior independência entre diferentes fases. Por conseguinte, este stock serve de facilitador no sistema de fornecimento-produção-distribuição, protegendo-o de utilização/desgaste excessivo.
Claramente, existem diversos tipos de stocks com o objectivo de servirem variados propósitos. Não podem ser geridos exactamente da mesma forma, mas devem ser geridos para desempenharem as suas funções específicas (Tersine, 1988, p. 7-8).
Gestão de existências/Introdução/Classificação dos problemas de gestão de existências
A gestão de existências inclui vários tipos de questões. Como não se conhece maneira de geri-las utilizando um único metodo, é necessário categorizar e classificar esses métodos em vários grupos principais. Todos os métodos serão avaliados de acordo com as suas condições ao nível da procura e variedade, prazos e limites de entrega, bem como os custos relacionados com as existências. Ora, isto exige que todos estes factores sejam tidos em conta, já que é preciso fazer o melhor trabalho possível no controlo das existências dadas estas condições. A única excepção a esta classificação é o método just in time que, com a sua filosofia de satisfazer a procura à medida que esta ocorre, há-de eliminar existências pela redução da variabilidade da procura e do tempo de ciclo de reposição, reduzindo o tamanho dos lotes e criando acordos com um número limitado de fornecedores, para assim garantir produtos de qualidade e o devido atendimento dos pedidos.
Natureza da Procura
A natureza da procura desempenha um papel extremamente importante na determinação do método adequado para controlar os níveis de existências. Existem vários tipos de padrões na procura, como terminal (peças de aviões), perpétua (sopas enlatadas), sazonal (aparelhos de ar condicionados) e irregular (materiais de construção). A característica mais comum na procura é a sua continuação ao longo do tempo, através de um período infinito de tempo, a que se dá o nome de perpétuo. Embora a procura de muitos produtos aumente e diminua ao longo dos seus ciclos de vida, outros apresentam ciclos suficientemente longos para serem considerados infinitos em termos de planeamento. Apesar de novas marcas surgirem a um ritmo de 20% ao ano, um ciclo de vida de 5 anos já é considerado suficientemente longo para justificar a sua inclusão entre os produtos com um padrão de procura perpétuo.
Existem, no entanto, produtos completamente sazonais, ou com surtos de procura. As existências criadas e mantidas para atender este a género de procura dificilmente são liquidadas, a não ser com recurso a promoções irresistíveis. Quando as projeções relativamente à procura se verificam incorretas, pedidos de devolução ou de nova produção são dificilmente atendidos, já que uma nova produção requer tempo e, quando esta tiver terminado, o surto/época de venda desse mesmo produto já terá passado. Roupas de marca, árvores de Natal e crachás de campanhas políticas são exemplos deste tipo de procura.
Gestão de existências/Introdução/Componentes dos sistemas de existências
Logística/Gestão de existências/Introdução/Componentes dos sistemas de existências
Gestão de existências/Introdução/Custos das existências
De acordo com Tersine (1988, p. 13-15), o objectivo da gestão de existências é ter as quantidades apropriadas de matérias-primas, consumíveis, e produtos acabados no lugar certo, no tempo certo e a um baixo custo. Os custos das existências estão associados à operação dos sistemas de existências e são parâmetros económicos básicos para qualquer modelo de decisão relacionado com as existências. Os custos mais relevantes para a maior parte dos sistemas são os seguintes:
- O custo de compra de um artigo é o custo de compra unitário se este for obtido a partir de uma fonte externa, ou o custo de produção unitário se for produzido internamente; um custo unitário deve ser sempre considerado como o custo de um artigo tal como foi colocado em stock. Para artigos comprados, considera-se o custo de compra adicionando o custo de transporte. Para artigos produzidos, o custo unitário inclui trabalho e material directos e custos indirectos de fabricação. Verifica-se a alteração de custo de compra em diferentes níveis de quantidade, quando um fornecedor oferece descontos de quantidade.
- O custo de encomenda/aprovisionamento tem origem na despesa proveniente de uma ordem de compra feita a um fornecedor exterior, ou nos custos das instalações de produção interna. Este custo é, normalmente, assumido como um custo que varia directamente com o número de encomendas e instalações existentes, e não como um custo que varia com a dimensão de cada encomenda. O custo de encomenda inclui actividades tais como fazer requisições, avaliar vendedores, escrever ordens de encomenda, receber e inspeccionar materiais, seguir ordens, e tratar da documentação necessária para completar a transacção. O custo das instalações abrange os custos de alteração do processo de fabrico para produzir o artigo encomendado; esta alteração inclui a preparação das ordens de compra/venda, o planeamento do trabalho, a instalação da pré-produção, a expedição e a aceitação da qualidade.
- O custo de posse está associado ao investimento feito em stocks e na manutenção do investimento físico em armazenagem. Neste custo estão incluídos custos de capital, impostos, seguro, custos de manuseamento, armazenagem, contracção, obsolescência, e deterioração. Os custos de capital reflectem a perda de poder ou custos de oportunidade. Se os fundos fossem investidos noutro sítio seria de esperar um retorno do investimento, mas o custo capital é uma conta caracterizada pela falta de retorno. Muitas regiões consideram os stocks como propriedades que podem ser ser cobradas, logo quanto mais stocks se tem, mais elevados são os impostos. Os requisitos para que haja cobertura dos seguros dependem da quantidade a ser reposta em caso de destruição da propriedade e os prémios de seguros variam com o tamanho do investimento feito em stocks. Obsolescência é o risco de perda de valor de um artigo devido a mudanças no estilo ou nas preferências do consumidor. Contracção é um decréscimo das quantidades em stock devido a perdas ou roubos. Deterioração significa a perda de propriedade devido à sua idade e à degradação ambiental. Muitos artigos sofrem um controlo de idade e devem ser vendidos antes da data de expiração (Ex: artigos alimentares, materiais fotográficos, e farmacêuticos). A suposição usualmente feita na gestão é a de que os custos de posse são proporcionais ao tamanho do investimento feito em stocks;
- O custo de ruptura é a consequência económica da escassez externa ou interna. Uma escassez externa ocorre quando a encomenda de um cliente não é satisfeita, enquanto que uma escassez interna ocorre quando não se satisfaz um requisito de um grupo, ou departamento, dentro da organização. A escassez externa pode incorrer custos de reserva, perda de benefícios presentes (perda de potenciais vendas) e futuros. A escassez interna pode dar origem a perdas de produção (ociosidade de mão-de-obra e de máquinas), e a atrasos na data de conclusão. A extensão do custo depende da reacção do consumidor face à falta de stock. Se ocorrer a procura por um artigo fora de stock, a perda económica depende da decisão do cliente em fazer uma nova encomenda, em se satisfazer com a substituição por um outro artigo ou de cancelar o seu pedido. Tipicamente, uma empresa expediria uma reserva de emergência para o artigo em falta e assumiria qualquer custo extra que fosse cobrado pelo serviço especial. Caso contrário, perde-se a hipótese de venda.
O objectivo principal da gestão de existências é, normalmente, a minimização dos custos. Apenas devem ser considerados para análise os custos que variam com o nível de stock. Por exemplo, os valores gastos em aquecimento, iluminação, e serviços de segurança para um armazém não devem ser considerados se não variam com a alteração dos níveis de stock.
Gestão de existências/Introdução/Conflito de objectivos
Logística/Gestão de existências/Introdução/Conflito de objectivos
Gestão de existências/Introdução/Ciclo do fluxo das existências
Logística/Gestão de existências/Introdução/Ciclo do fluxo das existências
Gestão de existências/Introdução/Considerações financeiras
Logística/Gestão de existências/Introdução/Considerações financeiras
Gestão de existências/Introdução/Influência nos ciclos económicos
Logística/Gestão de existências/Introdução/Influência nos ciclos económicos
Gestão de existências/Introdução/Just in time
De acordo com Tersine (1988, p. 26-27), o conceito de Just-in-time foi desenvolvido pelos japoneses e desafia a teoria das fundações clássicas dos stocks, no que diz respeito à produção de bens. Este conceito requer, precisamente, a produção das unidades necessárias nas quantidades necessárias e no tempo necessário, com o objectivo de ter um desempenho muito aproximado ao que foi programado. Isto significa que produzir uma peça a mais é considerado tão grave como produzir uma peça a menos, e o que for produzido acima das quantidades mínimas requeridas é tido como desperdício devido ao esforço e material despendido que ainda não precisa de ser utilizado. Neste ponto de vista, desperdício é qualquer recurso utilizado além do que foi requerido para adicionar valor ao produto, este recurso pode estar relacionado com materiais, máquinas ou mão-de-obra. É adicionado valor a um produto quando se realiza trabalhado sobre o mesmo, em actividades tais como a maquinação, montagem, pintura, e embalagem de um produto. Outras actividades tais como a movimentação, armazenagem, contagem, triagem e agendamento acrescentam custo a um produto mas não acrescentam valor, e custo sem valor é desperdício. Assim, qualquer acção que não adicione valor directamente ao produto é desperdício e deve ser minimizada, ou até mesmo eliminada.
O JIT nega o valor dos stocks, estes vão vistos de forma negativa pois são considerados um impedimento à qualidade dos produtos por esconderem os problemas em vez de possibilitar a sua resolução de uma forma rápida. Os stocks ocupam espaço, e quando se ocupa espaço inutilmente consome-se um recurso valioso. Para reduzir o desperdício resultante torna-se necessário o planeamento da disposição e dos fluxos de material, de forma eficiente. Com o JIT, o processo de ideal de fabricação pode ser visto como uma rede de centros de trabalho em que cada trabalhador completa a sua tarefa num item e, de seguida, passa o item para o próximo trabalhador, assim que este estiver disponível. O objectivo deste processo é anular as filas, com a finalidade de:
- minimizar o investimento em stocks;
- reduzir o tempo de aprovisionamento de produção;
- reagir rapidamente às mudanças na procura;
- descobrir qualquer problema relacionado com qualidade.
Uma vez que não é possível ter todos os trabalhadores adjacentes uns aos outros numa rede de trabalho, e que se deve incluir fornecedores exteriores, o sistema deve permitir que haja tempo de trânsito entre os centros de trabalho. No entanto, as quantidades transferidas são as mínimas possíveis e o tamanho do lote é uma fracção da produção diária. Não há lugar para contingências, os produtos são esperados sem erros aquando da sua recepção, as máquinas são tidas como disponíveis quando necessárias para produzir um item e cada compromisso de entrega deve ser cumprido na altura precisa em que foi planeado. Consequentemente, há um ênfase elevado na qualidade, na manutenção preventiva e na confiança mútua entre todos os participantes na rede de fabricação.
Técnicas de previsão
Etapas de desenvolvimento - 9 fases | ||||||||
---|---|---|---|---|---|---|---|---|
Início: ![]() |
Básico: ![]() |
Criação: ![]() |
Desenvolvimento: ![]() |
Maturação: ![]() |
Revisão: ![]() |
Desenvolvido: ![]() |
Finalização: ![]() |
Abrangente: ![]() |
Série temporal e dados transversais
Representação gráfica
Estatísticas univariadas, bivariadas e autocorrelação (Gonçalo Ferreira)
Medidas de precisão da previsão
Intervalo de previsão (Luís Pedro Seixas)
Estimativa dos mínimos quadrados
Transformações e ajustamentos (Gonçalo Ferreira)
Decomposição de séries temporais (José Santos)
Princípios
Médias móveis
Média móvel simples
Média móvel centrada
Média móvel ponderada
Alisamento local de regressão
Decomposição clássica
Métodos do Census Bureau
Decomposição STL
Alisamento exponencial (José Santos)
Regressão simples
Regressão múltipla (António Cruz)
Métodos ARIMA de Box-Jenkins (Luís Pedro Seixas)
Modelos avançados de previsão
Previsão a longo prazo
Dinâmica de grupo
Intenções
Opinião de peritos
Análise conjunta (Pedro Rito)
Metodologia bootstrap
Analogias
Extrapolação
Redes neuronais (Luís Pedro Seixas)
Previsão baseada em regras (Pedro Rito)
Sistemas periciais
Integração, ajustamento e combinação
Sistemas de procura independente: modelos determinísticos
Logística/Sistemas de procura independente: modelos determinísticos
Gestão de existências/Sistemas de procura independente: modelos determinísticos/Modelo de Quantidade Fixa de Encomenda
Gestão de existências/Sistemas de procura independente: modelos determinísticos/Modelo de Quantidade Económica de Encomenda (QEE)
Gestão de existências/Sistemas de procura discreta: modelos determinísticos
Logística/Gestão de existências/Sistemas de procura discreta: modelos determinísticos
Gestão de existências/Sistemas de procura independente: modelos estocásticos
Logística/Gestão de existências/Sistemas de procura independente: modelos estocásticos
Gestão de existências/Alteração e limitações dos sistemas de existências
Logística/Gestão de existências/Alteração e limitações dos sistemas de existências
Gestão de existências/Encomendas únicas
O modelo da quantidade de encomendas únicas diz respeito ao planeamento e controlo dos artigos em stock que são comprados apenas uma vez durante um período de tempo, ou aos quais apenas se dá início a uma linha de produção única. Os modelos mais familiares dos stocks (EOQ, EOI, e EPQ) ainda não põe em prática o método de encomendas únicas porque: (1) a procura não é contínua; (2) o nível de procura pode variar drasticamente de um período de tempo para outro; (3) um produto pode permanecer no mercado por pouco tempo devido à obsolescência ou perecibilidade.
O modelo quantitativo das encomendas únicas adapta-se à procura descontínua, variável e de curta duração. Este modelo é aplicável, especialmente, a duas categorias da procura: quando a procura de um determinado item ocorre em intervalos sem frequência e quando há uma procura incerta de um item de curta duração, mas em intervalos frequentes.
Procura e tempo de aprovisionamento conhecidos
Procura conhecida, tempo de aprovisionamento variável
Procura variável, tempo de aprovisionamento conhecido
Procura e tempo de aprovisionamento variáveis
Gestão de existências/Encomendas únicas/Procura e tempo de aprovisionamento conhecidos
Quando se conhece a procura e o tempo de aprovisionamento, não existem problemas de existências relacionados com encomendas únicas, o que raramente ocorre na prática. Para esta condição existir, toda a procura deve resultar em reservas vindas de clientes pacientes, ou todo o planeamento deve ser perfeito, sem ocorrências anormais nem atrasos(Tersine, 1988, p. 302-303).
Gestão de existências/Encomendas únicas/Procura conhecida, tempo de aprovisionamento variável
Uma vez conhecida a procura, também se conhece o tamanho da encomenda única. Com um tempo de aprovisionamento variável, a pessoa que toma decisões tem de se certificar de que a encomenda é recebida previamente à procura, para que não haja produção ociosa ou perda de vendas. Quando não há tolerância de vendas perdidas, as encomendas são feitas antes do tempo de aprovisionamento máximo. Se for possível apurar a distribuição do tempo de aprovisionamento, pode-se seleccionar um tempo de aprovisionamento, com uma elevada probabilidade de chegada antes da procura. Alternativamente, se a procura é fixa independentemente da altura em que os bens são entregues, uma entrega tardia apenas atrasa uma actividade. Esta situação pode ocorrer na construção de um edifício, onde um atraso na entrega apenas resulta num atraso na construção.
Quando existem fornecimentos internos, o tempo de aprovisionamento variável resulta de incertezas no planeamento e no processo produtivo. Pode se obter uma política para o nível de serviço, através de uma análise PERT (Tersine, 1988, p. 303-304).
Gestão de existências/Encomendas únicas/Procura variável, tempo de aprovisionamento conhecido
De acordo com Tersine (1988, p.304-305) , quando e procura é variável e o tempo de aprovisionamento é conhecido, o problema de existências relacionado com as encomendas únicas consiste na definição do tamanho da encomenda. Se a procura não é conhecida, mas se disponibiliza de uma distribuição da probabilidade da procura, o problema pode ser resolvido com uma tomada de decisão sob risco. É seleccionado o tamanho da encomenda com maior lucro ou com o menor custo esperados.
O procedimento, para a tomada de decisão sob risco, é determinar a estratégia da procura que conduza a um valor óptimo esperado. A probabilidade da procura ser menor ou igual à quantidade única de encomenda, para uma distribuição discreta, é a seguinte:
,
onde
Q = quantidade da encomenda única, em unidades,
M = procura em unidades (uma variável aleatória),
P(M) = probabilidade de uma procura de M unidades,
= procura máxima, em unidades.
A probabilidade da procura exceder a quantidade de encomenda única, é:
.
O procedimento, para calcular o valor esperado para cada estratégia de procura discreta, , é:
,
onde F(Q_iM_j) é o resultado da estratégica da procura, , quando a procura actual está no estado de natureza . A determinação dos resultados pode assumir duas formas, consoante a quantidade encomendada (), é menor ou maior do que o nível da procura (). Quando os resultados são expressos em termos de lucro ou benefício, aplicam-se as seguintes relações:
para (condição de ruptura de stock),
para (condição de excesso de stock),
onde
J = lucro ou benefício unitário,
l = perda por disponibilidade de stock não utilizado,
= quantidade única de encomenda de i unidades,
= nível de procura de j unidades,
= número de unidades em excesso de stock.
Quando os resultados são expressos em termos de custo ou sacrifício, aplicam-se as seguintes relações:
para (condição de excesso de produção),
para (condição de subprodução),
onde
P = custo unitário,
A = custo de ruptura de stock, por unidade,
= tamanho da ruptura de stock, em unidades.
Análise (marginal) do benefício
Segundo Tersine (1988, p.307-308), a secção anterior delineou um apuramento exaustivo da perspectiva de cada quantidade de encomenda para determinar o tamanho do lote com o valor óptimo esperado. Embora o método seja aplicável à quantidade única de encomenda envolvendo unidades de procura discretas, pode ser um processo tedioso quando o número de alternativas é grande. Nesta secção, é desenvolvida uma relação de optimização mais simples para indicar a quantidade de encomenda mais rentável. O objectivo é determinar o tamanho da encomenda (Q) que deve ser comprado no início do período (assumido que não há stock inicial) para maximizar o benefício esperado no final do período:
benefício esperado (EP) = receita esperada (ER) - custo esperado (EC);
receita esperada (ER) = receita de vendas esperada + receita de segurança esperada,
;
custo esperado (EC) = custo de compra + custo de encomenda + custi de ruptura esperado,
,
,
onde
A = custo de ruptura por unidade,
C = custo de encomenda, por cada encomenda realizada,
M = procura em unidades (uma variável aleatória),
f(M) = função da densidade de probabilidade da procura,
M - Q = tamanho da ruptura de stock, em unidades,
Q = quantidade da encomenda única, em unidades,
Q - M = quantidade de stock em excesso, em unidades,
P = custo de compra unitário,
P_1 = preço de venda unitário;
= probabilidade de uma ruptura de stock (probabilidade de haver uma procura superior a Q),
V = valor de segurança, por unidade,
= número de unidades em excesso (segurança) esperado,
= quantidade da ruptura de stock esperada, em unidades.
Para determinar o benefício máximo esperado, para uma distribuição contínua, é necessário derivar o benefício esperado em ordem à quantidade de encomenda e igualar a expressão a zero:
,
= probabilidade de ruptura de stock óptima,
onde
ML = P - V = perda marginal,
MP = = benefício marginal.
Análise da perda
Quando os itens são para uso interno, sem haver receita, a selecção do tamanho da encomenda única é baseada no menor custo esperado. Os componentes do custo são os custos por ordem, o custo de aquisição, custo de ruptura de stock e valor de segurança. A seguinte fórmula é relativa ao custo esperado para uma distribuição contínua:
custo esperado = custo de encomenda + custo de compra + custo de ruptura de stock esperado - segurança esperada,
, ,
onde
C = custo de encomenda, por cada encomenda realizada ou custo de instalação,
P = custo de compra unitário,
Q = quantidade da encomenda única, em unidades,
A = custo de ruptura por unidade,
M = procura em unidades (uma variável aleatória),
M - Q = tamanho da ruptura de stock, em unidades,
f(M) = função da densidade de probabilidade da procura,
V = valor de segurança, por unidade.
Para determinar a perda mínima esperada, para uma distribuição contínua, é necessário derivar o custo esperado em ordem à quantidade de encomenda e igualar a expressão a zero:
,
= probabilidade óptima de ruptura de stock.
É de observar que, se o custo de aquisição é igual ou superior ao custo de ruptura de stock, a probabilidade de ruptura desejada é 1. Nestas condições, nenhuma ordem seria instituída até existir uma procura conhecida. Além disso, se um item não tem valor de segurança, a probabilidade de ruptura de stock ideal é . A expressão é o nível de serviço e é a probabilidade de ruptura de stock. Assim, se a procura para o item é normalmente distribuída com uma média conhecida e desvio padrão , a seguinte expressão determina o menor custo esperado para a quantidade única de encomenda:
= tamanho óptimo da encomenda única,
onde Z é o desvio padrão normal obtido a partir da tabela normal, para uma probabilidade de ruptura de stock, (Tersine, 1988, p.310-312) .
Gestão de existências/Encomendas únicas/Procura e tempo de aprovisionamento variáveis
Quando ambos a procura e o tempo de aprovisionamento são variáveis, o problema é mais complexo. Uma vez que não se utiliza nenhum produto durante o tempo de aprovisionamento, o atraso numa entrega pode resultar na perda de procura. A procura pode ser determinada independentemente do tempo de aprovisionamento, como no caso em que a procura é variável mas o tempo de aprovisionamento é constante. O tempo de aprovisionamento pode ser fixado no seu nível máximo ou num nível de serviço aceitável.
As peculiaridades do problema das encomendas únicas ditam qual a política a seguir, no que se refere à determinação do tempo de aprovisionamento. As estipulações contratuais podem simplificar o problema do tempo de aprovisionamento, quando é utilizada procura vinda do exterior (Tersine, 1988, p. 314).
Gestão de existências/Avaliação e medição de existências
As existências são constituídas por características físicas objectivas, fluxos de bens, e financeiras, fluxos de capital, onde a vertente é mais subjectiva. Estes atributos são normalmente analisados separadamente de outras questões no interior da organização. A vertente financeira da gestão de existências está ligada à necessidade de medir o desempenho operacional num determinado período de tempo, juntamente com a análise da posição financeira da organização. Os procedimentos contabilísticos para os stocks dividem-se no método da avaliação e no método fluxo de existências (Tersine, 1988, p. 447).
Gestão de existências/Controlo de existências
As unidades em stock devem ser classificadas em categorias de forma a reduzir as existências. A complexidade do inventário requer que sejam aplicados procedimentos para a gerir e dividir os stocks em categorias. É inevitável que o tipo de controlo de existências seleccionado terá um impacto em toda a organização da empresa (Tersine, 1988, p. 501).
O ponto de partida no desenvolvimento de um sistema de controlo é uma análise de objectivos do sistema destinado. Este procedimento permite perceber quais são as actividades críticas nas operações em que o controlo pode ser mais eficiente.
É determinante que o mecanismo satisfaça o serviço e os objectivos operacionais no mínimo custo possível. Por esta razão é da responsabilidade da gestão de topo seleccionar o sistema de controlo e estabelecer níveis de stocks agregados.
Um sistema de operações deve indicar como as situações devem ser tratadas através de regras pré-determinadas e de procedimentos.
A análise de custos é a base da política de gestão de stocks. Esta análise terá de ser racional e emotiva. Apesar da sua exactidão o uso de técnicas matemáticas avançadas não resultará necessariamente num sistema efectivo.
Existem vários tipos de sistemas de controlo de existências. É difícil classifica-los de forma ordenada e separa-los das características que os definem.
Sistemas de controlo:
Sistema de procura independente
- Sistemas permanentes
- Sistemas de dois compartimentos
- Sistema periódico
- Sistema de reabastecimento opcional
- Sistemas de planeamento de distribuição
- Sistema de ordem de quantidade única
Sistemas de procura dependente
- Sistemas de planeamento de distribuição
- Sistema de ordem de quantidade única
- Sistemas de planeamento das necessidades dos materiais
- Sistemas just-in-time
Os sistemas permanentes e os de dois compartimentos são os dois sistemas que tem quantidade fixa de encomenda. O sistema periódico e o sistema opcional de reabastecimento são ambos sistemas de ordens fixas de encomenda. O planeamento das necessidades dos materiais e os sistemas just-in-time são derivadas dos sistemas de quantidade de ordem para ambientes de produção. Os sistemas baseados na quantidade são verificados
Reparações e sobressalentes
Etapas de desenvolvimento - 9 fases | ||||||||
---|---|---|---|---|---|---|---|---|
Início: ![]() |
Básico: ![]() |
Criação: ![]() |
Desenvolvimento: ![]() |
Maturação: ![]() |
Revisão: ![]() |
Desenvolvido: ![]() |
Finalização: ![]() |
Abrangente: ![]() |
Reparações e sobressalentes/Gestão de sobressalentes
A gestão de peças sobressalentes é uma parte fundamental da logística, pois geralmente representa cerca de 19 a 35% do custo unitário do produto (© DEGEI - UA, L.M.Ferreira). Para que esta gestão não seja uma "dor de cabeça" para os gestores, não pode ser só observada do ponto financeiro e/ou operacional, mas também como um serviço para o cliente, isto é, o serviço pós venda é também muito importante para satisfazer as necessidades do cliente. Esta gestão de sobressalentes consiste em ter um certo número de unidades do produto em armazém para que em caso de avaria ou defeito a empresa se encontarr capacitada para solucionar o problema em causa (Antonio Vinicius Pimpão Gomes; Peter Wanke).
Existem dois tipos de peças sobressalentes (Antonio Vinicius Pimpão Gomes; Peter Wanke):
- Itens reparáveis - são unidades que podem ser recuperadas, isto é, em caso de avaria a peça é substituida por uma semelhante e a que apresenta falha procede para o centro de reparação para posteriormente ser reposta no armazém;
- Itens consumiveis ou descartáveis - são unidades que são directamente descartadas e substituidas por outras que se apresentam em stock.
Um dos grandes desafios dos gestores é conseguir definir a quantidade e localização das peças sobressalentes, como é o caso do sector da aeronáutica, que possui peças com elevado custo de aquisição e de armazenamento. Existem duas fontes de estacionariedade na procura de peças de aviões: pequenas peças que vão ter uma procura mais previsível (os parafusos, filtros, chips, etc.) e as peças de maior porte e maior valor acrescentado, (motores, sistemas hidraulicos, componentes das asas, etc.) que vai variando ao longo do tempo. Para estas peças de maior valor existem umas previsões de quanto tempo demoram a danificar-se ou mesmo destruirem-se, mas mesmo assim nunca se tem a certeza de que elas aguentam até a essa estimativa. Por isso mesmo, tem que se ter uma atenção especial para que não tenhamos uma ruptura do stock nem um excesso de peças sobressalentes de valor acrescentado.
Um dos pontos fulcrais de uma boa gestão é detectar o tempo de vida das peças para que haja um rápido ajustamento de stock. Geralmente se tivermos uma detecção mais retardada do tempo de vida da peça os custos de transporte da peça sobressalente vão subir muito, devido ao facto de os fornecedores terem que transportar a peça num curto espaço de tempo, ou então a resposta à falha da peça é muito grande, levando a que os clientes fiquem descontentes.
A localização de armazéns é um dos pontos elementares da logística de sobressalente pois a resposta à procura de peças tem que ser o mais reduzida possível, daí obtar-se por ter um ou dois (no máximo) armazéns por continente e a maior parte espalhados por todo o mundo. Os armazéns espalhados por todo o mundo, geralmente denominados regionais, situam-se em locais de serviço para que possam controlar melhor o nivel de serviço da procura, isto é, o armazéns centrais tentam satisfazer a procura o mais rapidamente possível enquanto os armazéns regionais fornecem ao armazém central.
Existe uma inspecção de avião intercalada entre cada vôo, assim, se houver necessidade de trocar alguma peça danificada o armazém central tem que ter a capacidade de responder a esta procura, respondendo no máximo de quatro dias. Se houver uma avaria mais grave mas que o avião ainda possa voar, então este dirige-se a um local de serviço (armazém central). Neste caso o tempo de espera do avião não pode exceder dois dias. Existe ainda a situação de o avião não poder levantar vôo (Aircraft on Ground) e aí sim, a capacidade de resposta do armazém central é fulcral, pois o transporte de peças sobressalentes tem que ser respondida no máximo de seis horas. O Aircraft on Ground é um termo de manutenção aérea que indica que existe uma avaria suficientemente grave para que o avião não levante vôo. Quando um avião se encontra no estado de Aircraft on Ground e não houverem peças suplentes para substituirem as defeituosas, a companhia aérea geralmente pede ajuda ao aeroporto para que troque a peça em questão ou até mesmo a outra companhia aérea.
A gestão de stocks de valor acrescentado é feita através de uma revisão periódica do stock para que a peça sobressalente seja substituida no máximo em quadro dias.
Movimentação de materiais
Etapas de desenvolvimento - 9 fases | ||||||||
---|---|---|---|---|---|---|---|---|
Início: ![]() |
Básico: ![]() |
Criação: ![]() |
Desenvolvimento: ![]() |
Maturação: ![]() |
Revisão: ![]() |
Desenvolvido: ![]() |
Finalização: ![]() |
Abrangente: ![]() |
Introdução
Princípios de movimentação de materiais
Listas de verificação
Unidade de carga
Equipamento
Equipamento de contentorização e unitivo
Equipamento de movimentação de materiais
Equipamento de armazenagem
Armazenagem de unidades de carga
Equipamento de armazenagem de pequenas cargas
Equipamento de identificação e comunicação automática
Movimentação de materiais/Introdução
Segundo Guarnieri et al. (2006, p. 3), as crescentes exigências da competitividade dos mercados permitiram que as empresas adoptarem métodos e equipamentos mais eficientes a fim de melhorarem a sua produtividade e a qualidade dos serviços prestados. A logística empresarial fez com que as empresas adquirissem um maior controlo de todas as actividades de movimentação e armazenagem, facilitando assim, a verificação eficiente do fluxo de mercadorias, ou seja, desde o carregamento inicial de materiais de um fornecedor, até à venda do produto fabricado ao consumidor final.
Segundo Meyers (2000, p. 2), a movimentação de materiais não é mais que combinação de métodos e processos, capazes de movimentar toda a mercadoria, matéria-prima e produto final, para o lugar certo, com a quantidade específica e em tempo correto, numa sequência definida pelo layout da fabrica. O mesmo autor (2000, p. 223) afirma que a movimentação de materiais e produtos significa transportar pequenas ou grandes quantidades de bens, em distâncias relativamente pequenas, como por exemplo no interior do local de produção, como fábricas, lojas, armazéns, entre outros. Assim, pode ser definida como processo global de movimentação de materiais num ambiente de manufatura. Há quem defina este processo de transporte do material como "a arte e ciência da movimentação, embalagem e armazenamento de material em qualquer forma".
- Objetivos
O principal objectivo do processo de movimentação de material é reduzir os custos operacionais na concepção do produto final e no seu armazenamento. Contudo, é necessário alcançar outras metas e cumprir especificação primordiais a fim de alcançar o objectivo principal - redução de custos. Segundo Ray (2008, p. 2), alem da redução de custos, existem outros objectivos, tais como:
- Eficiência e segurança na movimentação dos materiais;
- Transporte dos materiais em tempo útil, com a quantidade exacta, para o local desejado;
- Armazenamento de materiais, optimizando a capacidade espacial fornecida pela empresa;
- Soluções de baixo custo para as actividades de movimentação de materiais.
- Importância
Segundo Ray (2008, p. 2), muitas empresas aumentam os seus custos devido a rotinas ineficientes na movimentação de materiais. A movimentação de materiais permite a optimização da produção e, consequentemente, aumenta a eficiência da empresa. A movimentação de materiais permite, também:
- Melhorar a eficiência do sistema de produção, movimentando quantidades exactas de materiais ao longo da sua linha de produção e armazenamento;
- Reduzir o custo global;
- Redução dos estragos nos materiais durante a sua movimentação;
- Maximizar a utilização do espaço para armazenamento;
- Minimizar o risco de acidente na movimentação manual de materiais.
- Conceito de sistema
Segundo Ray (2008, p. 2) e Kulwiec (1985, p. 5), a movimentação de materiais pode ser definida como parte integrante de um sistema de produção e que permite optimizar a eficiência da movimentação de materiais no sistema. Segundo Kulwiec (1985, p. 4), a movimentação de materiais deve descrever os tipos de equipamentos que irão ser utilizados nas diversas operações envolvidas no sistema, como a embalagem, transporte e armazenamento. Independentemente do tamanho e da complexidade do material, o sistema de movimentação deve atender dois tipos de fluxos em simultâneo: o fluxo físico de materiais e o correspondente fluxo de informação. O fluxo de informação permite fazer decisões relativamente ao controlo do fluxo físico do material, fornecendo informações sobre o componente que está a passar por um dado ponto, numa dada altura, para onde vai e o que vai ser executado posteriormente. O controlo do fluxo do material pode ser manual, mecanizado, ou automático.
- Aspectos fundamentais da movimentação
Segundo Meyers (2000, p. 223), a movimentação do material pode ser pensada como tendo cinco dimensões distintas: movimento, quantidade, tempo, espaço e controlo. O movimento envolve a eficiência do transporte do material durante a sua transformação. Interessa movimentar-lo o mais rápido possível, com segurança e integridade, pois a movimentação rápida pode ser um aspecto importante na redução de custos. A ineficiência dos equipamentos na movimentação de materiais pode acarretar altos custos para a empresa. A eficiência da movimentação do material encontra-se relacionada com a quantidade exacta a ser transportada pelos equipamentos. A quantidade a ser movimentada ditará o tipo e natureza do equipamento a ser utilizado, tal como o custo associado a essa movimentação. A movimentação de materiais não se baseia somente na deslocação, embalagem e armazenamento de produtos, mas também no desempenho temporal de equipamentos específicos, dentro de determinados limites estabelecidos. Aspectos relacionados com o tempo, como por exemplo: tempo das operações, horas de operação, tempo ocioso, repetição de operações e movimentações, inventário excessivo, em entre outros; podem ser optimizados a fim de obter uma eficiência maior na movimentação dos materiais e redução de custos. Os materiais devem chegar ao local de trabalho, estação de montagem e produção ou até mesmo ao cliente, a tempo e horas. O aspecto espacial na movimentação de materiais encontra-se relacionado com o espaço necessário existente na fábrica, quer para efeitos de armazenamento dos materiais, produtos e equipamento, quer para efeitos da sua circulação de um lugar para o outro. Pode-se dizer que a movimentação do material é parte integrante na decisão do design do layout. O rastreamento do material e a sua identificação são alguns aspectos fundamentais no controlo da movimentação. Existe a responsabilidade de verificar se o produto desejado encontra-se no sitio certo, quer durante a sua produção, quer esteja em armazenamento.
- Formas de movimentação
Segundo Kulwiec (1985, p. 5), dependendo do tipo de sistema de produção e armazenamento, o modo de controlo e movimentação das materiais e produtos pode ser manual ou automático.
Segundo Cheung (2007, p. 8-9, a Movimentação manual de materiais envolve o uso do corpo humano para levantar, baixar, atestar, ou transportar cargas de um local para outro. No entanto, quando as estas tarefas são realizadas de forma incorrecta ou excessiva, podem expor os trabalhadores a factores de risco físico, fadiga e lesões. Para evitar estes problemas, a organização pode beneficiar do avanço das novas tecnologias e melhorar o ajuste entre as tarefas do trabalho e a capacidade dos seus trabalhadores. A utilização de equipamentos e máquinas reduzem e previnem o risco de lesões e esforços dos trabalhadores, como também aumentam a produtividade e a qualidade do serviço.
Segundo Crowsox ((Crowsox, 2006, p. 57-58)), o equipamento automatizado é projectado e construído para atender determinados requisitos de transporte do material. A automatização de processos de fabricação e de operações de equipamentos tem sido adoptada por muitas empresas de modo a colmatar os problemas da movimentação manual e aumentar os níveis de produtividade. A automatização oferece muitas vantagens na movimentação de materiais, nomeadamente o fornecimento de informação relevante na tomada de decisões. Segundo Lambert (1998, p. 320), outras vantagens destes sistemas são: melhoramento dos níveis de serviço, aumento da produtividade e eficiência do sistema, e diminuição do transporte de materiais durante os seus processos .
- Controlo da movimentação do material
Segundo Kulwiec (1985, p. 4-5, nos sistemas de movimentação manual e mecanizados, todos os processos de movimentação são observados e controlados pelo operador, através de registos e correcções, quando necessárias, de mecanismo eléctricos constituintes dos equipamentos. Nos sistemas automáticos, scanners e outros tipos de aparelho de controlo e gestão permitem aceder a toda a informação acerca do estado dos equipamentos e dos materiais, em tempo real. O sistema pode estar sob controlo de um computador local, que por sua vez, pode estar ou não, ligado a um outro computador de alto nível. A integração de equipamentos automatizados de controlo da produção e da movimentação nos processos industriais irá ao encontro das necessidades da empresa, visto que existem processos onde é dispensável a utilização de determinados equipamentos, reduzindo assim os custos associados a esta aplicação.
- Custos
Segundo Yaman (1999), todos os gastos gerais de fabrico de uma empresa têm de ser justificados. Cerca de 30% a 70% dos custos totais de produção pertencem à movimentação de materiais. Esta analise percentual deve-se à falta de rigor de análises criticas e técnicas, quer dos equipamentos quer dos métodos em funcionamento. Segundo Meyer Meyers (2000, p. 2), um dos primeiros pontos fundamentais a ter atenção é analisar o fluxo da movimentação de materiais, layout e equipamentos de movimentação e armazenagem. Quando os equipamentos utilizados não são os mais apropriados para transportar o material, tornam-se ineficientes na produção em determinadas situações e são responsáveis pelo aumento de custos, tempo de produção e perdas durante a movimentação de materiais. Melhorando os aspectos mencionados, obtêm-se benefícios quando existe uma maior eficiência do sistema na movimentação do material.
Movimentação de materiais/Princípios de movimentação de materiais
O Material Handling Institute definiu 10 princípios de movimentação de materiais. Os 10 princípios são fundamentais para o projecto, concepção, análise e operação de sistemas de movimentação de materiais (THE TEN, [2010]).
- Planeamento. Toda as movimentações de materiais devem ser planeados de acordo com a sua necessidade, objectivos de desempenho e especificações funcionais propostas no início do projecto.
- O sucesso do planeamento de projectos de movimentação de material em grande escala requer uma equipa especializada e integrada que engloba fornecedores, consultores (quando necessário), gestores, engenharia, informática e sistemas de informação, finanças e operações;
- O planeamento da movimentação de material deve responder aos objectivos estratégicos da organização, bem como às necessidades a cumprir a curto prazo;
- O planeamento deve ser baseado em métodos e problemas existentes, sujeito às limitações económicas e físicas actuais, e atender aos requisitos e objectivos organizacionais;
- O planeamento deve promover a engenharia simultânea dos produtos, projecto e layout dos processos e métodos de movimentação de materiais, de modo a tornar o sistema flexível, para que possíveis alterações no mesmo, possam ser compreendidas e resolvidas, ao contrário das práticas de projectos independentes e sequenciais;
- Normalização dos métodos de movimentações de materiais, equipamentos, controlos e software, sem prejudicar a flexibilidade, modularidade e as taxas de produção necessárias do sistema. Normalizar métodos de movimentação de material e equipamentos, reduz a variedades e a personalização dos processos.
- O engenheiro deve seleccionar os métodos e equipamentos que possam executar diversas tarefas, sob várias condições de funcionamento, e antecipar futuras alterações no sistema. Ou seja, os métodos e equipamentos devem ser normalizados e, ao mesmo tempo, garantir a flexibilidade e modularidade do sistema;
- Deve ser aplicada aos diferentes métodos de movimentação de materiais, tais como aos diversos tamanhos de embalagens e contentores, bem como a procedimentos operacionais e equipamentos;
- A normalização, flexibilidade e modularidade devem-se complementar, proporcionando, assim, compatibilidade.
- Trabalho. A movimentação de materiais é igual ao produto da taxa de fluxo de movimentação de materiais (volume, peso ou quantidade por unidade de tempo) pela distância percorrida. A movimentação de materiais deve ser minimizada, sem prejudicar a produtividade ou o nível de serviço exigido pela operação.
- Simplificação de processos através da redução, combinação ou eliminação de movimentações desnecessárias;
- Deve-se considerar a armazenagem e a recolha de material, como movimentos distintos e componentes da distância percorrida;
- O trabalho da movimentação de materiais pode ser simplificado e reduzido através de layouts e métodos eficientes;
- Sempre que possível, a força gravitacional deve ser utilizada para mover materiais ou para ajudar na sua movimentação, tendo em atenção a segurança e potenciais danos no produto;
- A menor distância entre dois pontos é em linha recta.
- Ergonomia. É importante reconhecer as capacidades e limitações humanas, tanto físicas como psicológicas, de modo a conceber métodos de movimentação de material e equipamentos seguros e eficazes.
- Os equipamentos devem ser seleccionados de forma a eliminar movimentações manuais repetidas e extenuantes e que efectivamente possam interagir com os operadores;
- Nos sistemas de movimentação de materiais, modificações ergonómicas no layout e projecto do local de trabalho é importante prestar atenção às características físicas humanas;
- Os equipamentos especialmente concebidos para a movimentação de materiais são geralmente mais caros do que equipamentos genéricos. Contudo, é possível prevenir o risco de lesão e fadiga do trabalhador, assim como possíveis erros e ineficiências operacionais associadas, minimizando custos e prejuízos a longo prazo (Taylor, 2009, p. 7-5).
- Unidade de carga. A unidade de carga deve ser dimensionada e configurada de forma a satisfazer os objectivos de fluxo de materiais e armazenagem em cada fase da cadeia de abastecimento.
- Facilidade na recolha e movimentação de vários itens individuais como uma unidade de carga, do que a movimentação de vários itens, um de cada vez;
- O tamanho e a composição da carga podem ser alterados durante as diversas fases de fabricação, armazenagem e distribuição;
- É usual existirem unidades de carga de grandes dimensões de matérias-primas e produtos, antes e depois da fabricação, respectivamente;
- Durante a fabricação, unidades de carga de pequenas dimensões, por vezes constituídas por um item, diminuem os stocks em curso de fabrico e os tempos dos ciclos de produção;
- Unidades de carga de pequenas dimensões são utilizadas na produção, a fim de atingirem objectivos operacionais, tais como flexibilidade, fluxo contínuo de materiais e a entrega just-in-time;
- Unidades de carga compostas pelo agrupamento de diferentes itens são comuns nos processos just-in-time e em estratégias de oferta personalizada, desde que a selectividade dos itens não fique comprometida.

- Utilização do espaço. Deve ser feita de forma a tornar o sistema de movimentação de materiais mais eficaz e eficiente. Na movimentação de materiais, o conceito de espaço é tridimensional, normalmente considerado como espaço cúbico.
- Devem-se eliminar todos os espaços desordenados e desorganizados, como por exemplo: corredores obstruídos;
- Nas áreas de armazenamento, o objectivo é maximizar e balancear a densidade de armazenamento, de modo a obter acessibilidade e facilidade de seleccionar e carregar determinados itens;
- A utilização do transporte aéreo de carga, no interior do espaço cúbico da instalação, deve ser considerada como uma opção de melhorar e optimizar o sistema de movimentação de materiais (ver Figura 1);
- Sistema. As actividades de movimentação e armazenagem devem ser totalmente integradas de forma a criar um sistema operacional coordenado, que envolva a recepção, inspecção, armazenagem, produção, montagem, embalagem, selecção, expedição, transporte e movimentação de devoluções.
- A integração de sistemas deve envolver toda a cadeia de abastecimento, incluindo a logística inversa. As principais entidades da cadeia de abastecimento são: fornecedores, fabricantes, distribuidores e clientes;
- Os níveis de stock devem ser reduzidos em todas fases da produção e distribuição, considerando as variabilidades do processo e os serviços prestados ao cliente;
- Os fluxos de informação e de materiais devem ser integrados e processados em simultâneo. O fluxo de informação geralmente segue o fluxo de material;
- Os métodos devem facilitar a identificação de materiais e de produtos, determinar a sua localização, estado de processamento e movimentação, dentro das instalações e na cadeia de abastecimento;
- As necessidades dos clientes em relação à quantidade, qualidade, pedidos e cumprimento dos prazos devem ser atendidas com rigor.
- Automatização. As operações de movimentação de materiais devem ser mecanizadas ou automatizadas, sempre que possível, de modo a aumentar a eficiência, capacidade de resposta, uniformidade e previsibilidade do sistema, e reduzir custos operacionais, eliminando o trabalho manual repetitivo e potencialmente inseguro.
- Simplificação dos processos e métodos pré-existentes, antes de instalar sistemas mecanizados ou automatizados;
- Utilização de sistemas de informação de forma a integrar, controlar e gerir todos os fluxos de informação e de materiais;
- Os problemas de interface são críticos para garantir o sucesso da automatização;
- Os itens a ser movimentados devem possuir formas e características padronizadas que permitam a movimentação mecanizada ou automatizada.
- Meio-ambiente. O impacto no meio-ambiente e o consumo de energia devem ser considerados como aspectos relevantes no projecto e selecção de equipamentos e de sistemas de movimentação de materiais, de modo a preservar os recursos naturais existentes na Terra e minimizar os possíveis efeitos negativos no meio ambiente.
- Contentores, paletes e outros equipamentos usados para proteger unidades de carga devem ser concebidos visando a reutilização e a biodegradabilidade após a sua utilização, sempre que possível;
- O projecto de sistemas deve ser dimensionado de modo a acomodar equipamentos e subprodutos de movimentação de materiais e produtos;
- Materiais e produtos perigosos têm necessidades especiais no que diz respeito à protecção contra o derramamento, combustibilidade e outros riscos;
- Custo do ciclo de vida. A análise económica deverá considerar o ciclo de vida de todos os sistemas resultantes da movimentação de materiais, incluindo todas as despesas e gastos desde o momento em que o primeiro valor é gasto para projectar ou adquirir um novo método ou equipamento de movimentação, até a eliminação ou substituição total do métodos ou equipamento.
- Os custos do ciclo de vida do sistema incluem o investimento de capital, instalação, configuração e preparação de métodos e equipamentos, treino, teste e recepção do sistema, operação (mão-de-obra, serviços, entre outros), manutenção e reparação, revenda e disposição final;
- O plano de manutenção irá prolongar a vida útil do equipamento. Os custos associados à manutenção e substituição de equipamentos também devem ser incluídos na análise económica;
- Deve de existir um plano substituição de equipamentos obsoletos, a longo prazo;
- Além dos custos operacionais mensuráveis, existem outros factores de natureza estratégica e competitiva que devem ser quantificados, se possíveis.
Movimentação de materiais/Listas de verificação
Listas de verificação
Movimentação de materiais/Unidade de carga
Segundo Tompkins et al. (1996, p. 164), dos 10 princípios da movimentação de materiais, existe um princípio que deve-se tomar em consideração: o princípio da unidade de carga. Uma unidade de carga pode ser definida como a carga a ser movimentada, ou recolhida, de uma vez só, ao mesmo tempo. A unidade da carga é parte integrante do sistema de movimentação de materiais (Tompkins et al., 1996, p. 168).
O tamanho da unidade de carga e a sua composição podem ser alteradas durante as movimentações de produto. As unidades de carga podem ser compostas por um item individual, ou por diversos itens. Independentemente disso, as unidades de carga devem ter o tamanho e configuração apropriado para que os objectivos de fluxo e movimentação de materiais sejam atingidos (Machado, 2006).
Além do material, a unidade de carga inclui o contentor, ou o suporte, que será utilizado para movimentar o material. A disposição do material em unidades de carga pode ser efectuada no interior ou sobre o equipamento de contentorização (Tompkins et al., 1996, p. 164). A utilização da contentorização na distribuição física realça a importância do conceito de unidade de carga. O tamanho da unidade de carga pode variar, conforme o equipamento utilizado. A integridade da unidade de carga pode ser mantida de diversas maneiras. Por exemplo, equipamentoos como tote boxes, caixas, paletes, e pallets boxes, podem de utilizados para movimentar a unidade de carga. Da mesma forma, existem equipamentos de unitização que asseguram a formação, protecção e qualidade das unidades de carga, tais como: equipamento de shrinkwrapping, stretchwrapping e cintar.
A determinação do tamanho da unidade de carga, bem como o método de contentorização, é influenciada por diversos factores, como por exemplo: o material a ser unificado; o número de vezes que o material é removido da unidade de carga para ser processado; a quantidade de material a movimentar; as condições ambientais que a unidade de carga encontra-se exposta; a susceptibilidade do material a danos, entre outros factores. Para dimensionar a unidade de carga, é necessário ter em atenção algumas medidas:
- Determinar a aplicabilidade do conceito de unidade de carga;
- Seleccionar o tipo de equipamento a utilizar para movimentar a unidade de carga;
- Identificar a origem mais distante da unidade de carga;
- Estabelecer o destino mais distante da unidade de carga;
- Determinar o tamanho da unidade de carga;
- Configurar a composição e estrutura da unidade de carga;
- Determinar o método de formação da unidade de carga.
Geralmente, a unidade de carga é formada através da sobreposição de itens na palete. As dimensões dos itens irá influenciar o tipo de equipamento de armazenagem da unidade de carga a utilizar (Tompkins et al., 1996, p. 165). Caso a unidade de carga seja muito pesada, deve-se ter em consideração a importância do peso, em vez do volume, da unidade de carga (Tompkins et al., 1996, p. 168). As dimensões da unidade de carga e os equipamentos utilizados para a sua movimentação devem ser compatíveis, com outros equipamentos.
As especificações da unidade de carga podem ser influenciadas pela instalação de produção, ou de armazenagem. A largura das portas de entrada e saída, column spacings, largura dos corredores, o raio de curvatura dos veículos e a altura de empilhamento de equipamentos de armazenagem, são alguns dos factores que influenciam as dimensões e estrutura da unidade de carga. Tem havido inúmeros casos, em que os equipamentos adquiridos não puderam ser instalados, nem utilizados, devido às suas grandes dimensões.
Movimentação de materiais/Equipamento
Etapas de desenvolvimento - 9 fases | ||||||||
---|---|---|---|---|---|---|---|---|
Início: ![]() |
Básico: ![]() |
Criação: ![]() |
Desenvolvimento: ![]() |
Maturação: ![]() |
Revisão: ![]() |
Desenvolvido: ![]() |
Finalização: ![]() |
Abrangente: ![]() |
- Equipamento de contentorização e unitivo
- Equipamento de movimentação de materiais
- Equipamento de armazenagem
- Equipamento de identificação e comunicação automática
Movimentação de materiais/Equipamento/Equipamento de contentorização e unitivo
Luís Baptista
Etapas de desenvolvimento - 9 fases | ||||||||
---|---|---|---|---|---|---|---|---|
Início: ![]() |
Básico: ![]() |
Criação: ![]() |
Desenvolvimento: ![]() |
Maturação: ![]() |
Revisão: ![]() |
Desenvolvido: ![]() |
Finalização: ![]() |
Abrangente: ![]() |
Segundo Tompkins et al. (1996, p. 169), os contentores e unificadores (unitizers) são equipamentos utilizados em projectos de sistemas de movimentações de materiais. Estes equipamentos unificam o material, em unidades de carga, de modo a facilitar e economizar as movimentações e operações de armazenagem (1996, p. 173). Estes equipamentos servem, também, para proteger e garantir a segurança e qualidade da composição da unidade de carga.
Movimentação de materiais/Equipamento/Equipamento de contentorização e unitivo/Contentores
Os contentores são frequentemente utilizados para facilitar a movimentação e armazenamento de itens. Geralemnte, os itens são colocados em tote pans, ou em skid boxes. Os equipamentos de contetorização sao utilizados para facilitar a movimentação e armazenamento de unidades de carga, dependendo do tamanho e da configuração da mesma (Tompkins et al. , 1996, p. 173).
Por exemplo, o processo de transporte de aveia em sacos de serrapilheira, pode ser realizado através de um belt conveyor. Todavia, caso a contentorização dos sacos for efectuada em paletes, então já se justificaria a utilização de um roller conveyor. Dependendo da concepção do sistema de movimentação, é possível alterar a forma de transporte e de unitização da carga. Na generalidade, as decisões, sobre a forma como material deve ser movimentado ou armazenado, são influenciadas pela maneira como material se encontra contentorizado.
Segundo Chan et al. (2006, p. 143), existem alguns problemas no carregamento de contentores. Contudo, muitos investigadores têm vindo a abordar estes problemas, com o objectivo de tornar os sistemas logísticos de contentorização mais eficientes, reduzindo os espaços vazios no interior dos contentores.
Os problemas de carregamento de contentores podem ser divididos em dois tipos: problema do carregamento de um contentor ou de vários contentores. No primeiro caso, o objectivo é optimizar o espaço disponível no interior do contentor, sem considerar quaisquer restrições sobre o número de itens disponíveis para efectuar o carregamento. Pressupõe-se, então, que não há condições especiais impostas sobre o transporte dos itens. Neste caso, é permitido que alguns itens possam ser deixados de fora. Já no segundo caso, o objectivo principal é minimizar o numero de contentores que serão utilizados para armazenar e carregar os itens. Para isso, é necessário ter em consideração o carregamento de todos os itens, uma vez que se pretende minimizar o espaço disponível no interior dos contentores. Em ambos as situações, a maximização de ocupação do volume no interior dos contentores é a principal preocupação. Existem também outros aspectos importantes a considerar, no carregamento de contentores, como por exemplo: o peso dos itens, peso total do carregamento, estabilidade do contentor, entre outros. O problema tridimensional do carregamento de contentores pode ser descrito da seguinte forma: existe um conjunto de itens que possuem forma regular (quadrada, rectangular, triangular, entre outras) e tamanho variável, e que têm que ser armazenados e carregados num, ou mais, contentor, também estes de diferentes tamanhos (Eley, 2005, p. 359). De modo a utilizar, eficientemente, o espaço disponível no contentor, há que ter em consideração os seguintes aspectos:
- As caixas e recipientes, com mesmo tamanho, são agrupadas em unidades de carga;
- Apenas são permitidos arranjos ortogonais, ou seja, os itens são armazenadas em paralelo com as paredes do contentor;
- Pode haver rotação dos itens;
Existem outros problemas semelhantes ao problema de carregamento do contentor: bin packing problem (em inglês), problema da mochila (knapsack problem, em inglês) e cutting stock problem (em inglês). O objectivo deste problemas é minimizar o desperdício de espaço no interior dos contentores (Chan et al., 2006, p. 144).
Segundo Tompkins et al. (1996, p. 173), os equipamentos são considerados contentores são:
- Paletes. As paletes são, de longe, o equipamento mais comum de unitização de unidades de cargas;
- Skids e skid boxes. As Skids e skid boxes são equipamentos feitos de metal e por isso são bastante resistentes e permitem a unitização de grandes volumes de unidades de carga;
- Tote pans. São utilizados para unitizar, transportar e proteger as unidades de carga. Este equipamento tornou-se uma alternativa ao transporte de recipientes de papelão. Quando vazias, estes equipamentos podem ser empilhados uns nos outros, de modo a minimizar a utilização de espaço de ocupação. As dimensões deste equipamento devem ser combinadas com as dimensões dos equipamentos atrás referidos, de modo assegurar a optimização da movimentação de materiais, em veículos.
Movimentação de materiais/Equipamento/Equipamento de contentorização e unitivo/Unificadores
Segundo Tompkins et al. (1996, p. 175), existem outros equipamentos desenvolvidos para facilitar a formação e movimentação de unidades de carga.
A utilização de equipamentos de stretchwrap, shrinkwrap e cintar, asseguram que a composição da unidade de carga não se altere e desagregue, durante a sua movimentação. Os equipamentos de stretchwrap, shrinkwrap e cintar, são utilizados para unitizar a unidade de carga. O shrinkwrapping é a colocação de um saco de plástico, de grandes dimensões, sobre a carga, aplicando, posteriormente, calor e sucção para moldar o plástico à carga. O stretchwrapping envolve uma tela de plástico esticada, em torno da carga e podem ser aplicadas múltiplas camadas, para obter maior grau de segurança, face às condições ambientais (como a chuva, humidade, vento, entre outras) que podem danificar a composição e qualidade da carga. As cintas podem ser de aço, fibras e de materiais plásticos, e são utilizadas para compactar a unidade de carga.
As paletizadoras e despaletizadoras automáticas são utilizadas para empilhar e desconjuntar unidades de carga, respectivamente. As paletizadoras servem para conceber unidades de carga, paletizando os itens provenientes da linha de produção, ou de montagem, em conjunto com equipamentos de armazenagem de cargas (por exemplo: paletes), de acordo com padrões pré-especificados (Taylor, 2009, p. 7-11). Tipicamente, as paletizadores são equipamentos automatizados de alta velocidade, que possuem uma interface de controlo acessível para que os operadores possam facilmente controlar os processos de unitização. Segundo Tompkins et al. (1996, p. 176), as despaletizadoras têm a função de receber unidades de carga e desconjuntar a sua composição.
Movimentação de materiais/Equipamento/Equipamento de movimentação de materiais
Movimentação de materiais/Equipamento/Equipamento de movimentação de materiais/Conveyors
Existem vários tipos de transportadores (também conhecido como Conveyors) para as mais diversas indústrias. Com o passar do tempo existiu e existe uma constante evolução a nível de transportadores, sendo estes melhorados consoante a necessidade e o tipo de matérias a transportar, adaptando os mesmos a diferentes e várias redes de transporte, respeitando sempre as leis, códigos e regulamentos impostos pelas respectivas autoridades legais.
Os transportadores são usualmente utilizados:
- Quando existe uma constante necessidade de mover material entre pontos específicos.
- Para mover materiais ao longo de um caminho fixo.
- Quando existe um volume de fluxo suficiente para justificar o investimento em transportadores.
Os tipos de transportadores são:
Chute conveyors
Belt conveyor
Roller conveyor
Wheel conveyor
Slat Conveyor
Chain Conveyor
Tow Line Conveyor
Trolley Conveyor
Power e Free Conveyor
Cart-on-Track Conveyor
Sorting Conveyor
Movimentação de materiais/Equipamento/Equipamento de movimentação de materiais/Conveyors/Chute conveyors
Os “chute conveyors” são os modelos de transporte de materiais mais simples e também menos dispendiosos, não só no que diz respeito ao material que é utilizado para a sua fabricação mas também se demonstram bastante económicos na sua instalação e na sua manutenção.
São feitos geralmente de tapetes rolantes ou de grades de roletes accionados apenas pela gravidade. São muito utilizados em zonas de carga, pois permitem a acumulação do material a carregar. Utilizados também muito frequentemente em armazéns que demonstrem uma grande movimentação de paletes ou de embalagens, estes são montados como linhas de transporte entre dois pontos distintos e assim verifica-se uma rapidez e eficiência bastante boa no transporte de material. Outra vertente deste sistema é que não tem uma forma específica de transporte, ou seja, pode ser montado de forma a transportar na vertical ou na horizontal.
No transporte vertical o sistema mais usual é em forma de espira, este é desenhado de forma a transportar continuamente embalagens grandes e pequenas sem que estas se esmaguem entre elas ou se empurrem de forma a caírem fora ou dentro da linha de transporte. Este sistema apresenta uma grande capacidade de direccionar as embalagens ou produtos durante o transporte. Outra grande vantagem é a de não ocupar muito espaço horizontal e pode ser uma escolha possível afim de minimizar espaço para o transporte de materiais.
Uma das desvantagens deste sistema de transporte é que é necessária a embalagem do material e por vezes estas tendem a rodar e a tomar diversas direcções durante o seu transporte até a zona de carga, ou seja não existe uma forma específica de direccionar o material embalado afim de no seu destino estar na posição correcta para ser carregado.
Movimentação de materiais/Equipamento/Equipamento de movimentação de materiais/Conveyors/Belt conveyor
Belt conveyor, é como se designa o transporte por correia, que podem ser fabricadas de borracha, plástico, couro ou metal. Usualmente este sistema de transporte de materiais é constituído por uma correia unida a duas roldanas maioritariamente movidas por força mecânica. As duas roldanas rodam no mesmo sentido movendo assim a correia e consequentemente o material a ser transportado. Os produtos ou matérias a transportar são colocados sobre a correia e por meio de energia esta é colocada em movimento efectuando o transporte dos produtos entre dois pontos. Podem ser transportados vários tipos de produtos em forma de embalagem, a granel, ou simplesmente desagregados. (MHIA, [200?]).
Este é um sistema de transporte contínuo, ou seja não existe paragem na movimentação de material, o que requer que exista dois pontos muito distintos, um de partida, e outro de chegada.
A correia é composta por uma ou mais camadas de material tendo em conta os factores e as condições em que vão trabalhar, como o material a transportar ou as condições atmosféricas. Usualmente são compostas por duas camadas. Uma camada inferior para proporcionar tracção entre a correia e as roldanas e uma camada superior devidamente escolhida consoante o material a transportar.
Este sistema pode ser aplicado para transportar material já embalado ou a granel como é visível na indústria de extracção de minérios. Nesta indústria, é muitas vezes necessária a extracção de minério de pontos muito altos ou muito baixos relativamente ao ponto de chegada, o que cria acentuadas inclinações, como tal é necessário existir na camada superior sub-camadas com inclinação contrária suficiente para que o material não escorregue nem saia da linha de transporte ao longo da correia.
Movimentação de materiais/Equipamento/Equipamento de movimentação de materiais/Conveyors/Roller conveyor
Roller Conveyors, como sugere o título é um sistema de transporte por via de rolamentos. Os rolamentos são montados num mesmo eixo e estes eixos são montados sequencialmente criando uma linha de transporte. O material ou produto é transportado devido á rotação dos rolamentos, que é accionada por um motor eléctrico ou pelo simples movimento de empurrar o material ou produto que se encontra na linha de transporte.
As vantagens deste transporte são, revela-se um transporte silencioso, bem como a fácil instalação e manutenção da linha de transporte.
Uma desvantagem deste sistema de transporte é que só deve ser utilizado para diversos materiais e estes têm de corresponder a determinadas formas e tamanhos adequados á linha de transporte. Se o produto a transportar for de tamanho e forma variável é aconselhável utilizar o sistema de transporte por correia.
Consiste numa esteira formada por vários rolos e delimitada lateralmente. Este sistema de transporte é um dos mais utilizados devido à sua simplicidade, diversificação de utilização, podendo ser utilizado para o transporte de vários tipos e formas de produtos.
O sistema de movimentação de materiais por meio de esteiras rolantes é um dos mais populares e produtivos métodos de transporte relativamente a itens simples. Este sistema tem diversos usos dentro das indústrias, assim como no mundo real, bem mais amplo. Existem vários tipos, geralmente baseados na maneira em que são alimentados. Poderiam até ser totalmente sem energia, dado que o sistema por rolos vai ser o mecanismo ideal na utilização de transportadores inclinados, sendo assim um sistema bastante eficaz em levar um item de um nível para outro sem a utilização de energia mecânica ou até mesmo elétrica.
Geralmente os transportadores podem ajudar a salvar uma empresa de elevados custos de horas-homem. A remoção efectiva da exigência física de um trabalhador ao transportar um item de um local para outro pode fazer uma enorme diferença para a produtividade de cada indivíduo. Os transportadores podem muitas vezes oferecer itens para o trabalhador antes de este ainda ter acabado de trabalhar o item anterior com sucesso, diminuindo o tempo de transporte para zero. O transportador por meio de rolos está entre os mais versáteis, sendo possível a escolha das mais diversas opções disponíveis que melhor se adequem ao transporte pretendido.
Os sistemas de transporte por meio de rolos que utilizam somente a gravidade para o transporte de produtos são geralmente os mais fáceis de instalar, desde que exista uma estrutura das próprias instalações adequadas para a utilização e instalação destes mesmos sistemas. Estes não necessitam de instalações eléctricas, exceptuando os casos em que estão ser utilizados como complemento de um sistema de transporte maior que envolva o uso de energia. Caso contrário apenas necessitam de um declive suficiente para garantir o movimento contínuo dos item até ao final da linha de transporte.
Uma vez que estes sistemas são instalados, as indústrias que optam pela utilização destes sistemas irão economizar dinheiro em todos os seus dias de trabalho. O sistema não utiliza formas de combustível, e ainda vai permitir a eliminação da necessidade de funcionários moverem fisicamente os objectos ao longo da linha de transporte. Naturalmente, este será apropriado para aplicar em indústrias que ponderem alternativas aos possíveis sistemas motorizados. Porém em indústrias onde seja necessário transportar objectos sobre uma superfície plana, ou que seja preciso movê-los várias vezes por dia em distâncias bastante longas, este é um sistema de transporte pouco provável de ser o mais adequado.
Sistemas que utilizem meios mecânicos ou eléctricos para o transporte de materias vão envolver as indústrias em custos de exploração e manutenção mais elevados, mas que até se poderiam revelar mais compensadores no que diz respeito ás suas instalações visto que estas são mais fáceis. Considerando que, os sistemas de transporte por meio de rolos que utilizem planos inclinados precisam de instalações especiais dentro de áreas que podem também necessitar de ser modificadas , ao contrário de sistemas elétricos que podem ser montados em praticamente qualquer lugar, é assim necessário que a selecção deste sistema tenha de ser minuciosamnte pensada em todos os aspectos de laboração e instalação, tendo em conta as próprias características das instalações. (Rollerconveyor, [200?]).
Movimentação de materiais/Equipamento/Equipamento de movimentação de materiais/Conveyors/Wheel conveyor
Este sistema é composto por uma série de rolamentos montados sobre o mesmo eixo, onde o espaçamento dos rolamentos é dependente da carga e das dimensões da mesma a ser transportada.
Pode ser accionado por meio da gravidade, o que implica a existência de uma certa inclinação de maneira a que o produto possa, com o seu peso, colocar em movimento rotacional os rolamentos, e consequentemente o seu movimento ao longo da linha de transporte.
É um sistema de transporte muito económico e de fácil manutenção e proporciona um ambiente de trabalho silencioso. As linhas de transporte são de fácil montagem, podendo ser rectas ou com ligeira curvatura. Uma desvantagem é que os produtos têm de obedecer a determinados tamanhos e formas para caberem com alguma folga na linha de transporte.
Os mecanismos de transporte rolante são considerados uma invenção muito útil para o Homem. Estes sistemas de transporte possuem um enorme potencial na medida em que ajudam várias empresas a poupar tempo e dinheiro nas operações do dia-a-dia.
Estes tornaram-se numa tecnologia madura, com diferentes modelos e métodos operacionais desenhados para diferentes usos industriais e aplicações comerciais.Ao escolher-se que tipo de sistema é mais adequado para determinada actividade, é importante ter em consideração o tipo e tamanho de carga a ser transportada, a distância que este terá de percorrer e a que níveis de altura estas operações vão decorrer.
No entanto, em certos casos, o uso do transporte por meio rolante não será o mais eficiente. Por exemplo, no exterior, quando se trata de materiais de construção que precisam de ser transportados a grandes altitudes e distâncias será necessário utilizar um tipo diferente de mecanismo de transporte.
Estas correias de transporte de terra funcionam movendo colunas de baldes na vertical numa estrutura de transporte. Os baldes estão suspensos com folga no sentido de permanecerem na perpendicular em relação ao ângulo da estrutura.
Na maioria das aplicações fabris e de armazéns, o sistema de transporte de rodas irá funcionar melhor. As excepções são quando existe a necessidade de processar objectos em diferentes níveis. A forma mais económica de transportador é a que usa a gravidade para transportar materiais para níveis mais baixos. Estes transportadores apenas serão apropriados para situações em que os materiais irão ser transportados em curtas distâncias e em declives acentuados. Estes podem ser adaptados para uso em superfícies planas ao movimentar manualmente o transportador, mas na maioria das situações é melhor que o transportador seja motorizado.
Em todas as outras situações, algum tipo de transportador de rodas será a melhor forma de movimentar objectos em qualquer distância. Com um transportador de rodas eléctrico, tem-se a opção de se poder criar um sistema tão complexo quanto necessário. Os transportadores de rodas podem ter curvas, leves inclinações, ou até junções permitindo construir uma estrutura complexa. Quaisquer que sejam as necessidades especificas do seu sistema de distribuição, uma construção baseada em transportadores de rodas pode satisfazê-la.
Movimentação de materiais/Equipamento/Equipamento de movimentação de materiais/Conveyors/Slat Conveyor
Slat conveyors, é um sistema de transporte por um filamento de placas (articuladas) na horizontal. O sistema é bastante semelhante ao de transporte por tapetes rolantes, mas com a vertente de ser mais rígido e consequentemente mais resistente ao desgaste e como tal permite o transporte de materiais mais pesados.
Sendo maioritariamente concebidos em placas de aço inoxidável, torna-se mais higiénico pois permite uma lavagem mais eficiente. Por isso é muitas vezes um sistema de eleição para indústrias alimentícias e farmacêuticas. Estas placas também proporcionam um baixo atrito, o que é bastante bom para o transporte de embalagens pois não existe muita força entre a embalagem e o tapete de slats, o que não provoca desgaste na embalagem nem danifica a mesma.
O sistema de transporte por slats é accionado mecanicamente e pode ter velocidade variável, tendo também guias laterais. Normalmente é montado em pernas de tripé o que permite regular a altura de funcionamento. Este sistema tem vários exemplos de aplicação como, aeroportos, indústrias químicas, linhas de montagem.
Os transportadores mecânicos de ripas podem ser usados quando a velocidade e precisão são essenciais. Geralmente são utilizados nas indústrias alimentar, farmacêutica e de processamento e embalamento, mas também podem ser usados para o transporte de produtos pesados.
As ripas são geralmente produzidas com plástico resistente a altas temperaturas ou em aço inoxidável permitindo que seja utilizado em aplicações de secagem a quente. Os transportadores mecânicos de ripas são extremamente fortes e de construção robusta o que lhes confere um desempenho confiável de de longa duração.
Movimentação de materiais/Equipamento/Equipamento de movimentação de materiais/Conveyors/Chain Conveyor
Chain conveyors, é o transporte derivado do uso de correntes, usualmente utilizado para o transporte de cargas muito pesadas. É um transporte contínuo de material que é accionado por meio motor. Este sistema é utilizado em muitos sectores industriais, tais como indústria automóvel. É um sistema bastante resistente ao desgaste, e é assim a escolha possível para indústrias que necessitam de transportar cargas muito pesadas
Os transportadores mecânicos de corrente são uma parte essencial de muitos sistemas de transporte e armazenamento, geralmente são utilizados para a movimentação e distribuição de material em massa. Em geral a maioria dos grãos, flocos e pós de livre fluxo podem ser manuseados com um transportador mecânico de corrente. A selecção do tipo de transportador e da corrente depende das características do material a ser transportado.
Movimentação de materiais/Equipamento/Equipamento de movimentação de materiais/Conveyors/Tow Line Conveyor
Tow Line Conveyor, são sistemas de transporte por reboque. É necessária a utilização de um veículo motorizado ou não, para transportar os materiais ou embalagens.
Um dos exemplos mais frequentes é a utilização de camiões que rebocam semi-reboques. Estes semi-reboques são cheios, convenientemente com as suas dimensões, de material a transportar.
Outro exemplo é o da utilização de porta paletes, estes são utilizados para movimentar dentro de espaços relativamente pequenos, como por exemplo somente dentro do armazém.
É um sistema de transporte não sincronizado, mas bastante flexível visto que não necessita de uma linha de transporte previamente definida.
É uma hipótese bastante viável para espaços pequenos, tendo uma grande acessibilidade este sistema torna-se a longo prazo muito mais barato do que instalar outro sistema existente no mercado.
Movimentação de materiais/Equipamento/Equipamento de movimentação de materiais/Conveyors/Trolley Conveyor
Basicamente é um sistema de transporte por meio aéreo, o produto ou material a transportar é suspenso e transportado.
É necessária a criação prévia de uma linha de transporte bem definida visto que depois é difícil de alterar a mesma. Esta linha é instalada no meio aéreo e é composta por um cabo, corrente ou correia. Ao longo do cabo são instalados sucessivamente ganchos ou ímanes onde o produto ou material a transportar irá ser fixo.
É um sistema que permite economizar o espaço terrestre disponível, contudo permite que o transporte em curvas, subidas e descidas seja facilitado e minimize os danos na mercadoria que possam ocorrer durante o embate das mesmas, e consequentemente reduz o risco de acidentes no local de trabalho.
O seu layout tem de ser minuciosamente bem definido e desenhado, é necessário ter em conta o espaçamento que deve existir entre as cargas a transportar, e também o material a utilizar consoante as características físicas (forma geométrica, peso) do material. Pode ser accionado por meio de gravidade ou por auxílio motorizado.
Movimentação de materiais/Equipamento/Equipamento de movimentação de materiais/Conveyors/Power e Free Conveyor
O termo “power and free” descreve um sistema de transporte que não necessita de uma fonte de energia. Usualmente o material a transportar é movido ao longo de pistas compostas por dois canais, montados abaixo ou adjacentes a uma faixa “i-beam” a partir da qual a cadeia de transporte é suspensa. Este sistema de transporte permite transportar cargas com uma ampla variedade de formas e tamanhos, tais como os seus pesos.
Este sistema de transporte pode encontrar uma vasta gama de aplicações de transporte de materiais do que qualquer outro método de transporte único. Embora seja mais conhecido pelo seu uso em grandes instalações e de fabricação complexa, existem muitas aplicações simples que utilizam as suas funções originais.
Este sistema deve ser considerado para as seguintes aplicações:
Armazéns de existências – em qualquer tipo de estacão de trabalho individual onde seja necessário ser abastecida constantemente, este sistema é uma boa escolha. Um mecanismo de paragem é montado no carril de transporte que irá interromper o transporte na estação de trabalho. O recurso à acumulação dos carros livres permite que as filas de transporte nos postos de trabalho continuem a funcionar sem que seja necessário interromper o movimento de transporte nas outras secções do transportador. Um botão pode ser instalado no posto de trabalho, que o operador irá accionar para largar a carga quando o trabalho estiver completo. Todas as cargas irão automaticamente avançar afim de substituir a carga largada.
Entre processos – este sistema é utilizado quando é necessário acomodar as diferentes taxas de produção entre os diferentes processos de fabricação, permitindo assim manter um caudal constante.
Armazenamento e separação on-line – quando é necessário suspender um trabalho que se encontre em processo ou unidades completas que se encontrem em armazém à espera de serem carregadas, este sistema deve ser uma escolha possível. Os Transportadores podem ser mudados da principal linha de transporte para outra via de armazenamento. Diferentes Centros de Carga – diferentes espaçamentos entre o transporte são muitas vezes requeridos, uma forma eficaz de atingir este objectivo é a utilização deste sistema. Por exemplo, partes que necessitem de ser bem separadas para serem pintadas. Posteriormente as partes devem ser trazidas juntas para os fornos, estas devem vir com um espaçamento que permita cozer o maior número de pecas ao mesmo tempo, por razões de conservação e economia de energia. Este sistema torna tal possível. A velocidade da cadeia também é variável para poder preencher os requisitos dos mais vários processos.
Diferentes velocidades de carga – Se o número de unidades por hora devem ser movidas para estações de produção por onde já passaram e estão em diferentes sítios do layout, esta situação também pode ser resolvida com recurso a este sistema. Os segmentos do sistema que exigirem maiores taxas de produção são servidos por redes de energia que operam a altas velocidades. As transferências entre as cadeias de diferentes velocidades são realizadas com recurso a técnicas de transferência estabelecidas.
Diferentes elevações – Este sistema encontra-se preparado para corresponder a diferentes elevações. Quando o transporte de cargas é ao longo de grandes distâncias, a partir de um local de trabalho para outro, este sistema tem a capacidade para fazer viajar as cargas em níveis bem acima dos postos de trabalho, o que possibilita poupar espaço terrestre. As cargas também podem ser levantadas ou baixadas directamente de um nível para outro por meio de um elevador. Uma aplicação comum é fazer o transporte ao longo de um banho de tinta e posteriormente fazer levantar a carga ao nível da faixa original para esta prosseguir viagem.
Os sistemas “Power & Free” constituem um método simples e robusto para deslocação de materiais em linhas de produção com fluxo constante. Os transportadores consistem basicamente em dois carris posicionados um acima do outro, sendo que pelo carril superior passa um circuito fechado de corrente e pelo trilho inferior se deslocam os carros de carga.
O accionamento do sistema é realizado por uma única motorização, que tracciona a corrente. O deslocamento desta corrente, que possui pequenos arrastadores espaçados de forma constante em seu comprimento, promove o deslocamento dos carros de carga.
Além da robustez, podem ser destacadas como vantagens deste sistema:
- Facilidade de manutenção, principalmente devido à existência de um único motor de accionamento. No caso de circuitos muito grandes ou cargas muito elevadas, pode ser necessária a utilização de motores adicionais traccionando a mesma corrente, porém, sempre serão poucos comparativamente a outros sistemas de transporte;
- Possibilidade de execução de espaços ascendentes com mais de 45˚ de inclinação vertical;
Uma das principais aplicações destes sistemas de transporte é em linhas de pintura, onde devido às características do processo, são necessárias velocidades constantes relativamente baixas, em ambientes agressivos com temperaturas elevadas.
Movimentação de materiais/Equipamento/Equipamento de movimentação de materiais/Conveyors/Cart-on-Track Conveyor
Este sistema de transporte é resumido pela utilização de um carro sobre carris. É definida uma pista entre dois pontos em que o carro de transporte vai circular. No meio dos carris existe um tubo ligado ao carrinho que por acção de rotação irá proporcionar velocidade ao carro de transporte ao longo da pista. O sistema de ligação entre os carros e o tubo é feito por uma roda existente no carro que repousa sobre o tubo e que é utilizada para variar a velocidade do carro (variando o ângulo de contacto entre a roda e o tubo).
Estes carros são independentemente controlados por estes tubos e os mesmos podem ser acumulados ao longo da pista ficando parados quando a roda de contacto entre o carro e o tubo fique paralela ao tubo.
Movimentação de materiais/Equipamento/Equipamento de movimentação de materiais/Conveyors/Sorting Conveyor
Os sistemas de transporte por triagem são utilizados para desviar um determinado produto de uma linha de transporte para outra. Utilizando controlos e transportadores múltiplos de triagem o produto pode ser classificado e desviado para o seu transporte adequado.
Este sistema é projectado para permitir uma separação mais fácil e adequada dos produtos. Os recursos para a separação podem incluir calhas, curvas e rampas.
Usualmente o produto é transportado em ripas ou rolos, maioritariamente feitas em alumínio, ao longo de um trajecto ou pista horizontal em que é instalado num local pré-definido uma calha ou sistema que permita seleccionar e desviar o produto requerido para outra linha de transporte ou armazenagem.
Este desvio pode ser controlado por foto células, leitor de códigos, controladores PLC ou outros métodos de controlo estabelecidos. O sistema de triagem apresenta também a opção de velocidade variável de transporte, permitindo assim, com base nas especificações do produto, mais tempo para a auditoria, inspecção e classificação do produto que se queira desviar. Esta variação da velocidade permite um método rápido e fácil de ajustamento da taxa de alimentação para uma ampla variedade de produtos diferentes.
Movimentação de materiais/Equipamento/Equipamento de movimentação de materiais/Veículos Industriais
Movimentação de materiais/Equipamento/Equipamento de movimentação de materiais/Veículos Industriais/Walking
Um mecanismo utilizado é o carrinho de mão, estes estão divididos em duas categorias. Carrinhos de mão com duas rodas e carrinhos de mão com múltiplas rodas, o tipo da última categoria são aqueles que detêm mais do que duas rodas e são basicamente utilizados para o transporte na horizontal.
Estas unidades são muitas vezes utilizadas em operações que necessitam de transporte por meio de reboque. Dentro destas duas categorias ainda existem muitas outras sub-categorias. Maioritariamente utilizadas em indústrias de manufactura, armazéns, terminais, armazéns comerciais, serviços de entrega entre outras numerosas indústrias.
Outros tipos são especializados para materiais específicos e como tal têm de satisfazer os requisitos, necessidades e comodidade dos mesmos durante o transporte.
Existem factores que determinam e que devem ser considerados para a escolha do tipo de carrinho a escolher.
Carga – massa ou peso da carga a transportar. Peso que o chão pode suportar, este pode ser susceptível a danos durante o transporte. O carrinho também pode ser submetido a um abuso por parte do operador.
Condições do piso – Os carrinhos são mais baratos de serem substituídos do que o chão ou piso. Contudo as rodas dos carrinhos devem ser seleccionadas de forma a minimizar o desgaste do piso onde os carrinhos irão operar ou circular. O uso de rodas de aço ou ferro em certos pisos não é aconselhável podendo ser recorrido ao uso de rodas de borracha.
Condições Globais – Após a análise dos elementos precedentes que deram origem ao problema, deve ser escolhido o modelo mais correcto para a operação de transporte. Antes de encomendar os carrinhos de transporte, o utilizador deve ter em conta as dimensões das portas e do trajecto por onde irá passar. Plantas de fábricas ou armazéns mais antigas podem não satisfazer os requisitos, no que diz respeito a dimensões, dos novos modelos de carrinhos existentes no mercado presente.
Equipamento Suplementar – Os carrinhos de mão industriais foram a origem do transporte de matérias na indústria. A certa altura foi pensado que a eliminação e substituição dos mesmos por equipamentos industriais eléctricos ou mecânicos seria uma opção para aumentar a produtividade. Porém a melhor maneira de tal ser possível é a utilização de ambos em simultâneo ou não. Por esta razão é hoje possível utilizar empilhadores para elevar carrinhos de mão a elevações desejadas, e terminar o movimento de transporte com os carrinhos de mão para veículos de transporte ou para pontos de processamento. Outra situação é a criação de linhas de carrinhos de mão que são dirigidas por rebocadores mecânicos.
Uso Múltiplo – Os carrinhos de mão são maioritariamente desenhados para poderem desempenhar o transporte de materiais com diversas formas geométricas.
Movimentação de materiais/Equipamento/Equipamento de movimentação de materiais/Veículos Industriais/Riding
Movimentação de materiais/Equipamento/Equipamento de movimentação de materiais/Veículos Industriais/Automated
Em geral, este sistema pode ser dividido em três categorias básicas: o sistema padrão com controlos electrónicos básicos, o sistema avançado com microprocessadores ou controlos electrónicos sofisticados, e o sistema com microprocessadores e interface com outros sistemas para possibilitar a total automação do transporte de materiais.
Sistema padrão com controlos electrónicos básicos – Esta classe do sistema é simples no seu conceito e operação. Pode envolver três ou quatro estações de paragem e apenas um ou dois veículos associados a reboques.
Sistema avançado com microprocessadores ou controlos electrónicos sofisticados – Onde um determinado número de veículos é necessário e as linhas são mais longas e as rotas mais complexas. A sua enorme sofisticação permite o uso autónomo e automático de estações de carga/descarga e controlo remoto ou automático dos veículos. Como existem mais controlos a bordo dos veículos este sistema torna-se mais dispendioso. O aumento do número de balizas de bloqueio em zonas do chão, a complexidade da linha de guia, tal como a alimentação da mesma torna todo o sistema mais caro também.
Sistema com microprocessadores e interface com outros sistemas – Criar a ligação entre vários sistemas e sistemas autónomos dentro do mesmo local de trabalho permite e oferece inúmeras vantagens. Contudo o aumento da complexidade do sistema requer mais engenharia, software, e uma despesa adicional no planeamento do sistema mais o custo dos controlos sofisticados.
Movimentação de materiais/Equipamento/Equipamento de movimentação de materiais/Monocarris,Hoists e Gruas
Movimentação de materiais/Equipamento/Equipamento de movimentação de materiais/Monocarris,Hoists e Gruas/Monocarril
Movimentação de materiais/Equipamento/Equipamento de movimentação de materiais/Monocarris,Hoists e Gruas/Hoists
Movimentação de materiais/Equipamento/Equipamento de movimentação de materiais/Monocarris,Hoists e Gruas/Gruas
Movimentação de materiais/Equipamento/Equipamento de armazenagem
Movimentação de materiais/Equipamento/Equipamento de armazenagem/Armazenagem de unidades de carga
Movimentação de materiais/Equipamento/Equipamento de armazenagem/Armazenagem de unidades de carga/Estantes para armazenagem de unidades de carga
Movimentação de materiais/Equipamento/Equipamento de armazenagem/Armazenagem de unidades de carga/Estantes para armazenagem de unidades de carga/Armazenagem por empilhamento
Movimentação de materiais/Equipamento/Equipamento de armazenagem/Armazenagem de unidades de carga/Estantes para armazenagem de unidades de carga/Armação para empilhamento
Movimentação de materiais/Equipamento/Equipamento de armazenagem/Armazenagem de unidades de carga/Estantes para armazenagem de unidades de carga/Estante de profundidade simples
Movimentação de materiais/Equipamento/Equipamento de armazenagem/Armazenagem de unidades de carga/Estantes para armazenagem de unidades de carga/Estante de profundidade dupla
Movimentação de materiais/Equipamento/Equipamento de armazenagem/Armazenagem de unidades de carga/Estantes para armazenagem de unidades de carga/Estante drive-in
Movimentação de materiais/Equipamento/Equipamento de armazenagem/Armazenagem de unidades de carga/Estantes para armazenagem de unidades de carga/Estante drive-thru
Movimentação de materiais/Equipamento/Equipamento de armazenagem/Armazenagem de unidades de carga/Estantes para armazenagem de unidades de carga/Estante dinâmica
Movimentação de materiais/Equipamento/Equipamento de armazenagem/Armazenagem de unidades de carga/Estantes para armazenagem de unidades de carga/Estante push-back
Movimentação de materiais/Equipamento/Equipamento de armazenagem/Armazenagem de unidades de carga/Estantes para armazenagem de unidades de carga/Estante móvel
Movimentação de materiais/Equipamento/Equipamento de armazenagem/Armazenagem de unidades de carga/Estantes para armazenagem de unidades de carga/Estante cantilever
Movimentação de materiais/Equipamento/Equipamento de armazenagem/Armazenagem de unidades de carga/Equipamento para armazenagem de unidades de carga
Etapas de desenvolvimento - 9 fases | ||||||||
---|---|---|---|---|---|---|---|---|
Início: ![]() |
Básico: ![]() |
Criação: ![]() |
Desenvolvimento: ![]() |
Maturação: ![]() |
Revisão: ![]() |
Desenvolvido: ![]() |
Finalização: ![]() |
Abrangente: ![]() |
Os equipamentos para armazenagem ou descarregamento de unidades carga distinguem-se uns dos outros pelo seu preço, grau de automatização, alcance vertical e pela largura de corredor necessária. Os equipamentos com preços mais elevados são lógicamente aqueles que dispõem de maior alcance vertical, que operam em corredores mais estreitos e que oferecem um grau superior de automatização. Esta diferença de preços justifica-se devido à poupança feita em termos de espaço e de mão de obra. Na tabela 2 iremos analisar os vários equipamentos e comparar as suas características (Tompkins et al., 2003, p. 256).
Contrapeso | Straddle | Straddle reach | Lateral | Torre | Híbrido | Automatizado | ||||
---|---|---|---|---|---|---|---|---|---|---|
Custo do equipamento (€) | 30 000 | 35 000 | 40 000 | 75 000 | 95 000 | 125 000 | 200 000 | |||
Capacidade de elevação (m) | 6,7 | 6,4 | 9,1 | 9,1 | 12,2 | 15,2 | 22,9 | |||
Largura do corredor (m) | 3-4 | 2,1-2,7 | 1,8-2,4 | 1,5-2,1 | 1,5-2,1 | 1,5-2,1 | 1,2-1,5 | |||
Peso suportado (ton) | 5 | 3 | 5 | 4 | 4 | 4 | 6 | 4 | 1 | 4 |
Velocidade de elevação(m/s) | 0,4 | 0,3 | 0,25 | 0,25 | 0,4 | 0,3 | 0,5 | |||
Velocidade de cruzeiro (m/s) | 2,8 | 2,4 | 2,5 | 2,2 | 2,5 | 2,5 | 2,5 |
Movimentação de materiais/Equipamento/Equipamento de armazenagem/Armazenagem de unidades de carga/Equipamento para armazenagem de unidades de carga/Operador a pé
Etapas de desenvolvimento - 9 fases | ||||||||
---|---|---|---|---|---|---|---|---|
Início: ![]() |
Básico: ![]() |
Criação: ![]() |
Desenvolvimento: ![]() |
Maturação: ![]() |
Revisão: ![]() |
Desenvolvido: ![]() |
Finalização: ![]() |
Abrangente: ![]() |
A popularidade deste tipo de equipamento para armazenagem de unidades de carga deve-se à sua simplicidade e ao seu baixo custo (Tompkins et al., 2003, p. 233).
Movimentação de materiais/Equipamento/Equipamento de armazenagem/Armazenagem de unidades de carga/Equipamento para armazenagem de unidades de carga/Operador a pé/Porta paletes
Um porta paletes é utilizado para levantar, manobrar e transportar, a curtas distâncias, material em paletes. No que toca à elevação e ao transporte, um porta paletes pode ser completamente manual [2] ou funcionar a bateria [3], de modo a facilitar a tarefa do trabalhador. A capacidade de elevação costuma ser entre 15 a 25 centímetros (Tompkins et al., 2003, p. 234).
Movimentação de materiais/Equipamento/Equipamento de armazenagem/Armazenagem de unidades de carga/Equipamento para armazenagem de unidades de carga/Operador a pé/Empilhadora
Uma empilhadora fornece maior capacidade de elevação que o porta paletes permitindo assim o empilhamento ou armazenamento de unidades de carga em estantes. Existem dois tipos de empilhadores: straddle [4] e reach [5]. O straddle envolve as cargas entre os seus outriggers, enquanto o reach utiliza um pantógrafo ou uma espécie de tesoura para segurar a carga permitindo assim armazenar ou descarregar as cargas das estantes.
Uma empilhadora permite a elevação, empilhamento e transporte, a curtas distâncias, das respectivas paletes. O operador está colocado na parte traseira da empilhadora de modo a conduzi-la a pé. A utilização desta empilhadora é apropriada quando existe uma capacidade de produção baixa, distâncias curtas, altura de armazenagem baixa e quando é procurada uma solução de baixo custo (Tompkins et al., 2003, p. 234).
Movimentação de materiais/Equipamento/Equipamento de armazenagem/Armazenagem de unidades de carga/Equipamento para armazenagem de unidades de carga/Condutor a bordo
Etapas de desenvolvimento - 9 fases | ||||||||
---|---|---|---|---|---|---|---|---|
Início: ![]() |
Básico: ![]() |
Criação: ![]() |
Desenvolvimento: ![]() |
Maturação: ![]() |
Revisão: ![]() |
Desenvolvido: ![]() |
Finalização: ![]() |
Abrangente: ![]() |
Este tipo de equipamento para armazenagem de unidades de carga permite ao operador do veículo conduzir entre locais a distâncias maiores do que no equipamento com o operador a pé. Estes veículos fornecem também uma capacidade superior para suportar peso e maior alcance vertical (Tompkins et al., 2003, p. 235).
Movimentação de materiais/Equipamento/Equipamento de armazenagem/Armazenagem de unidades de carga/Equipamento para armazenagem de unidades de carga/Condutor a bordo/Corredores largos
As empilhadoras de corredores largos operam em corredores com mais de 3,4 metros de largura sendo 3,7 metros a largura padrão para a armazenagem de cargas com a profundidade de 1,2 metros (PIASECKI, 2003).
Movimentação de materiais/Equipamento/Equipamento de armazenagem/Armazenagem de unidades de carga/Equipamento para armazenagem de unidades de carga/Condutor a bordo/Corredores largos/Porta paletes motorizado
O porta paletes motorizado [6] simplesmente eleva a capacidade de transporte de um porta paletes normal. Este veículo pode ser conduzido a pé ou a motor. Normalmente o porta paletes motorizado é utilizado quando não faz sentido percorrer uma certa distância a pé (Tompkins et al., 2003, p. 236).
Movimentação de materiais/Equipamento/Equipamento de armazenagem/Armazenagem de unidades de carga/Equipamento para armazenagem de unidades de carga/Condutor a bordo/Corredores largos/Empilhadora de contrapeso
O «burro de carga» da movimentação de materiais é a empilhadora de contrapeso. Apesar deste ser considerado uma empilhadora de garfos, nem todos os modelos usam garfos para elevar as cargas; aríetes e plataformas também podem ser utilizados para o mesmo efeito. Tal como a maioria das empilhadoras industriais, a de contrapeso pode ser impulsionada a bateria ou por um motor de combustão interna, que pode funcionar a gasolina, propano ou a gasóleo. Os pneumáticos são utilizados nesta empilhadora em operações a céu aberto, enquanto nas operações no interior de edifícios são utilizados pneus cushion. A empilhadora de contrapeso consegue suportar entre 450 a 45 000 kg de carga.
A empilhadora de contrapeso aplica um enorme peso nas suas rodas traseiras para puder suportar as cargas que podem chegar aos 45 000 kg. A capacidade de elevação costuma ser entre 7,6 a 9,1 metros. Este tipo de empilhadora pode não ser apropriada para armazenamento em profundidade dupla.
Tal como a estante de profundidade simples é considerado um modelo de referência das estantes de armazenagem de unidades de carga, a empilhadora de contrapeso pode ser considerada uma referência dos veículos de armazenagem de unidades de carga. A empilhadora de contrapeso é a escolha indicada quando se pretende utilizar o mesmo veículo para carregar ou descarregar camiões e armazenar ou retirar cargas. No caso da armazenagem por empilhamento, estantes drive-in e drive-thru e nas armações para empilhamento, os corredores têm que ser adequados para a empilhadora de contrapeso. A largura necessária destes corredores é entre 3-4 metros para que a empilhadora de contrapeso possa operar, largura que é superior à necessidade das outras empilhadoras. A empilhadora de contrapeso requer corredores mais largos porque para retirar cargas ela tem de efectuar uma viragem. Contudo, a maior vantagem desta empilhadora é o seu baixo custo e a sua flexibilidade.
Para além de garfos existem outras fixações utilizadas para elevar cargas. Estas serão desenvolvidos de seguida.
A principal função da fixação de uma empilhadora é poupar tempo, conservar espaço, reduzir danos no produto, reduzir a mão de obra ou eliminar equipamento desnecessário. O sideshifter [7] permite que os garfos se movimentem de um lado para o outro de modo que o operador possa aceder às paletes sem ter que reposicionar a empilhadora, poupando assim bastante tempo. A fixação push/pull permite que a palete seja substituída por uma folha deslizante. O bloco de cinzas é uma fixação que elimina a necessidade de uma palete, poupa espaço e reduz o peso da carga. Outras fixações que eliminam a necessidade de uma palete são as garras para caixas de cartão, para rolos de papel e a fixação aríete (Tompkins et al., 2003, p. 236).
Movimentação de materiais/Equipamento/Equipamento de armazenagem/Armazenagem de unidades de carga/Equipamento para armazenagem de unidades de carga/Condutor a bordo/Corredores estreitos
Etapas de desenvolvimento - 9 fases | ||||||||
---|---|---|---|---|---|---|---|---|
Início: ![]() |
Básico: ![]() |
Criação: ![]() |
Desenvolvimento: ![]() |
Maturação: ![]() |
Revisão: ![]() |
Desenvolvido: ![]() |
Finalização: ![]() |
Abrangente: ![]() |
As empilhadoras de corredores estreitos operam em corredores com um aproveitamento de espaço muito eficiente, o que significa entre 1,5 a 2,7 metros em termos de largura e entre 7,6 a 18,3 metros em termos de altura (Tompkins et al., 2003, p. 257).
Empilhadora straddle
Empilhadora straddle reach
Empilhadora lateral
Empilhadora de torre
Empilhadora híbrida
Movimentação de materiais/Equipamento/Equipamento de armazenagem/Armazenagem de unidades de carga/Equipamento para armazenagem de unidades de carga/Condutor a bordo/Corredores estreitos/Empilhadora straddle
Normalmente a empilhadora straddle é utilizada quando o espaço do corredor é escasso e/ou excessivamente caro. Esta empilhadora mantém tanto a sua estabilidade como a da carga usando uns outriggers ao nível do pavimento em vez de um sistema de contrapeso, diminuindo assim a largura de corredor necessária para entre 2,1 a 2,7 metros. Para aceder às cargas, os outriggers são conduzidos e colocados debaixo da carga do primeiro nível de modo a permitir que os garfos possam puxar as paletes para fora da estante sem que o veículo perca a sua estabilidade (Tompkins et al., 2003, p. 257).
Movimentação de materiais/Equipamento/Equipamento de armazenagem/Armazenagem de unidades de carga/Equipamento para armazenagem de unidades de carga/Condutor a bordo/Corredores estreitos/Empilhadora straddle reach
A empilhadora straddle reach foi desenvolvida a partir da tradicional empilhadora straddle encurtando os outriggers para aumentar o alcance dos garfos na estante. Ao contrário do anterior, nesta empilhadora já não é necessário colocar os outriggers debaixo da carga do primeiro nível para se poder aceder às cargas.
Existem dois tipos básicos de empilhadoras straddle reach: mastro e garfo. O design mastro-reach consiste num mastro que se move para frente ou para trás ao longo dos outriggers . O design garfo-reach consiste num pantógrafo montado no mastro que se estende para alcançar a carga.
A empilhadora reach duplo é uma variação do design garfo-reach e permite aos garfos um alcance horizontal duplo. Daí que esta empilhadora permita a armazenagem das cargas com profundidade dupla (Tompkins et al., 2003, p. 257).
Movimentação de materiais/Equipamento/Equipamento de armazenagem/Armazenagem de unidades de carga/Equipamento para armazenagem de unidades de carga/Condutor a bordo/Corredores estreitos/Empilhadora lateral
A empilhadora lateral [8] carrega e descarrega as cargas apenas de um lado, eliminando assim a necessidade de efectuar uma viragem para conseguir aceder às cargas. Existem dois designs básicos para empilhadoras laterais. Num design o mastro move-se através de faixas perpendiculares ao veículo, noutro os garfos são projectados de um mastro fixo, através de um pantógrafo [9] , de modo a alcançar as cargas. Os requisitos de largura de corredor são inferiores ás das empilhadoras straddle, i.e. entre 1,5 a 2,1 metros. Estas empilhadoras são guiadas por cabos ou por carris. O alcance vertical pode chegar até 9 metros de altura. A empilhadora lateral tem um particularidade, na medida em que o acesso ao corredor tem de ser feito através da extremidade correcta, tendo em conta de que lado se pretende armazenar/retirar a carga. Vários tipos de cargas podem ser movimentadas com este tipo de empilhadora, apesar dela ser mais adequada para a armazenagem de cargas longas em estantes cantilever (Tompkins et al., 2003, p. 259).
Movimentação de materiais/Equipamento/Equipamento de armazenagem/Armazenagem de unidades de carga/Equipamento para armazenagem de unidades de carga/Condutor a bordo/Corredores estreitos/Empilhadora de torre
Uma empilhadora torre faz parte da nova geração de equipamentos. Este modelo não necessita de efectuar viragens dentro do corredor para armazenar/retirar cargas quer de um lado do corredor quer do outro. Os garfos afixados no mastro podem-se movimentar num ângulo de 180 graus ao longo do mastro. Noutro design é o mastro que roda.
No geral, este tipo de empilhadoras conseguem ter acesso a cargas até 12 metros de altura, o que permite aumentar a densidade de armazenagem em locais onde o espaço de armazém é limitado. Podem operar em corredores de 1,5-2,1 metros de largura (Tompkins et al., 2003, p. 259).
Movimentação de materiais/Equipamento/Equipamento de armazenagem/Armazenagem de unidades de carga/Equipamento para armazenagem de unidades de carga/Condutor a bordo/Corredores estreitos/Empilhadora híbrida
A empilhadora híbrida [10] é igual à empilhadora de torre, com a particularidade de a cabine do operador ser elevada com a carga. Este modelo é uma evolução da máquina de armazenagem/descarga (Storage and retrieval - S/R) utilizada num sistema de armazenagem/descarga automatizado. Ao contrário da máquina S/R, a empilhadora híbrida não está presa a um só corredor, mas sim habilitada a movimentar-se para outros corredores. Os modelos existentes são um pouco desajeitados fora dos corredores, mas dentro deles elas operam com uma elevada taxa de produção.
As empilhadoras híbridas operam em corredores com larguras entre 1,4 a 2,1 metros, permitem armazenamento em estantes até 18 metros de altura sempre com possibilidade de ter uma cabine para o operador, que pode também ser aquecida ou ter ar condicionado. As empilhadoras híbridas sofisticadas movem-se simultâneamente na horizontal e na vertical para acederem às posições das cargas.
As maiores vantagens da utilização deste tipo de empilhadoras é o excelente aproveitamento do espaço e a possibilidade de serem transferidas entre corredores. Por outro lado, as desvantagens são a falta de flexibilidade de reconfiguração, o elevado custo do equipamento e a elevada tolerância dimensional das estantes (Tompkins et al., 2003, p. 261).
Movimentação de materiais/Equipamento/Equipamento de armazenagem/Armazenagem de unidades de carga/Equipamento para armazenagem de unidades de carga/Máquina de armazenamento automática
As máquinas de armazenamento e descarregamento (Storage and Retrieval - S/R) automáticas estão integradas num sistema automatizado de armazenamento e descarregamento (Automated Storage and Retrieval System - AS/RS), onde trabalham com caminhos fixos num ou mais carris em vectores definidos entre as estantes de armazenamento.
Um AS/RS de unidades de carga movimenta normalmente cargas com mais de 450 kg e é utilizado para matéria prima, trabalho em progresso e produtos acabados.
Uma operação típica de um AS/RS pode ser descrita de seguinte maneira: A máquina vai buscar a carga ao local de input/output (I/O), de seguida ela é transportada e depositada numa posição vazia e finalmente a máquina volta vazia para o local de I/O. Esta operação é designada como operação de comando simples. O comando simples só consegue efectuar uma operação por cada visita ao local de I/O, ou seja, armazenar ou retirar uma unidade de carga. Uma operação mais eficiente é a operação de comando dual. Esta operação permite que a máquina para além de ir buscar a carga ao local de I/O depositando-a numa posição desejada, siga de imediato para retirar outra carga de uma posição desejada descarregando-a para o local de I/O. O objectivo principal deste comando é que entre cada visita ao local de I/O seja possível efectuar 2 operações, ou seja, um armazenamento e um descarregamento.
Uma característica única da movimentação da máquina de S/R é o facto de se puder movimentar vertical- e horizontalmente ao mesmo tempo. Daí que o tempo necessário para alcançar a posição desejada na estante seja o máximo entre o tempo horizontal e vertical, dependendo das características das velocidades do equipamento. A velocidade horizontal destes equipamentos pode chegar até 3,0 m/s e a vertical até 0,8 m/s.
No caso de existir uma configuração típica de um AS/RS de unidades de carga, esta seria de armazenagem com profundidade simples, em corredores estreitos (entre 1,2 e 1,5 metros) onde cada corredor contem uma máquina de S/R. O único ponto de I/O estaria situado no nível mais baixo de armazenagem e numa das extremidades do sistema. Contudo, esta configuração raramente tem estes parâmetros constantes. As possíveis variações podem ser a profundidade de armazenagem, o número de máquinas em cada corredor e o número de locais de I/O.
Quando existe pouca variedade de cargas armazenadas no sistema, os requisitos de taxa de produção são elevados e o número de cargas a armazenar é elevado, sendo aconselhável armazenar as cargas em profundidades múltiplas. De seguida vamos analisar algumas configurações alternativas.
Uma configuração alternativa inclui:
- Armazenamento em profundidade dupla com largura de corredor simples. As cargas da mesma SKU são normalmente armazenadas na mesma posição. Uma máquina de S/R alterada é capaz de chegar ás cargas em profundidade dupla.
- Armazenamento em profundidade dupla com largura de corredor dupla. A máquina de S/R consegue carregar duas cargas ao mesmo tempo e armazená-las no cubículo com profundidade dupla.
- Armazenamento em profundidade múltipla com largura de corredor simples. A máquina de S/R armazena material dos dois lados do corredor. Cada fila pode ter até 10 cargas armazenadas. Do lado do output existe uma máquina própria para retirar as cargas da estante. As estantes podem ser dinâmicas, ter inclinação ou correias transportadoras.
- Um sistema de módulo de entrada das prateleiras (Rack entry module - REM) onde o REM entra na estante e coloca/recebe cargas em/de carris especiais da estante.
- Sistemas de garfos-gémeos onde o máquina S/R está equipada com dois garfos e pode mover duas unidades de carga de cada vez.
- Múltiplas máquinas de S/R a operar no mesmo corredor. Apesar de raros, estes sistemas são utilizados para conseguir simultâneamente uma elevada taxa de produção e um bom aproveitamento do espaço.
Outra variação da configuração típica é a utilização de veículos que transportam as máquinas de S/R entre corredores. Estes veículos são utilizados quando os requisitos de armazenamento são elevados em relação aos requisitos de taxa de produção. Nestas situações, não é rentável adquirir máquinas para cada corredor, embora tenha de se ter em conta que o número de corredores deve ser suficiente para os requisitos de armazenagem das cargas.
A terceira variação é o número e o local dos pontos de I/O que variam. Os requisitos da taxa de produção ou as limitações em termos de design das instalações são duas das razões pelas quais existem múltiplos pontos de I/O em outros locais que não os do costume. A utilização de múltiplos pontos de I/O deve-se ao facto de aumentar a taxa de produção ou consequente separação das cargas que entram das que saem. Locais alternativos dos pontos de I/O incluem o tipo de sistema que está na extremidade e no meio da estante (Tompkins et al., 2003, p. 261).
Movimentação de materiais/Equipamento/Equipamento de armazenagem/Equipamento de armazenagem de pequenas cargas
Etapas de desenvolvimento - 9 fases | ||||||||
---|---|---|---|---|---|---|---|---|
Início: ![]() |
Básico: ![]() |
Criação: ![]() |
Desenvolvimento: ![]() |
Maturação: ![]() |
Revisão: ![]() |
Desenvolvido: ![]() |
Finalização: ![]() |
Abrangente: ![]() |
O equipamento de armazenagem de pequenas cargas é classificado como operator to stock se o operador se deslocar até à zona de armazenagem de material e é classificado como stock to operator se o material for transportado mecanicamente até ao operador.
Os vários tipos de equipamento stock to operator proporcionam uma maior produtividade, facilidade na supervisão e maior segurança e protecção dos materiais relativamente ao sistema operator to stock. Ao mesmo tempo, as opções que o sistema stock to operator dispõe são mais caras, mais complicadas de configurar e requerem uma maior manutenção relativamente às opções do sistema operator to stock.
Nos sistemas operator to stock o desenho e selecção do modelo de armazenagem podem ser distintos do projecto e selecção do mecanismo de picking. Por esta razão, os equipamentos de armazenagem operator to stock e os equipamentos de picking podem ser definidos separadamente (Tompkins et al., 2003, p. 264).
Equipamento de armazenagem operator-to-stock
Estantes para caixas
Armários com módulos de gavetas
Estante dinâmica para caixas
Mezanino
Estantes móveis (ou Armazenagem móvel?)
Equipamento de remoção operator-to-stock
Equipamento stock-to-operator
Movimentação de materiais/Equipamento/Equipamento de armazenagem/Equipamento de armazenagem de pequenas cargas/Equipamento de armazenagem operator-to-stock
Etapas de desenvolvimento - 9 fases | ||||||||
---|---|---|---|---|---|---|---|---|
Início: ![]() |
Básico: ![]() |
Criação: ![]() |
Desenvolvimento: ![]() |
Maturação: ![]() |
Revisão: ![]() |
Desenvolvido: ![]() |
Finalização: ![]() |
Abrangente: ![]() |
Os três tipos principais de equipamentos para armazenagem de pequenas cargas, em que o operador se desloca até às existências, são: estantes, armários com módulos de gavetas e estantes de armazenagem dinâmica. Para melhorar o aproveitamento de espaço, cada um destes sistemas de armazenagem pode ser instalado num mezanino ou em estantes móveis (Tompkins et al., 2003, p. 264).
Estante para caixas
Armários com módulos de gavetas
Estante dinâmica para caixas
Mezanino
Estante móvel
Movimentação de materiais/Equipamento/Equipamento de armazenagem/Equipamento de armazenagem de pequenas cargas/Equipamento de armazenagem operator-to-stock/Estante para caixas
A estante para caixas é utilizada para armazenar pequenos produtos e representa um elevado volume de vendas pois está incorporada em vários sistemas. Os custos iniciais, facilmente configurados, instalados e de pequenos custos de manutenção, são a base deste equipamento. Os baixos custos inicias podem não ser os custos efectivos. É também importante recordar que apesar do investimento ser baixo, é possível não estar perante a melhor solução, com as prateleiras, poupança no investimento e manutenção pode significar subaproveitamento de espaço e maior exigência no trabalho.
Na estante para caixa não é habitual o aproveitamento total das dimensões das caixas. A altura das prateleiras é semelhante à altura dos operadores quando estes estão a fazer o picking. Duas consequências da pouca utilização do espaço são:
- O pouco aproveitamento de espaço significa que para armazenar material é necessário mais área.
- Quanto maior a área, maior a distância a percorrer para retirar artigos e por consequências maior o esforço exigido.
Algumas das desvantagens das estantes para caixas dizem respeito ao controlo de problemas e à segurança dos produtos.
Tal como em todos os tipos de equipamento, estas desvantagens têm de ser avaliadas e comparadas com as vantagens para escolher o equipamento apropriado (Tompkins et al., 2003, p. 264-265).
Movimentação de materiais/Equipamento/Equipamento de armazenagem/Equipamento de armazenagem de pequenas cargas/Equipamento de armazenagem operator-to-stock/Armários com módulos de gavetas
Movimentação de materiais/Equipamento/Equipamento de armazenagem/Equipamento de armazenagem de pequenas cargas/Equipamento de armazenagem operator-to-stock/Estante dinâmica para caixas
A estante dinâmica para caixas é outro equipamento popular do tipo operator to stock. A armazenagem em estantes dinâmicas é usada normalmente para artigos que são armazenados em embalagens de tamanho e forma apropriados. As caixas são repostas nas traseiras das estantes no corredor de reposição e avançam/deslizam para substituir o espaço vazio deixado pelas embalagens que se encontravam na frente. Este movimento de trás para a frente assegura o sistema FIFO (first in, first out) do material.
O arrumo em estantes não é mais do que o sistema de prateleiras com rolos e com um determinado ângulo para fazer deslizar os materiais. Quanto mais profundas as secções, maior é o espaço dedicado à armazenagem em oposição ao espaço no corredor. A obtenção de espaço pode ser alcançada aproveitando o espaço acima da armazenagem em estantes dinâmicas para armazenagem de paletes.
Os custos da armazenagem por gravidade em estantes dependem da capacidade de suportar o peso e do comprimento das estantes. Idêntico ao sistema de estantes para caixas, a armazenagem em estantes dinâmicas para caixas tem um baixo custo de manutenção e encontra-se disponível em vários tamanhos e variedades de secção, de uma lista de vários fornecedores.
O facto de apenas uma embalagem de cada coluna de artigos estar localizada à frente, significa que um grande número de artigos são apresentados ao funcionário numa pequena área. Portanto, as deslocações e as exigências de mão de obra podem ser reduzidas com a implementação de um layout eficiente (Tompkins et al., 2003, p. 267-268).
Movimentação de materiais/Equipamento/Equipamento de armazenagem/Equipamento de armazenagem de pequenas cargas/Equipamento de armazenagem operator-to-stock/Mezanino
A estante para caixas, os armários com módulos de gavetas e os sistemas de carrósseis podem ser instalados em mezaninos.
A vantagem do uso de um mezanino é que se pode processar aproximadamente o dobro do material que se conseguiria sem o mesmo, no mesmo espaço e a baixo custo.
Os principais aspectos que devem ser analisados na construção de um mezanino são a adequação à carga a que irá ser sujeito, as características do projecto do sistema de movimentação de materiais que serve o nível superior do mezanino e a utilização do pé-direito disponível. A altura mínima necessária para se construír um mezanino é de 4,26 metros (Tompkins et al., 2003, p. 268).